|
Sep 03, 2025
|
|
|
|
2021-2022 College Catalog [ARCHIVED CATALOG]
|
WLD 264 - Introduction to CNC Plasma Arc and Basic Robotic Welding 4 Credits, 6 Contact Hours 2 lecture periods 4 lab periods
Procedures and techniques in Computer Numerical Control (CNC) plasma arc cutting and robotic automated welding. Includes health, safety, and environmental practices; history of plasma arc cutting; software and coordinate systems; tool paths, importing images, and cutting with a CNC plasma machine. Also includes programming and operation procedures for Gas Metal Arc Welding (GMAW) process using a Fanuc R30iA robotics welding cell, Teach Pendent Programs (TPP), and maintenance.
Prerequisite(s): CAD 101 or CAD 117 ; WLD 110 and WLD 261 . Information: Prerequisite(s) may be waived with welding industry experience. WLD 264A and WLD 264B combined are equivalent to WLD 264.
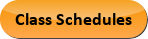
Course Learning Outcomes
- Demonstrate all safety protocol.
- Use appropriate terminology in the CNC plasma arc cutting process.
- Import images into Torchmate CAD.
- Demonstrate how to write, modify, and edit new and existing welding programs
- Create program and run a robotic welding project.
Outline:
- Health, Safety, and Environmental Practices
- Eye and ear protection
- Electric shock
- Arc rays
- Fumes and gases
- Fire and explosion
- Cylinder handling
- Pinch and crush points
- Robotic work cell safety
- During operation
- Inspection
- Maintenance
- Plasma Cutting Terminology
- Definitions
- Applications
- Plasma Cutting Equipment
- How plasma cutting works
- Manual plasma cutting
- CNC-operated plasma cutting
- Process variables
- Consumables
- Gas selection
- Cut quality
- CNC Related Software and Coordinate Systems
- File types
- CNC software
- Coordinate systems
- G-Code Programming
- Code letters
- Using G-Code
- G-Codes supported
- Introduction to tool paths
- Tool path types
- Tool path offset
- Applications
- Torchmate Driver Software User Interface
- Main screen features
- Menus
- Pull-down menu bar
- File
- Configuration
- Controller
- View
- Coordinates
- Favorites
- Boxes
- DRO
- Tool path viewport
- Control panels
- G-Code
- Jog
- Point
- Test Cutting
- Set amperage
- Set the height
- Run the line speed test
- Set the best voltage
- Introduction to Torchmate CAD
- Mainscreen features
- Importing Images into Torchmate CAD
- Vector graphics
- Raster images
- Importing raster images
- Basic CAD Project
- Sizing a part
- Round corners
- Add text
- Create bridges
- Creating a tool path
- Basic Robotic Operation
- Overall robotic cell description
- Pendent safety
- Pendent familiarization and basic operation
- Robot power
- Jogging robot
- Robot coordinating motions (World, Tool, Joint)
- Screen displays
- X,Y,Z motions and programs
- J1, J2, J3, J4, J5, J6 motions and operations
- Axis limits, brakes, home position and teach keys
- Create Teach Pendant Programs (TPP)
- Program name
- 1st TPP
- Program editing
- Bead around box
- Weld on plate
- How to input weld parameters, welding procedure specifications
- Set up jog frame-right hand rule
- Teach and create:
- Circular moves
- Circular weld programs
- Basic weaving
- Wait and timer instruction
- Other select key functions:
- Program
- Copy
- Delete
- Comment
- Write protect functions of the RO3iA
- Six point tool center point program
- Planning and creating individual teach pendant program (TPP)
- Maintenance Programs for Robotic Welding Cells
- GMAW troubleshooting
- Welding discontinuities
- Zero position program
- Preventative maintenance plan and service
- 6 point tool center point
- Robot Service Request (RSR)
- Torch reamer and wire clip
- Welding power source set up and operation
Effective Term: Full Academic Year 2019/20
|
|