2021-2022 College Catalog [ARCHIVED CATALOG]
|
SGT 112 - Instrument Technician 7.75 Credits, 19.25 Contact Hours 2.00 lecture periods 17.25 lab periods
Introduction to precautions, documentation, and infection control procedures in healthcare facilities. Includes cleaning, decontamination, and disinfection; preparation and packaging, documentation and record maintenance, sterilization process, customer relations, sterile storage and inventory management, patient care equipment, and practice exam study tips.
Prerequisite(s): Completion of SGT 101 , SGT 102 , SGT 102LB , and SGT 102LC Information: This course provides hands-on clinical for students who wish to function in entry-level positions in Central Service and Sterile Processing departments of healthcare facilities. The course includes 32 hours of Certified Registered Central Service Technician (CRCST) exam review and 276 (total of 420) hours of hands-on experience that must be verified by the employer. This verification confirms eligibility for the International Association of Healthcare Central Service Material Management (IAHSCMM) exam.
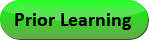.png)
Course Learning Outcomes 1. Interact effectively with interdisciplinary team members to adhere to Standard Precautions and Infection Control practices maintaining a clean and safe environment [communication].
2. Engage in practices that demonstrate an understanding of the importance of the role of the central sterile and sterile processing technician through continued improvement and life-long learning [professionalism].
3. Use information and technology to monitors inventory and maintains central sterile, surgery, and outpatient supply levels [informatics].
4. Minimize staff, patient, instrumentation and equipment risk and damage by following established protocols, policies, and procedures [safety].
5. Function effectively with inter-professional teams, fostering open communication, mutual respect, and shared decision-making to achieve quality patient care and safety [teamwork and collaboration].
6. Use data to monitor quality control on sterilization methods, using this data to continuously improve processes and outcomes for patient and staff safety [quality improvement].
7. Participate in quality improvement projects to reduce the errors in the processing of sterile instruments to decrease errors, avoid increased operative times and cost, and patient infections [patient-centered care].
8. Foster an environment of ethical, legal, moral and medical values demonstrated by record keeping, processing and distributing in compliance with internal and external regulatory standards [leadership]
9. Champion best practice to prevent and control the spread of infectious microorganisms in the hospital environment [evidence-based practice].
10. Examine personal influence on the assurance of high quality care [systems-based practice]. Performance Objectives:
- Function independently and safely in the various roles.
- Discuss aspects of the responsibilities of central service and sterile processing technician as it relates to the CRCST exam.
Outline:
- Cleaning, Decontamination, and Disinfection
- Safety standards
- Temperature and humidity of the work environment
- Preparing work area for decontamination
- Quality tests
- Troubleshooting cleaning equipment
- Disposable items from non-disposable items
- Preparing, cleaning and decontamination items
- Selecting appropriate disinfectant
- Disinfection instruments and equipment
- Transferring items to preparation area
- Preparation and Packaging
- Preparing work area for packaging
- Receiving items for preparation
- Inspecting items for cleanliness and functionality
- Selecting items for assembly
- Assembling items for packaging
- Packaging methods
- Labeling method
- Transferring items to appropriate areas
- Documentation and Record Maintenance
- Record maintenance
- Temperature, humidity, and corrective action
- Quality test results
- High level disinfection process
- Incident reports
- Sterilization Process
- Preparation of work area for sterilization
- Sterilizer tests and results
- Receiving items for sterilization
- Sterilization method and cycle
- Pre and post-sterilization package integrity
- Loading and unloading sterilizer
- Operating and monitoring sterilization equipment
- Cycle parameters
- Potential process failures
- Documenting sterilization load contents
- Transferring sterilized items to storage and distribution
- Customer Relations
- Requests and communication
- Policies and procedures
- Sterile Storage and Inventory Management
- Ordering inventory
- Receiving and Inspecting inventory
- Distribution, stocking, and rotating inventory
- Tracking items, monitoring use, and disposal
- Patient Care Equipment
- Inspecting equipment for cleanliness and functionality
- Assembling equipment for distribution
- Tracking, care, and handing of equipment
- Repair and safety inspection
- Practice Exams, Study Tips, and Review for the CRCST Exam
Effective Term: Full Academic Year 2020/2021
|