|
2022-2023 College Catalog [ARCHIVED CATALOG]
Course Descriptions
|
|
Legend for Courses
HC/HN: Honors Course IN/IH: Integrated lecture/lab LB: Lab LC: Clinical Lab LS: Skills Lab WK: Co-op Work
SUN#: is a prefix and number assigned to certain courses that represent course equivalency at all Arizona community colleges and the three public universities. Learn more at www.aztransfer.com/sun.
|
|
Welding |
|
-
WLD 110 - Basic Arc and Oxyacetylene Welding 4 Credits, 6 Contact Hours 2 lecture periods 4 lab periods
Procedures and techniques in arc and oxyacetylene welding. Includes health, safety, and environmental practices, welding terminology, arc and oxyacetylene welding equipment, proper welding procedures for arc and oxyacetylene, arc and oxyacetylene steel welding, welding machines and polarities, filler metal identification, and welding positions, and oxyacetylene cutting.
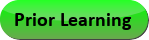.png)
Course Learning Outcomes
- Demonstrate all safety protocol
- Describe the welding machines and polarities used in the arc welding process.
- Demonstrate welding in flat and horizontal positions used in the arc and oxyacetylene welding processes.
- Demonstrate hand and track torch techniques for oxyacetylene cutting.
Outline:
- Health, Safety, and Environmental Practices
- Eye protection
- Protective clothing
- Equipment handling
- Safety features to welding processes
- Shop clean-up procedures
- Occupational Safety and Health Administration (OSHA) regulations
- Ventilation requirements
- Waste disposal
- Material Safety Data Sheets (MSDS)
- Welding Terminology
- Definitions
- Applications
- Arc and Oxyacetylene Welding Equipment
- Identification
- Proper handling
- Assembly
- Types of gases
- Handling of cylinders
- Types of regulators
- Hose size and safety features
- Torch handling and types
- Arc welding helmets and lenses
- Power tools
- Proper Welding Procedures for Arc and Oxyacetylene
- Electrode size
- Amperage settings
- Arc length
- Speed of travel
- Electrode angle
- Flame adjustment
- Tip size
- Torch angle
- Arc and Oxyacetylene Steel Welding
- Definition
- Application
- Processes
- Regulator pressure settings
- Lighting the torch
- Flame adjustment
- Clamping and tacking procedures
- Welding Machines and Polarities
- Alternating Current (AC) machines
- Direct Current (DC) machines
- Polarities
- AC current
- DC current
- Filler Metal Identification
- Digit selection
- Types of electrodes
- E6010
- E6011
- E7018
- E7024
- Identification of gas welding rods
- Application
- Welding Positions
- Flat
- Vertical
- Horizontal
- Overhead
- Oxyacetylene Cutting
- Hand cutting torch
- Lighting
- Flame adjustment
- Procedures
- Track torch
- Lighting
- Flame adjustment
- Procedures
|
|
-
WLD 115 - Blueprint Reading/Estimating 4 Credits, 4 Contact Hours 4 lecture periods 0 lab periods
Principles and procedures for interpreting structural blueprints and determining materials and labor costs. Includes fundamentals of blueprint reading, welding print format and types of fabrication blueprints, welding symbols and sizes, structural shapes and symbols, and blueprint interpretation. Also includes introduction to estimating, bonds and insurance, materials specifications, labor, structural steel systems, and steel fabrication checklist.
Prerequisite(s): Within the last three years: MAT 089A through Module 10, or ICS 081 , or required score on the Mathematics assessment test.
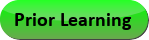.png)
Course Learning Outcomes
- Interpret the types of welding symbols used on blueprints and the significance of each element.
- Interpret detail drawings, assembly prints, and subassembly prints.
- Describe general and subcontractor building construction estimating procedures.
- Identify the types of structural steel systems on retail buildings.
Outline:
- Introduction
- Personal form and class schedule
- Evaluation procedures
- Course content
- Fundamentals of Blueprint Reading
- Basic lines
- Basic views
- Sketching
- Notes and specifications
- Dimensions and methods
- Limits and tolerances
- Units of measurement
- Radius and arc dimensions
- Scale sizes
- Preparation of bill of materials
- Welding Print Format and Types of Fabrication Blueprints
- Structural shapes
- Size specifications for structural shapes
- Conventional breaks
- Auxiliary views
- Partial views
- Detail views
- Section views
- Detail and assembly prints
- General abbreviations and structural and symbols
- Welding Symbols and Sizes
- Basic welding symbols
- Types of welds
- Location of welds
- Combined weld and welding symbols
- Weld sizes
- Weld strengths
- Weld designs
- Weld contour
- Welding abbreviations
- Joint designs
- Structural Shapes and Symbols
- Identification of structural steel
- Nominal and basic sizes
- Structural steel symbols
- Threaded fasteners
- Blueprint Interpretation
- Detail drawings
- Assembly prints
- Subassembly prints
- Introduction to Estimating
- Building construction estimating
- General contractors
- Subcontractors
- Material suppliers
- Bonds and Insurance
- Surety bonds
- Statutory bonds
- Nonstatutory bonds
- Bid bond
- Performance bond
- Labor and material bond
- Worker’s compensation insurance
- Builder’s risk fire insurance
- Materials Specifications
- Description of materials
- Construction systems
- Workmanship
- Invitation to bid
- Instructions to bidders
- Labor
- Wages and rules
- Field reports
- Pricing labor
- Structural Steel Systems
- Structural steel specifications
- Structural steel framing
- Steel Fabrication Checklist
- Steel shapes
- Engineering (fabrication, drawings, inspection)
- Installation (welding, bolting, etc.)
- Miscellaneous (chips, anchor bolts, ties)
|
|
-
WLD 120 - Welding for Metal Sculpture 4 Credits, 6 Contact Hours 2 lecture periods 4 lab periods
Basic welding techniques and processes used in metal sculpture design and fabrication. Includes oxyacetylene safety practice, oxyacetylene equipment handling, oxyacetylene welding procedures, assembly of portable equipment, oxyacetylene cutting and design, and oxyacetylene bronze build-up. Also includes arc welding safety practices, arc welding procedures, basic joint design, currents and polarities, arc welding machines and electrodes, and arc designing for sculpture.
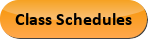
Course Learning Outcomes
- Demonstrate all safety protocol
- Design an original metal sculpture with appropriate welding processes
Outline:
- Oxyacetylene Safety Practice
- Fires
- Burns
- Eye injuries
- Explosions
- Fumes
- Oxyacetylene Equipment Handling
- Cylinders
- Pressures
- Safety devices
- Gases
- Types
- Safety
- Regulators
- Torches
- Tips
- Filler rods
- Oxyacetylene Welding Procedures
- Pressure settings
- Tip size
- Flame adjustments
- Torch angle
- Filler rod and flame manipulation
- Travel speed
- Assembly of Portable Equipment
- Secure cylinders
- Crack cylinder valves
- Attach regulators and hoses
- Check regulator adjustment screw
- Open cylinder valves
- Set working pressures
- Oxyacetylene Cutting Design
- Cutting shapes
- Preparation
- Weldability
- Desgin for abstract sculpture
- Oxyacetylene Bronze Buildup
- Light bronze welding to create three dimensional forms and texture
- Texture design
- Arc Welding Procedures Safety Practices
- Fires
- Burns
- Eye injuries
- Electric shock
- Radiation
- Arc Welding Procedures
- Current settings
- Arc length
- Electrode angle
- Travel speed
- Electrode size
- Basic Joint Design
- Identification
- Preparation
- Weldability
- Currents and Polarities
- Direct current
- Reverse polarity
- Straight polarity
- Alternating current
- Arc Welding Machines and Electrodes
- Generator
- Transformer D.C. and A. C.
- Transformer A.C. only
- Classification
- Sizes
- Fluxes and their purpose
- Arc Designing for Sculpture
- Preparation
- Weldability
- Design for abstract sculpture
|
|
-
WLD 160 - Arc Welding 4 Credits, 6 Contact Hours 2 lecture periods 4 lab periods
Principles and techniques of joining metals with an electric arc as the source. Includes arc welding uses, safety, techniques, flame cutting, joint design, welding costs, electric currents and power sources, carbon arc cutting, filler metal selection, hardfacing, and metal identification.
Prerequisite(s): WLD 110 Information: Prerequisite may be waived with appropriate work experience or course work. See a welding instructor or advisor for prerequisite information.
Course Learning Outcomes
- Demonstrate all safety protocol
- Describe effects of root opening, bevel angle, and reinforcement
- Describe hard facing techniques, preparation, and electrode selection.
- Describe identification methods on ferrous and non-ferrous metals and steel alloys
- Demonstrate welding competency by completing an American Welding Society D1.1 Structural certification test.
Outline:
- Introduction to Arc Welding
- Welding defined
- Uses of welding
- Welding processes
- Occupational opportunities in welding
- Training for welding occupations
- Safety in Arc Welding
- Burns
- Eye and ear protection
- Respiratory protection
- Ventilation
- Electrical safety
- General work clothing
- Cylinder safety
- Fire protection
- Work area
- Hand and power tools
- Basic and Intermediate Arc Welding Techniques
- Striking the arc
- Effect of too high or too low current setting
- Electrode size and current setting
- Arc length
- Electrode angle
- Electrode travel
- Stringer beads
- Weld bead placement
- Oxyacetylene Flame Cutting
- Safety in cutting
- Pressure regulators
- Cylinder valves
- Cutting torches
- Cutting tips
- Check valves
- Hoses and fittings
- Flashbacks and backfires
- Types of flames
- Leak detection
- Manifold systems
- Cutting techniques
- Arc Welding Terminology
- Arc welding terms
- Arc welding definitions
- Welding Joint Design
- Forces on a weld
- Types of weld joints
- Weld joint design
- Edge preparation
- Joint dimensions
- Welding Costs
- Minimum root opening
- Minimum bevel angle
- Minimum reinforcement
- Out of Position Arc Welding
- Vertical position welding, all joints with E6010, E7018 electrodes
- Overhead position welding, all joint with E6010, E7018 electrodes
- Horizontal position welding, butt joint, with E6010, E7018 electrodes
- Electric Currents for Arc Welding
- Electric currents
- Arc temperature
- Direct current
- Alternating current
- Polarities
- Welding Power Sources
- Generator power source
- Transformer/rectifier power source
- Transformer power source
- Air Carbon Arc Cutting
- Carbon arc cutting safety
- Air carbon arc cutting
- Torch design
- Carbon electrodes
- Power source
- Air supply
- Application process
- Filler Metal Selection
- American Welding Society (A.W.S.) filler metal classification
- Electrode coatings
- Electrode sizes
- Types of electrodes
- Electric currents vs. electrode type
- Electrode metal transfers
- Hard Facing
- Process
- Preparation
- Techniques
- Electrode selection
- Basic Metal Identification
- Five basic test methods
- Ferrous and non-ferrous metals
- Steel alloys
- Steel numbering system
|
|
-
WLD 250 - Pipe Welding 4 Credits, 6 Contact Hours 2 lecture periods 4 lab periods
Principles and techniques of pipe welding. Includes introduction to pipe layout and drawing equipment. Also includes an introduction to performance testing, types of pipe, methods and preparation of pipe joints and miter joints, methods of joining pipe and miter joints.
Prerequisite(s): WLD 160 Information: Prerequisite(s) may be waived with appropriate work experience. See a welding instructor or advisor for prerequisite information.
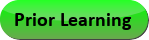.png)
Course Learning Outcomes
- Describe processes, standards and codes for performance testing.
- Describe types of pipe, pipe standards and codes.
- Explain the what, where, how, and why of pattern layout for pipe fabrication.
- Use drawing equipment required for pattern layout.
- Setup and draw connections for pipe.
- Cut and bevel pipe using the freehand and machine techniques.
- Demonstrate methods of joining pipe in vertical, horizontal and 45° fixed positions.
- Demonstrate coping and mitering procedures.
- Demonstrate fit-up, tacking and welding procedures.
Outline:
- Introduction to Performance Testing
- Processes
- Standards and codes
- Organizations
- Classifications
- American Welding Society qualifications codes
- American Petroleum Institute qualification codes
- American Society of Mechanical Engineers qualification codes
- Types of Pipe
- Schedules of pipe
- Steel alloy pipe
- Pipe standards and codes
- Introduction to Pipe Layout
- What is pattern layout?
- Where is it used?
- How is it used?
- Why is it used?
- Drawing Equipment
- Drawing board
- T-Square
- Triangles
- Scale
- Dividers
- Compass
- Bow spacers
- Pencils
- Pipe to Pipe
- Miters
- Copes
- Methods and Preparation of Pipe Joints and Miter Joints
- Butt joint
- Tee joint 90°
- Branch joint
- Bevel angles
- Set up of pipe test
- Methods of Joining Pipe and Miter Joints
- Layout
- Tacking procedures
- Welding procedures
- Selection of filler rods
- All positions
- Preparation of Pipe Test
- Bevel angle
- Set up of test plate for end test
- Set up of test plate for x-ray test
- Cutting test coupons for bend test
- Methods of Welding Pipe Test
- Tacking procedures
- Welding procedures
- Finishing methods
- Selection of filler rods
- All position procedures and techniques
- Bend tests
|
|
-
WLD 261 - Gas Metal Arc Welding 4 Credits, 6 Contact Hours 2 lecture periods 4 lab periods
Procedures and techniques in Gas Metal Arc Welding (GMAW) and Flux Core Arc Welding (FCAW) processes. Includes health, safety, and environmental practices; welding terminology, GMAW and FCAW processes and equipment. Also includes equipment operation, welding techniques, power source and wire feed types and controls; welding currents and polarities; welding wires in GMAW and FCAW processes; shielding gases; and mild steel and aluminum welding.
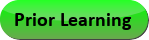.png)
Course Learning Outcomes
- Demonstrate all safety protocol.
- Demonstrate mild steel welding.
- Demonstrate aluminum welding.
Outline:
- Health, Safety, and Environmental Practices
- Personal, body, and eye protection
- Protective clothing
- Equipment handling safety
- Safety features to GMAW and FCAW processes
- Occupational Safety and Health Administration (OSHA) regulation
- Welding Terminology
- Dictionary of welding terms
- GMAW and FCAW applications
- GMAW and FCAW Processes and Equipment
- Process of operations
- GMAW and FCAW parameters and variables
- Power sources
- Wire feeders
- Welding guns
- Shielding gases
- Gas regulators
- Welding wires
- Equipment Operation and Welding Techniques
- Assembly of the GMAW and FCAW equipment
- Starting the weld bead
- Metal Inert Gas (MIG) gun angles
- Oscillating the gun
- Travel speed
- Forehand and backhand techniques
- Power Source and Wire Feed Types and Controls
- Types of power sources
- Types of wire feeders
- Manual power source and wire feed controls
- Amperage control
- Voltage control
- Inductance control
- Slope control
- Polarity control
- Wire feed control
- Welding Currents and Polarities
- Types of welding currents and their uses
- Types of polarities in the current and their uses
- Welding Wires in GMAW and FCAW Processes
- Types and sizes of welding wire used in GMAW and FCAW processes
- Care of the welding wire
- Selecting the correct welding wire
- Shielding Gases
- Types of shielding gases used for different types of basemetal welding
- Characteristics of the different types of shielding gases
- Mild Steel Welding
- Basemetal preparation and identification
- Welding procedures and position welding techniques
- Aluminum Welding
- Basemetal preparation and identification
- Welding procedures and position welding techniques
|
|
-
WLD 262 - Gas Tungsten Arc Welding 4 Credits, 6 Contact Hours 2 lecture periods 4 lab periods
Procedures and techniques in the Gas Tungsten Arc Welding (GTAW) process. Includes health, safety, and environmental practices; welding terminology, GTAW process and equipment, equipment operation and techniques. Also includes power source types and controls, welding currents and polarities, tungsten electrodes, shielding gases, mild steel welding, aluminum welding, stainless steel welding, and GTAW certification.
Prerequisite(s): WLD 110
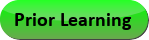.png)
Course Learning Outcomes
- Demonstrate all safety protocol.
- Demonstrate mild steel welding.
- Demonstrate aluminum welding.
- Demonstrate stainless steel welding.
Outline:
- Health, Safety, and Environmental Practices
- Eye Protection
- Protective clothing
- Equipment handling
- Safety features to GTAW process
- Occupational Safety and Health Administration (OSHA) regulations
- Welding Terminology
- Dictionary of welding terms
- Applications
- GTAW Process and Equipment
- Process of operation
- GTAW parameters and variables
- Power sources
- Types of foot pedals
- Welding torches
- Gas regulators
- Equipment Operation and Techniques
- Assembly of the GTAW equipment
- Starting the arc
- Torch angles
- Oscillating the torch
- Adding the filler rod
- Speed of travel
- Power Source Types and Controls
- Types of power sources
- Manual power source controls on panel
- Polarity control
- Amperage control
- Welding Currents and Polarities
- Types of welding currents and their uses
- Types of polarities in the current and their uses
- Tungsten Electrodes
- Types and sizes of tungsten electrodes used in welding projects
- Care of the tungsten electrode
- Shielding Gases
- Types of shielding gases used in different types of basemetal welding
- Characteristics of the shielding gases
- Mild Steel Welding
- Basemetal preparations
- Welding procedures and techniques
- Flat, vertical, and horizontal positions
- Aluminum Welding
- Basemetal preparations
- Welding procedures and techniques
- Flat, vertical, and horizontal positions
- Stainless Steel Welding
- Basemetal preparations
- Welding procedures and techniques
- Flat, vertical, and horizontal positions
- GTAW Certification
- Types of GTAW certifications
- GTAW codes and specifications
|
|
-
WLD 263 - Layout and Fabrication Welding 4 Credits, 6 Contact Hours 2 lecture periods 4 lab periods
Principles and techniques of steel layout and fabrication welding. Includes measurement, print reading review, layout tools, layout techniques, hand-held power tool safety and use, large power tool safety and use, drawing interpretation, structural methods, and welding projects.
Prerequisite(s): WLD 115 , WLD 261 and GTM 105 (or placement into MAT 092 or higher). Recommendation: Completion of WLD 160 before enrolling in this course. If any recommended course is taken, see a financial aid or Veteran’s Affairs advisor to determine funding eligibility as appropriate. Information: Prerequisites may be waived for appropriate work experience. See a welding instructor or advisor for prerequisite information.
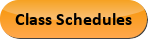
Course Learning Outcomes
- Demonstrate the ability to perform several measuring procedures.
- Demonstrate the ability to read blueprints.
- Setup and draw connections for channel.
- Setup and draw sheet metal layout.
- Setup and draw connections for I-Beams.
- Demonstrate the use of varies layout tools.
- Demonstrate layout techniques and sequencing for completion of fabrication project.
- Demonstrate safety in the use of hand-held power tools.
- Demonstrate safety in the use of large power and hydraulic tools.
- Interpret shop drawings.
- Demonstrate coping and mitering procedures for varies structural materials.
- Demonstrate fit-up, tacking and welding procedures for varies structural connections.
- Demonstrate the ability to build projects from shop drawings.
Outline:
- Measurement
- Linear
- Angular
- Four-sided
- Triangular
- Circular
- Print Reading Review
- Types of drawings
- Types of lines used on a drawing
- Using a working drawing
- Drawings made to a scale
- Basic weld joints
- Welding symbol
- Weld symbol
- Layout Tools
- Squares
- Rap-a-rounds
- Center punches
- Stair nuts
- Scribes/metal markers
- Jigs and fixtures
- Protractors
- Dividers
- Layout Techniques
- Layout from one end
- Layout from two sides of square or rectangle
- Compound errors
- Gages
- Planning sequences
- Tacking; How and Where
- Welding sequences
- Distortion control
- Hand-Held Power Tool Safety and Use
- Angle grinders
- Drills
- Reciprocating saw
- Port-a-band
- Large Power Tool Safety and Use
- Pedestal grinder
- Horizontal band saw
- Iron worker
- Drawing Interpretation
- Material identification
- Basic (i.e. base plates and flag plates) to stair layout
- Preparation of Structural members
- Structural identification
- Beam coping and beveling
- Angle iron copes and miters
- Channel copes and miters
- Welding Projects
- Student generated
- Instructor generated
- Structural member connections
- I-Beams
- Same size beams
- Different size beams
- Angle to beam
- Channel to beam
- Beam squares
- Channel to Channel
- Miters
- Copes
- Structural Members
- Fit-up
- Tack
- Weld
- Sheet Metal Layout
- Material usage
- Develop stretch out
- Simple transitions
|
|
-
WLD 264 - Introduction to CNC Plasma Arc and Basic Robotic Welding 4 Credits, 6 Contact Hours 2 lecture periods 4 lab periods
Procedures and techniques in Computer Numerical Control (CNC) plasma arc cutting and robotic automated welding. Includes health, safety, and environmental practices; history of plasma arc cutting; software and coordinate systems; tool paths, importing images, and cutting with a CNC plasma machine. Also includes programming and operation procedures for Gas Metal Arc Welding (GMAW) process using a Fanuc R30iA robotics welding cell, Teach Pendent Programs (TPP), and maintenance.
Prerequisite(s): CAD 101 or CAD 117 ; WLD 110 and WLD 261 . Information: Prerequisite(s) may be waived with welding industry experience. WLD 264A and WLD 264B combined are equivalent to WLD 264.
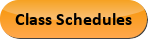
Course Learning Outcomes
- Demonstrate all safety protocol.
- Use appropriate terminology in the CNC plasma arc cutting process.
- Import images into Torchmate CAD.
- Demonstrate how to write, modify, and edit new and existing welding programs
- Create program and run a robotic welding project.
Outline:
- Health, Safety, and Environmental Practices
- Eye and ear protection
- Electric shock
- Arc rays
- Fumes and gases
- Fire and explosion
- Cylinder handling
- Pinch and crush points
- Robotic work cell safety
- During operation
- Inspection
- Maintenance
- Plasma Cutting Terminology
- Definitions
- Applications
- Plasma Cutting Equipment
- How plasma cutting works
- Manual plasma cutting
- CNC-operated plasma cutting
- Process variables
- Consumables
- Gas selection
- Cut quality
- CNC Related Software and Coordinate Systems
- File types
- CNC software
- Coordinate systems
- G-Code Programming
- Code letters
- Using G-Code
- G-Codes supported
- Introduction to tool paths
- Tool path types
- Tool path offset
- Applications
- Torchmate Driver Software User Interface
- Main screen features
- Menus
- Pull-down menu bar
- File
- Configuration
- Controller
- View
- Coordinates
- Favorites
- Boxes
- DRO
- Tool path viewport
- Control panels
- G-Code
- Jog
- Point
- Test Cutting
- Set amperage
- Set the height
- Run the line speed test
- Set the best voltage
- Introduction to Torchmate CAD
- Mainscreen features
- Importing Images into Torchmate CAD
- Vector graphics
- Raster images
- Importing raster images
- Basic CAD Project
- Sizing a part
- Round corners
- Add text
- Create bridges
- Creating a tool path
- Basic Robotic Operation
- Overall robotic cell description
- Pendent safety
- Pendent familiarization and basic operation
- Robot power
- Jogging robot
- Robot coordinating motions (World, Tool, Joint)
- Screen displays
- X,Y,Z motions and programs
- J1, J2, J3, J4, J5, J6 motions and operations
- Axis limits, brakes, home position and teach keys
- Create Teach Pendant Programs (TPP)
- Program name
- 1st TPP
- Program editing
- Bead around box
- Weld on plate
- How to input weld parameters, welding procedure specifications
- Set up jog frame-right hand rule
- Teach and create:
- Circular moves
- Circular weld programs
- Basic weaving
- Wait and timer instruction
- Other select key functions:
- Program
- Copy
- Delete
- Comment
- Write protect functions of the RO3iA
- Six point tool center point program
- Planning and creating individual teach pendant program (TPP)
- Maintenance Programs for Robotic Welding Cells
- GMAW troubleshooting
- Welding discontinuities
- Zero position program
- Preventative maintenance plan and service
- 6 point tool center point
- Robot Service Request (RSR)
- Torch reamer and wire clip
- Welding power source set up and operation
|
|
-
WLD 264A - Introduction to CNC Plasma Arc Welding: Module A 2 Credits, 3 Contact Hours 1 lecture period 2 lab periods
Procedures and techniques in Computer Numerical Control (CNC) plasma arc cutting. Includes health, safety, and environmental practices; history of plasma arc cutting; software and coordinate systems; tool paths, importing images, and cutting with a CNC plasma machine.
Prerequisite(s): CAD 101 or CAD 117 ; WLD 110 and WLD 261 . Information: Prerequisite(s) may be waived with welding industry experience. Constitutes approximately first one-half of WLD 264 . WLD 264A and WLD 264B combined are equivalent to WLD 264 .
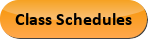
Course Learning Outcomes
- Demonstrate all safety protocol.
- Use appropriate terminology in the CNC plasma arc cutting process.
- Import images into Torchmate CAD.
- Demonstrate and determine process for setting arc length and travel speeds for various materials
Outline:
- Health, Safety, and Environmental Practices
- Eye and ear protection
- Electric shock
- Arc rays
- Fumes and gases
- Fire and explosion
- Cylinder handling
- Pinch and crush points
- Plasma Cutting Terminology
- Definitions
- Applications
- Plasma Cutting Equipment
- How plasma cutting works
- Manual plasma cutting
- CNC-operated plasma cutting
- Process variables
- Consumables
- Gas selection
- Cut quality
- CNC Related Software and Coordinate Systems
- File types
- CNC software
- Coordinate systems
- G-Code Programming
- Code letters
- Using G-Code
- G-Codes supported
- Introduction to tool paths
- Tool path types
- Tool path offset
- Applications
- Torchmate Driver Software User Interface
- Main screen features
- Menus
- Pull-down menu bar
- File
- Configuration
- Controller
- View
- Coordinates
- Favorites
- Boxes
- DRO
- Tool path viewport
- Control panels
- G-Code
- Jog
- Point
- Test Cutting
- Set amperage
- Set the height
- Run the line speed test
- Set the best voltage
- Introduction to Torchmate CAD
- Mainscreen features
- Importing Images into Torchmate CAD
- Vector graphics
- Raster images
- Importing raster images
- Basic CAD Project
- Sizing a part
- Round corners
- Add text
- Create bridges
- Creating a tool path
|
|
-
WLD 264B - Introduction to Basic Robotic Welding: Module B 2 Credits, 3 Contact Hours 1 lecture period 2 lab periods
Procedures and techniques in robotic automated welding. Includes safety, programming and operation procedures for Gas Metal Arc Welding (GMAW) process using a Fanuc R30iA robotics welding cell, Teach Pendent Programs (TPP), and maintenance.
Prerequisite(s): CAD 101 or CAD 117 ; WLD 110 and WLD 261 . Information: Prerequisite(s) may be waived with welding industry experience. Constitutes approximately second one-half of WLD 264 . WLD 264A and WLD 264B combined are equivalent to WLD 264 .
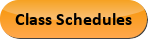
Course Learning Outcomes
- Demonstrate all safety protocol.
- Demonstrate how to set up power supply operations and safely jog the robot through different coordinate system.
- Demonstrate how to write, modify, and edit new and existing welding programs
- Create program and run a robotic welding project.
Outline:
- Health, Safety, and Environmental Practices
- Eye and ear protection
- Electric shock
- Arc rays
- Fumes and gases
- Fire and explosion
- Cylinder handling
- Pinch and crush points
- Robotic work cell safety
- During operation
- Inspection
- Maintenance
- Basic Robotic Operation
- Overall robotic cell description
- Pendent safety
- Pendent familiarization and basic operation
- Robot power
- Jogging robot
- Robot coordinating motions (World, Tool, Joint)
- Screen displays
- X,Y,Z motions and programs
- J1, J2, J3, J4, J5, J6 motions and operations
- Axis limits, brakes, home position and teach keys
- Create Teach Pendant Programs (TPP)
- Program name
- 1st TPP
- Program editing
- Bead around box
- Weld on plate
- How to input weld parameters, welding procedure specifications
- Set up jog frame-right hand rule
- Teach and create:
- Circular moves
- Circular weld programs
- Basic weaving
- Wait and timer instruction
- Other select key functions:
- Program
- Copy
- Delete
- Comment
- Write protect functions of the RO3iA
- Six point tool center point program
- Planning and creating individual teach pendant program (TPP)
- Maintenance Programs for Robotic Welding Cells
- GMAW troubleshooting
- Welding discontinuities
- Zero position program
- Preventative maintenance plan and service
- 6 point tool center point
- Robot Service Request (RSR)
- Torch reamer and wire clip
- Welding power source set up and operation
|
|
-
WLD 296 - Welding Independent Projects 1-4 Credits, 3-12 Contact Hours 0 lecture periods 3-12 lab periods
Self-directed laboratory projects. Includes project objectives, procedures, safety practices, welding processes, set-up for the project, and project completion.
Prerequisite(s): WLD 110 Information: Welding industry experience or welding skills may be substituted for the prerequisite requirement. See a welding instructor for approval. May be repeated up to three times for a maximum of sixteen credit hours. If this course is repeated, see a financial aid or Veteran’s Affairs advisor to determine funding eligibility as appropriate.
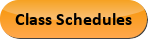
Course Learning Outcomes
- Demonstrate all safety protocol
- Create an independent welding project
- Complete an industry standard certification
Outline:
- Project Objectives
- Plans / Specifications
- Materials
- Procedures and Safety Practices
- Required welding process
- Oxyacetylene
- Grinder
- Other equipment
- Welding Processes and Set-up for the Project
- SMAW, GMAW, GTAW
- Equipment set-up
- Electrode type and amperage settings
- Other equipment and tools
- Project Completion
- Blueprint requirements
- Inspection
- Certification (Code) specifications
|
|
|
|