|
2022-2023 College Catalog [ARCHIVED CATALOG]
Course Descriptions
|
|
Legend for Courses
HC/HN: Honors Course IN/IH: Integrated lecture/lab LB: Lab LC: Clinical Lab LS: Skills Lab WK: Co-op Work
SUN#: is a prefix and number assigned to certain courses that represent course equivalency at all Arizona community colleges and the three public universities. Learn more at www.aztransfer.com/sun.
|
|
Machine Tool Technology |
|
-
MAC 100 - Introduction to Machine Tool 3 Credits, 3 Contact Hours 3 lecture periods 0 lab periods
Principles and procedures for basic machine tool operations. Includes careers in manufacturing, machine tool history, safety, materials, manufacturing process planning, and measurement. Also includes principles of metal cutting, bench and hand tools, power saws, drill presses, and abrasive machine.
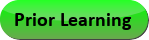.png)
Course Learning Outcomes
- Use Micrometers, Depth Mic, and Calipers accurately
- Demonstrate an understanding of basic machine shop safety
- Calculate correct speeds and feeds for machines
- Pass the National Institute for Metalworking Skills (NIMS) Measurement Materials and Safety certification test
- Achieve the NC3 Precision Measuring Instruments Certificate
Outline:
- Careers in Manufacturing
- Trade opportunities
- Types of machine shops
- Machine Tool History
- Evolution and the industrial revolution
- Types and applications
- Safety
- General safety guidelines
- Personal Protective Equipment
- Safety Data Sheets (SDS)
- Hazardous Material Information Systems (HMIS)
- Causes of accidents
- Materials
- Manufacture of iron and steel
- Metals, their properties, identification
- Manufacturing Process Planning
- Technical drawings and prints
- Orthographic projections
- Title block and block tolerances
- Surface finish requirements
- Introduction to geometric dimensioning and tolerancing
- Classes of fits
- ANSI Standard Fit Symbols
- Machining procedures
- Speeds and feeds
- Calculate for lathes
- Calculate for mills
- Measurement
- Measurement systems
- Micrometers
- Vernier calipers
- Inspection tools
- Reading steel rules
- Gage block assembly
- Principles of Metal Cutting
- Reading chips
- Cutting fluid
- Bench and Hand Tools
- Typical shop hand tools
- Cutting hand tools
- Power Saws
- Cut-off saws
- Contouring saws
- Drill Presses
- Types of drill presses
- Twist drills
- Producing and finishing holes
- Abrasive Machines
- Bench and pedestal grinders
- Abrasive belt machines
|
|
-
MAC 110 - Manual Machine Shop 4 Credits, 6 Contact Hours 2 lecture periods 4 lab periods
Introduction to basic machine shop practices. Includes safety, basic set-up and operation of engine lathes, and vertical milling machines.
Prerequisite(s): MAC 100 or concurrent enrollment.
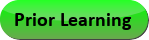.png)
Course Learning Outcomes
- Adhere to all shop safety practices.
- Successfully demonstrate machine setup and perform basic applications and operations using a manual lathe.
- Successfully demonstrate machine setup and perform basic applications and operations using a vertical mill.
- Perform in-process part inspection.
- Pass the NIMS Manual Milling Certification
Outline:
- Safety
- General safety guidelines
- Machinery safety
- Lathes
- Nomenclature and accessories
- Cutting tools and holders
- Turning and facing
- Grooving
- Threading
- Knurls
- Drills
- Calculating feeds and speeds
- Set-ups and operations
- Turning
- Grooving
- Chamfering
- Facing
- Knurling
- Single point threading
- Center drilling
- Vertical Milling Machines
- Nomenclature and accessories
- Cutting tools and holders
- Endmills
- Reamers
- Center drills
- Drills
- Taps
- Calculating feeds and speeds
- Set-ups and operations
- Face Milling
- Angle Milling
- Corner Rounding
- Drilling
- Center Drill
- Tapping
|
|
-
MAC 120 - Machine Shop 4 Credits, 6 Contact Hours 2 lecture periods 4 lab periods
Instruction and applied practices of advanced manual machining procedures. Includes a more in-depth application of safety, lathe usage, vertical milling machines, and outside diameter (OD) grinding machines.
Prerequisite(s): MAC 110 or equivalent with department advisor approval.
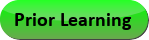.png)
Course Learning Outcomes
- Adhere to all shop safety practices
- Proficiently make part skill sets to print
Outline:
- Safety
- General safety guidelines
- Machinery safety
- Lathes
- Chucks
- Turn between centers
- Thread measurement
- Milling Machines
- Special cutters and their applications
- Accessories
- Grinding Machines
- Grinding wheels
- OD grinders
|
|
-
MAC 125 - Inspection Quality Assurance 4 Credits, 6 Contact Hours 2 lecture periods 4 lab periods
Principles and applications of dimensional measurement. Includes line graduated measuring instruments, fixed gages, gage blocks, comparative measurements, optical comparators and projectors. Also includes angle measurement, straightness, flatness, perpendicularity measurement, and coordinated measuring machines.
Prerequisite(s): GTM 105 and MAC 100 . Information: Prerequisite may be waived with industry experience. See a machine tool instructor for prerequisite information.
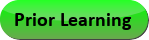.png)
Course Learning Outcomes
- Demonstrate proficiency of physical measurement
- Proficiently use coordinate measuring machine
- Apply usage of Quality Assurance forms and data gathering
Outline:
- Introduction
- Course objectives
- Expectations of course
- Line Graduated Measuring Instruments.
- Rules and tapes
- Micrometers and calipers
- Fixed Gages
- Classifications of fixed gages
- Principles of limit gage measurement
- Fixed gages for multiple dimensions
- Gage Blocks
- Description and technical requirements
- Gage block sets and accessories
- Applications for gage blocks
- Comparative Measurements
- Evaluation of the measuring system and instruments
- Dial indicators
- Electronic measuring instruments
- Internal measuring instruments
- Optical Comparators and Projectors
- Principles of optical measurement
- Applications of optical measurement
- Angle Measurement
- Unit of angle measurement
- Angle measuring systems and techniques
- Straightness, Flatness, and Perpendicularity Measurement
- Measurements of straightness
- Measurements of flatness
- Measurements of perpendicularity
- Coordinate Measuring Machines
- Manual applications
- Computer supported applications
|
|
-
MAC 130 - Machine Setup and Fixture Making 3 Credits, 5 Contact Hours 1 lecture period 4 lab periods
Applied setup of manual machining techniques and related skill sets to produce various part fixtures. Includes translating blueprints into machine setup and fixture making.
Prerequisite(s): MAC 110 Information: Prerequisite(s) may be waived with faculty approved industry experience.
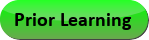.png)
Course Learning Outcomes
- Adhere to all shop safety practices
- Design and manufacture different types of fixtures
Outline:
- Safety
- General Safety Guidelines
- Machine usage safety
- Machine Setup
- Approaches
- What works and why
- Setups an part accuracy
- Design and Construction of Fixtures
- Plate fixtures
- Angle plate fixtures
- Vise jaw fixtures
- Components
- Types of locating pins
- Types of clamps
- Fixture Making
- Approaches per blueprint
- Machining principles for making fixtures
- Machining accuracy
|
|
-
MAC 140 - Introduction to Electrical Discharge Machining 4 Credits, 6 Contact Hours 2 lecture periods 4 lab periods
Applications for electrical discharge machining (EDM). Includes EDM machines, processes, spark generation, dielectric fluids, manufacturing of electrodes, and surface finishes.
Prerequisite(s): MAC 110 Information: Prerequisite(s) may be waived by faculty approved industry experiences.
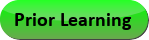.png)
Course Learning Outcomes
- Discuss EDM machine types, applications, nomenclature, and safety.
- Describe EDM basic machine functions and processes.
- Describe power supplies, spark generation, cycle time, power settings, and dielectric fluids.
- Demonstrate proper electrode selection, fabrication, and describe their properties.
- Demonstrate methods of achieving various surface finishes and finished burn sizes.
Outline:
- Overview of Electrical Discharge Machining (EDM)
- Safety procedures
- Origins and development of EDM
- Machine types and applications in industry
- EDM nomenclature
- EDM Machines and Processes
- Ram EDM (die-sinkers)
- EDM machines
- Machine set-ups
- Material removal
- Flushing
- Spark Generation and Dielectric Fluids
- Power supplies
- Cycle times
- Volts and amps
- Spark Gap
- Dielectric fluids
- Electrodes
- Selection and types
- Fabrication
- Overcut
- Wear
- Surface Finishes
- Surface finish considerations
- Duty cycle and finish
|
|
-
MAC 150 - Introduction to Computer Numerical Control (CNC) Operations (Mill and Lathe) 4 Credits, 6 Contact Hours 2 lecture periods 4 lab periods
Introduction to setup, operations, and programming procedures for Computer Numerical Control (CNC) Mills and Lathes. Includes CNC machining system, positioning and coordinate systems used in CNC machining, part programming, diagnosis and correction of programming errors, and programming procedure.
Prerequisite(s): GTM 105 or concurrent enrollment. Recommendation: Completion of CAD 117 before enrolling in this course. If any recommended course is taken, see a financial aid or Veteran’s Affairs advisor to determine funding eligibility as appropriate.
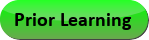.png)
Course Learning Outcomes
- Describe tool changers, tool storage, tool offsets, special tooling, and fixturing.
- Demonstrate the construction of a basic part program.
- Pass the NIMS CNC Lathe Operations Credential
- Demonstrate machine setup, tool setting, loading of the program, and machining of the part.
- Pass the NIMS CNC Mill Operations Credential
Outline:
- Numerical Control (NC) and Computer Numerical Control (CNC) Machining Systems
- Introduction and safety procedures
- Description of NC/CNC machinery
- Objectives and application of NC/CNC
- Components and control systems
- Tool changers, tool storage, and special tooling/fixturing
- Positioning and Coordinate Systems used in NC/CNC Programming
- Review the Cartesian coordinate system
- Description and use of datum and delta dimensioning
- Description and use of absolute and incremental positioning
- Plotting part coordinates
- Plotting cutter offsets
- Selecting order of operations needed for programming
- Developing a program
- Importance of program documentation
- Part Programming
- Point to point programming
- Program formatting
- Description and use of Canned Cycles
- Trigonometry used in plotting intersections and tangent points
- Plotting arc positions
- Plotting angle positions
- Plotting cutter offsets
- Arc programming
- Angular programming
- Diagnosis and Correction of Programming Errors
- Operator error
- Dimensional error
- Machine error
- Programming error
- Machine Usage Procedures
- Set zero coordinates/tool length offset
- Load and edit program in machine
- Adjust speed and feeds
- Program Prove In
- Cutting tool setup
|
|
-
MAC 155 - Computer Numerical Control (CNC) Mill Programming II 4 Credits, 6 Contact Hours 2 lecture periods 4 lab periods
Continuation of MAC 150 programming instruction. Includes a review of Computer Numerical Control (CNC), mill programming, diagnosis and correction of programming errors, advanced programming techniques used in production and prototype machining.
Prerequisite(s): MAC 150 Information: Prerequisite(s) may be waived with industry experience and faculty approval.
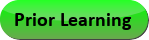.png)
Course Learning Outcomes
- Demonstrate usage and setup of current CNC Mills.
- Describe techniques used in diagnosing and correcting a program.
- Demonstrate the use of advanced programming techniques.
- Use sub-programming applications.
- Pass the NIMS CNC Mill Programming Setup and Operation Certification
Outline:
- Review of CNC Mill Programming
- Safety procedures
- Cartesian Coordinate System
- Absolute and incremental positioning
- Order of operation, process planning, and documentation
- Trigonometry used in calculating cutter path
- CNC operations
- Part programming
- Diagnosis and Correction of Programming Errors
- Operator error
- Dimensional error
- Machine error
- Advanced Programming Techniques Used in Production and Prototype Machining
- Use of tooling offsets
- Multiple part programming
- Introduction of 4th axis programming
- Description of tooling used in production machining
- Applied knowledge of tooling/fixtures
- Pallet changers
- Multiple vices
- Rotary tables
- Part and tool setup with finished part inspection
- Uses of fixtures in milling operations
- Description of programming techniques used in production and prototype machining
- Advanced canned cycles
- Subprograms and routines
- Loops and repeat functions
- Introduction to Sub-Programming
- Sub-routing applications
- Utilization of sub’s in part programs
- Finished Parts
- Inspection
- Part per print
|
|
-
MAC 160 - Computer Numerical Control (CNC) Lathe Programming 4 Credits, 6 Contact Hours 2 lecture periods 4 lab periods
Operations and procedures for Computer Numerical Control (CNC) Lathe. Includes review of CNC concepts and programming, diagnosis and correction of programming errors, advanced programming for CNC Lathes.
Prerequisite(s): GTM 105 and MAC 150 . Information: Prerequisites may be waived with industry experience and faculty approval.
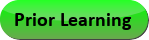.png)
Course Learning Outcomes
- Discuss CNC concepts and programming basics that will include operator setup knowledge with tool setting.
- Demonstrate ability to create part program.
- Demonstrate part and tooling setup for a 2 axis CNC Lathe.
- Perform in-process part inspection.
- Pass NIMS CNC Lathe Programming Set-up and Operations Credential.
Outline:
- Review of CNC Concepts and Programming
- Safety procedures
- Cartesian coordinate system
- Absolute and incremental positioning
- Order of operation, process planning, and documentation
- Trigonometry used in calculating cutter path
- Operator level understanding of CNC machine operations
- Part programming
- Diagnosis and Correction of Programming Errors
- Operator error
- Dimensional error
- Machine error
- Advanced Programming for CNC Lathes
- Part programming using cutter compensation
- Use of tool offsets in machine operations to produce parts
- Tooling used in production machining
- Special tooling
- Fixtures
- Part(s) inspection
- Programming techniques used in production
- Advanced canned cycles
- Subprograms and routines
- Loops and repeat functions
- Tooling requirements
- Tooling used
- Feeds and speeds
|
|
-
MAC 257 - Computer-Aided Machining CAM I 4 Credits, 6 Contact Hours 2 lecture periods 4 lab periods
Computer-Aided Machining (CAM) I Programming of Computer Numerical Control (CNC) machines using Computer-Aided Manufacturing (Mastercam) software. Includes a review of CNC and Computer-Aided Drafting (CAD), introduction to a CAM environment, creating geometry, operating manager, and code generation.
Prerequisite(s): MAC 155 Information: Prerequisite(s) may be waived with industry experience with faculty approval.
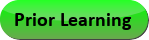.png)
Course Learning Outcomes
- Describe standard shop safety, positioning systems, orders of operation, proper nomenclature associated with drafting, geometric construction, and windows command.
- Demonstrate basic CAM commands and menu usage.
- Create wireframe geometry on a CAD-CAM system.
- Demonstrate use of the operating manager with tool paths.
- Exhibit the ability to generate code for different numerical control machines.
Outline:
- Review of Computer Numerical Control (CNC) and Computer-Aided Drafting (CAD)
- Safety procedures
- Cartesian coordinate system
- Absolute and incremental positioning
- Order of operation and documentation
- Drafting language and geometric construction
- Introduction to a CAM Environment
- Machining 2D Models
- Main menu
- Overview of CAM icons
- Stock setup
- Explanation of menu bars and their uses
- Import solid models
- Data entry shortcuts
- Creating Geometry
- Arc, lines, radius
- Transforming geometry
- Moving
- Copying
- Rotating
- Mirroring
- Extracting wireframe geometry from solid models
- Operating Manager
- Drilling, contour, pocketing, islands, and surfaces
- Get tool from library
- Selecting tool parameters
- Verification of tool path
- Transform tool path
- Code Generation
- Coding a process model
- Posting code for different machining centers
|
|
-
MAC 258 - Computer Aided Machining (CAM) II 4 Credits, 6 Contact Hours 2 lecture periods 4 lab periods
Continuation of MAC 257 . Includes three-dimensional (3D) surfacing and introduction to CAM Lathe Programming.
Prerequisite(s): MAC 257
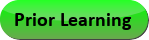.png)
Course Learning Outcomes
- Create and edit three-dimensional (3D) profile surfaces.
- Create 3D surfacing toolpaths.
- Create toolpaths using Solid Models.
- Apply CAM programming to lathe.
Outline:
- Profile Surfaces
- Drive/check
- Rough
- Finish
- Re-cut manager
- Creating and Editing 3D Surfaces
- Revolved
- Ruled
- Loft
- Project curves
- Swept
- Draft
- 3D Milling Toolpaths
- Roughing strategies
- Finishing strategies
- Using stock models
- Workholding for surfacing
- Programming for fixtures
- CAM for Lathe
- Chuck setup
- Stock setup
- General operations
- Tools
- Canned cycles
- Posting
|
|
-
MAC 259 - Computer Aided Machining (CAM) III 4 Credits, 7 Contact Hours 1 lecture period 6 lab periods
Continuation of MAC 258 . Includes profile surfaces of tool path, solid model features in three-dimension (3-D), and editing solid model surfaces. Also includes introduction to Multi-Axis Milling.
Prerequisite(s): MAC 258
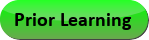.png)
Course Learning Outcomes
- Create a tool path for a solid model surface.
- Create three-dimensional (3-D) solid model surfaces.
- Edit solid model surfaces.
- Create 5 Axis toolpath
- Set up Basic 5 Axis Milling using a laser tool setter. (Siemens and Haas)
Outline:
- Profile Surfaces of Tool Path.
- Drive/Check
- Rough passes
- Finish passes
- Recut/Edit
- Code generators
- Solid Model Features in Three-Dimension (3-D)
- Revolved surface
- Ruled surface
- Loft surface
- Swept surface
- Extrude surface
- Cut body surface
- Add boss feature
- Editing Solid Model Surfaces
- Zigzag
- One way
- Plunge control
- Step directions
- Offset
- Cut tolerance
- Data management techniques
- 5 Axis Milling
- Planes management
- Tool path selection
- Machine setup
- Part probing
- Using laser tool setter
- Prove in 5 Axis program
|
|
-
MAC 275 - Applied Metallurgy 4 Credits, 6 Contact Hours 2 lecture periods 4 lab periods
Application of metallurgical concepts, procedures, and testing. Includes materials, alloy classification systems, industrial and manufacturing concepts, properties and testing, and industrial and manufacturing processes and applications.
Prerequisite(s): GTM 105 Gen-Ed: Meets CTE - M&S
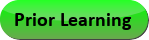.png)
Course Learning Outcomes
- Discuss the general origin and role of materials, metals and alloys in the modern world.
- Use standard classification systems, for both ferrous and non-ferrous metals and alloys, to specify and identify common industrial materials.
- Discuss the basic industrial and manufacturing concepts related to the processes of shaping metals, and how such procedures are specified and described.
- Perform Rockwell and Brinell hardness tests, and relate the results of these procedures to the basic strength properties of metals and alloys.
- Describe how the structures of metals and alloys relate to their strength properties, and guide their processing operations.
- Discuss the basic processes for strengthening metals and performing the common heat-treating procedures.
- Discuss how the basic concepts of metallurgy apply to machining.
- Select and develop a project of specific interest that applies metallurgical background.
Outline:
- Materials
- Introduction to materials
- Introduction to metals
- Introduction to alloys
- Extractive metallurgy
- Alloy Classification Systems
- Ferrous alloys, steels, stainless steels, and irons
- Nonferrous metals and alloys
- Industrial and Manufacturing Concepts
- Metal shaping processes
- Interpretation of technical information
- Temperature and its effects
- Specifications documents
- Properties and Testing
- Strength properties
- Hardness testing
- Structure and Properties
- Nature of metals
- Metallography
- Industrial and Manufacturing Processes
- Strengthening processes
- Heat treating equipment and procedures
- Industrial and Manufacturing Applications
- Metallurgy in machining
- Casting metallurgy
- Individual Student Projects
- Project planning and development
- Presentation of projects
|
|
-
MAC 296 - Machine Tool Independent Projects 1-4 Credits, 3-12 Contact Hours 0 lecture periods 3-12 lab periods
Independent machine tool projects. Includes producing prints that become skill set completed projects with setup of machines to part completion.
Prerequisite(s): MAC 110 Information: May be taken sixteen times for a maximum of sixteen credit hours. If this course is repeated see a financial aid or Veteran’s Affairs advisor to determine funding eligibility as appropriate. Consent of instructor must be obtained before enrolling in this course.
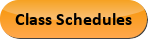
Course Learning Outcomes
- Define project objectives.
- Use the mill, lathe, grinder or other machine tools to complete an independent project.
- Identify necessary tooling to be used in completing a project.
- Demonstrate safety and machining practices to complete a project per blueprint requirements and inspection.
Outline:
- Define a Project
- Plans
- Materials
- Procedures and Safety Practices
- Mill
- Lathe
- Grinder
- Other equipment
- Tooling Necessary for the Project
- Mill cutting tools
- Lathe cutting tools
- Other equipment tooling
- Complete a Project
- Blueprint requirements
- Inspection
|
|
|
|