|
Jul 12, 2025
|
|
|
|
2022-2023 College Catalog [ARCHIVED CATALOG]
|
ENG 211IN - Computer Aided Engineering Design and Manufacturing 3 Credits, 1 lecture period 6 lab periods
Introduction to engineering graphics, concepts of engineering design and manufacturing processes. Includes sketching, manual drafting, dimensioning practices and tolerances, drafting standards, computer-aided design three-dimensional (3D) parts and assembly modeling, CAD/CAM in manufacturing processes, introduction to additive manufacturing.
Prerequisite(s): MAT 189
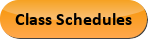
Course Learning Outcomes
- Demonstrate ability to read and interpret engineering and manufacturing drawings.
- Generate components and assembly drawings using 3D parametric modeling software.
- Demonstrate correct usage of ANSI and ASME drafting standards in engineering/manufacturing drawings, including geometric dimensioning and tolerancing.
- Demonstrate knowledge of the computer numerical control machining.
- Demonstrate ability in applying CAD/CAM software to product design and program manufacturing processes.
- Exhibit knowledge to generate code for a different numerical control machines.
Performance Objectives:
- Demonstrate the fundamental concepts and principles of engineering graphics as a language.
- Generate hand-drawn multi-view technical sketches.
- Apply methods of orthographic projection to produce detail.
- Demonstrate the fundamental concepts and principles of the computer-aided design (CAD) system.
- Demonstrate the ability to read engineering drawings.
- Construct three-dimensional (3D) solid models on a modern CAD system:
- Create 3D solid models of complex objects given a multi-view representation
- Create solid models of individual parts
- Create reference geometry features (planes, axes)
- Measure properties of 3D CAD models
- Create multi-view, auxiliary and section drawings from 3D solid models:
- Use the principal planes of projection and the principal views
- Create hidden lines, center lines, etc. based on graphics conventions
- Create multi-view drawings from 3D solid models on a CAD system
- Represent typical features: e.g. holes, threads, chamfers, and fillets
- Create auxiliary views automatically from 3D solid models
- Generate appropriate section views
- Create dimensioned drawings from 3D solid models:
- Understand the basic terminology and geometrical relationships associated with dimensioning practice
- Demonstrate size, location, and coordinate dimensioning
- Create dimensioned drawings from 3D solid models
- Create complete working drawings including assembly and detailed drawings for a “real-life” object
- Apply geometric dimensioning and tolerancing (GD&T):
- Understanding and practical proficiency in dimensioning and tolerancing.
- Recognize GD&T dimensioning on an engineering drawing
- Determine maximum material condition (MMC) and its implications
- Calculate bonus tolerance allowances as features deviate from MMC
- Recognize and specify GD&T datums
- Visualize tolerance zones as specified in GD&T
- Create GD&T control features on an engineering drawing
- Apply CAD/CAM software to product design and program manufacturing processes
- Describe numerical control (NC) and computer numerical control (CNC) machine systems
- Identify NC/CNC components and control systems
- Demonstrate the correct CNC programming sequences
- Develop a program flowchart and process planning
- Demonstrate knowledge of absolute and incremental positioning
- Understand CAM environment
- Identify CAM icons
- Identify different screen areas within CAM environment
- Identify menu bars and program’s essential functions
- Create geometry using CAD/CAM software
- Identify geometry features : arc, lines, radius
- Identify geometry functions : moving, copying, mirroring
- Demonstrate the ability to create geometry using proper techniques appropriate for multi-axis tool pathing
- Demonstrate knowledge to select the best geometry creation technique for the part features to be machined
- Demonstrate knowledge to use ‘operating manager’ with toolpaths
- Determine proper tool path for material removal
- Demonstrate the ability to select proper tooling from tool library
- Demonstrate the ability to select proper speeds and feeds for tool motion based on machine limits and set up
- Exhibit knowledge to generate code for a different numerical control machines
- Understand coding for a different machining centers
- Understand coding a process model
- Understand principles of Additive Manufacturing
- Demonstrate knowledge of production methods and production materials
- Demonstrate the ability to apply design principles
- Analyze advantages and disadvantages of additive and subtractive manufacturing
Outline:
- Sketching and manual drafting; Reading and interpreting drawings
- Free-hand sketching techniques
- Manual drafting techniques
- Manual drafting tools
- Orthographic projections
- Isometric sketches
- Oblique sketches
- Perspective sketches
- Section views
- Auxiliary views
- Details views
- Reading and interpreting engineering drawings
- Dimensioning practices and Tolerances; Drafting standards
- Dimensioning systems
- Unidirectional
- Aligned
- Tabular
- Arrowless
- Chart drawing
- Dimensioning fundamentals
- Dimension line spacing
- Chain dimensioning
- Datum dimensioning
- Preferred dimensioning practices
- Dimensioning angles
- Dimensioning a simple hole
- Dimensioning chamfers
- Dimensioning cylinders and conical shapes
- Dimensioning arcs
- Representing and dimensioning for external and internal threads
- Dimensioning countersink and counterbore holes
- Tolerancing conventions; Geometric and position tolerancing
- Direct tolerancing methods
- Tolerance expressions
- Angular tolerances
- Standard fits
- Tolerances of form
- Tolerances of orientation
- Positional tolerances
- ANSI and ASME drafting standards
- Computer-Aided Design (CAD)
- Introduction to parametric modeling
- Introduction to CAD systems (AutoCAD, SolidWorks, Autodesk Inventor)
- Basic two-dimensional (2D) drawing skills
- Basic commands
- File management
- Command Manager and Feature Manager
- Parts and Assembly Modeling
- Basic parts modeling
- Basic and complex 2D model design
- Three-dimensional (3D) modeling
- Basic part modeling
- Basic tools extrude, cut, hole, mirror, edit part modeling, etc.
- Revolved features
- Swept, Loft and additional features
- Three-Dimensional (3D) Assembly Modeling
- Bottom-up assembly modeling approach
- Linear and rotational motion
- Assembly-exploded view
- Part drawing from 3D models
- Configuration in SolidWorks
- Overview of SolidWorks modules (sheet designer, weldments, pipes, etc.)
- CAD data management in a corporate environment
- Product data management system
- Data vault principles
- Data version control
- Basics of Numerical Control (NC) and Computer Numerical Control (CNC) Machining Systems
- Description of NC/CNC machinery
- Objectives and application of NC/CNC
- Components and control systems
- Tool changers, tool storage, and special tooling/fixturing
- Positioning and Coordinate Systems used in NC/CNC Programming
- Absolute and incremental positioning
- The order of operations and documentation needed for programming
- Developing a program flowchart and process planning
- Importance of program documentation
- Fundamentals of G-code programming
- Introduction to a CAM Environment
- Main menu
- Overview of CAM icons
- Explanation of different screen areas within a CAM environment
- Explanation of menu bars and their uses
- Creating Geometry
- Arc, lines, radius
- Transforming geometry
- Moving
- Copying
- Rotating
- Mirroring
- Operating Manager
- Drilling, contour, pocketing, islands, and surfaces
- Get tool from library
- Selecting tool parameters
- Viewing tool path
- Code Generation for CNC
- Coding a process model
- Coding for different machining centers
- Introduction to additive manufacturing
- Additive manufacturing methods
- Production methods
- Production materials
- Design principles
- Alternative prototyping methods
- Injection mold prototyping
- Custom made machined parts
- Cost versus time saving
- Additive vs subtractive manufacturing (pros and cons)
|
|