|
Jul 15, 2025
|
|
|
|
2022-2023 College Catalog [ARCHIVED CATALOG]
|
AIT 115 - Hydraulic Systems 3 Credits, 5 Contact Hours 2 lecture periods 3 lab periods
Introductory course in the principles of hydraulic system operation, components construction, maintenance, troubleshooting, and operation, as well as the role of the individual components in an operating hydraulic system. Includes hydraulic fitting and seals, accumulators, cylinders, directional control valves (DVC), relief valves, check valves, pumps, filters, hoses, and a variety of hydraulic control circuits.
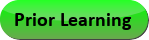.png)
Course Learning Outcomes
- Interpret hydraulic schematics, including identifying schematic symbols, process flow, and operation of the components and systems.
- Operate hydraulic systems, including the adjustment of hydraulic pressure control valves in the given hydraulic systems.
- Perform maintenance on hydraulic components, including inspection, removal, and replacement.
- Install components of hydraulic systems.
- Test components of hydraulic systems.
- Troubleshoot malfunctioning components of hydraulic systems.
Performance Objectives:
- Employ mechanical fabrication procedures.
Outline:
- Basic hydraulic schematics for operation of components/systems
- Basic hydraulic components
- NFPA schematic symbols
- ISO schematic symbols
- Operation of circuits
- Single stage hydraulic directional control valves with manual and electrical operators
- Two stage hydraulic directional control valves with manual and electrical operators
- Types of spool centers: 2-position/3-position and 2/3/4 way designs
- Operation of hydraulic circuits
- Accumulators
- Pump uploading
- Remote pressure control
- Rapid traverse slow feed
- Pilot-operated check valves
- Interpretation of hydraulic line types on a schematic
- Operation of a basic hydraulic circuit given a schematic
- Start Up/shut down of a hydraulic system
- Safe start up of a hydraulic power system (including pre-start inspection)
- Safe shut down of a hydraulic power system
- Manufacturers documentation per specific application to determine correct operating pressure
- Reading pressure gauges
- Adjusting system operating pressure using a relief valve
- Manual valves operation to direct system flow
- Adjusting pressure of a pressure reducing valve
- Adjusting system operating pressure
- Pressure-flow characteristics
- Relief valves
- Direct and pilot operated
- Operation
- Double acting cylinder
- Motor
- Hydraulic sequence valve
- Pressure reducing valve
- Pressure-flow characteristics of displacement pumps
- Fixed
- Variable
- Pressure checks and charge accumulators
- Pressure versus force/torque output characteristics of cylinders and motors
- Using Pascal`s law to determine system pressure and volume
- Hydraulic actuator speed
- Actuator speed adjustment
- Needle valve
- Non-compensated flow control valves
- Compensated flow control valves
- Flow control valves adjustment in meter-in and meter-out configurations
- Measuring actuator speed
- Operation
- Needle valve
- Flow control valve
- Compensated flow control valve
- Meter-in circuits
- Meter-out circuits
- Flow vs. speed characteristics of a hydraulic cylinder and a motor
- Calculating pump flow rate requirements given actuator speeds and sizes
- Calculating pump flow rate given pump size and speed
- IV. Hydraulic filters and maximizing hydraulic fluid cleanliness
- Inspection of hydraulic filters
- Interpreting filter specifications/models to determine correct filter
- Manufacturer’s documentation to determine frequency of change
- Measuring pressure differential across a filter
- Replacement of filters based on pressure differential across the filter
- Filter removal and replacement
- Symptoms of a required strainer
- Strainer replacement
- Hydraulic fluid
- Inspecting fluid levels using a level gauge
- Adding fluid to a hydraulic system
- Replacing hydraulic fluid using a filter cart
- Fluid inspection through sight, touch, and smell
- Fluid inspection for water and visible contaminants
- Water and contaminants removal from a hydraulic system
- Flushing
- Refilling
- Other
- Interpreting manufacturer`s documentation to determine appropriate oil selection
- Fluid sampling
- Taking fluid sample
- Submission to testing lab
- ISO 4406 cleanliness standards
- VI. Connecting, adjusting, and disconnecting flexible and rigid hydraulic conductors
- Interpreting pipe, hose, and tubing specifications
- Identification of type and size of hose, tubing, and hydraulic fittings (given a sample)
- Safety procedures for pressure removal before disconnecting conductors
- Proper fitting tightening, including consequences of over-tightening
- Attaching and tightening hydraulic components using line wrenches
- Hydraulic steel tubing
- Hydraulic fittings to components with threaded ports, using applicable thread sealant
- Hydraulic hoses and swivel fittings
- Hydraulic hoses and straight thread O-ring fittings
- Adjusting the position and alignment of conductors for proper operation
- How to make a hydraulic hose using barbed fittings
- O-rings
- Operation
- Installation
- Specification
- Operation of components in a basic hydraulic linear or rotary actuator
- Installing/connecting hydraulic components in basic functional circuit given a schematic
- Replacing subplate-mounted directional, flow, and pressure control valves in a hydraulic system
- Replacing a threaded port valve
- Mounting/aligning a hydraulic cylinder and a motor
- Types and applications of cylinder and motor mounting methods
- Analyzing the proper operation of a hydraulic system
- Bleeding procedures of a hydraulic system after component replacement
- Troubleshooting a basic hydraulic linear or rotary actuator circuit
- Basic components in a hydraulic circuit using in-circuit tests troubleshooting
- Using flow and pressure instruments to take hydraulic circuit readings during in-circuit testing
- Flow vs. pressure drop characteristics of components and conductors and their impact on system operation
- Systematic methodologies to troubleshoot basic hydraulic circuits with linear and rotary actuators
- Types of failure of basic hydraulic components
|
|