|
2021-2022 College Catalog [ARCHIVED CATALOG]
Course Descriptions
|
|
Legend for Courses
HC/HN: Honors Course IN/IH: Integrated lecture/lab LB: Lab LC: Clinical Lab LS: Skills Lab WK: Co-op Work
SUN#: is a prefix and number assigned to certain courses that represent course equivalency at all Arizona community colleges and the three public universities. Learn more at www.aztransfer.com/sun.
|
|
Aviation Technology |
|
-
AVM 100A - Aircraft Maintenance Fundamentals: Module A 3 Credits, 6 Contact Hours 1 lecture period 5 lab periods
Introduction to the fundamental knowledge and skill requirements of an Airframe and Powerplant mechanic. Includes fasteners, safety and rigging, aircraft maintenance tools, aircraft types and construction, aircraft materials, theory of flight, and aircraft structures.
Information: Constitutes approximately the first one-half of AVM 100 . AVM 100A and AVM 100B together constitute AVM 100 .
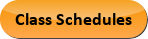
Course Learning Outcomes
- Describe the work requirements and the responsibilities of a qualified Airframe and Powerplant (A&P) mechanic as described in Title 14 Code of Federal Regulations.
- Identify different types of fasteners and their uses, and demonstrate methods of locking those fasteners.
- Discuss the work environment of an A&P mechanic, workplace hazards, personal safety procedures, facility and ramp safety procedures, steps to be taken in an emergency, and fire protection procedures; identify the correct fire extinguisher type and techniques for the different classes of fire; and describe the correct safe procedures for starting, moving and servicing aircraft and ground support equipment, and erecting and using stands and scaffolding.
- Discuss the tools and equipment available to the A&P mechanic and their use and maintenance: safety rules and proper use of hand tools, sheet metal machines, material handling equipment, cutting tools, and measuring tools.
- Identify and describe different types of aircraft and how they are constructed; basic components of an aircraft; differences in aircraft structures; and airfoil design.
- Identify different types of aircraft materials, their uses, and indications of corrosion; demonstrate the removal and treatment of corrosion.
- Describe why and how an aircraft flies, and discuss the principles related to aerodynamics, theory of flight, airfoil characteristics, and fundamentals of lift production.
- Discuss the materials and processes involved in aircraft construction; identify and compare aircraft structural materials; and describe a basic level of heat treatment processes, dye-penetrant, eddy current, and ultrasonic and magnetic particle inspections.
- Identify types of aircraft corrosion and its removal and treatment, and select the appropriate cleaning solutions for various materials.
Outline: I. Airframe and Powerplant Mechanics
A. Airframe (A)
B. Powerplant (P)
C. Structures
D. Avionics
E. Responsibilities and limitations of A&P certification
F. Qualification requirements for A&P certification
G. Types of work
H. Terminology
I. Technical data
II. Fasteners
A. Threaded
B. Rivets
C. Adhesives
D. Special
III. Safety and Rigging
A. Personal
B. Facility
C. Aircraft
D. Equipment
E. Fire
F. Fluids
G. Chemicals
H. Aircraft movements
I. Human factors
IV. Aircraft Maintenance Tools
A. Hand tools
B. Power tools
C. Measuring tools
D. Special tools
V. Aircraft Types and Construction
A. Fixed wing
1. Monoplanes
2. Biplanes/ triplanes
3. Canard
4. Tandem
B. Rotary wing
1. Helicopter
2. Autogyro
3. Ornithopter
C. Flight controls
1. Primary
2. Secondary
D. Landing gear
1. Fixed
2. Retractable
3. Floats
4. Skis
VI. Aircraft Materials
A. Wood
B. Metal
C. Man made
D. Sealants
E. Cleaning
F. Removal and inhibition of corrosion
G. Repair
H. Technical data
VII. Theory of Flight
A. Theory of flight
B. History of flight
C. Basic aerodynamics
D. Weight and balance
E. Atmospheric conditions
F. Propulsion requirements
VIII. Aircraft Structures
A Primary structure
1. Wood
2. Metal
3. Composite
B. Secondary structure
1. Wood
2. Metal
3. Composite
4. Plastic
C. Aircraft covering
D. Protective finishes
E. Corrosion
1. Identification
2. Removal
3. Treatment
F. Repair
Effective Term: Full Academic Year 2021/2022 |
|
-
AVM 100B - Aircraft Maintenance Fundamentals: Module B 3 Credits, 6 Contact Hours 1 lecture period 5 lab periods
Introduction to the fundamental knowledge and skill requirements of an airframe and powerplant mechanic. Includes powerplant types, aircraft assembly, engine theory, aircraft repair, aircraft reciprocating engine overhaul/repair, aircraft maintenance, aircraft systems and components, rigging flight controls, and jacking aircraft.
Prerequisite(s): AVM 100A Information: Constitutes approximately the second one-half of AVM 100 . AVM 100A and AVM 100B together constitute AVM 100 .
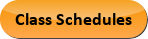
Course Learning Outcomes
- Discuss the methods used to propel an aircraft; aircraft powerplant configurations; manufacturers and classification used by the aviation industry; the principles of operation and mechanics behind energy transformation; the factors effecting power and the distribution of power; propeller components; and typical nomenclature used in the inspection, servicing, and repairs of aircraft engines.
- Identify different parts of an aircraft and demonstrate how to assemble and disassemble them using technical data.
- Describe how aircraft engines work.
- Identify different types of damage and demonstrate the methods used to repair that damage.
- Discuss aircraft engine components and their purpose; perform visual, dimensional, and non-destructive inspections used in aircraft reciprocating engine overhaul; and demonstrate the proper methods of cleaning and storing engine components in preparation for inspection, repair, or overhaul.
- Discuss the scope of work required of an A&P mechanic during routine and non-routine inspections.
- Describe the principles of hydraulic and pneumatic power systems, and the system requirements for small and large aircraft by comparison of their needs; identify hydraulic, electrical, and pneumatic system components both physically and operationally (including hydraulic fluids) and match them with their proper seal, line and “O” ring materials; and identify and discuss the basic mechanics used to power or transfer information on aircraft/engine instrument systems.
- Identify different control surfaces and their specific purpose, and demonstrate inspection and maintenance.
- Demonstrate the safe procedure for jacking aircraft and making it safe while jacked.
Outline: I. Powerplant Types
A. Reciprocating engines
1. Air cooled
2. Liquid cooled
3. Rotary
4. Radial
5. Inline
6. Horizontally opposed
7. ‘V’; ‘H’; ‘X’;
8. Tandem
9. Inverted
B. Gas turbine engines
1. Centrifugal flow
2. Axial flow
3. Turboprop
C. Selection for use
D. Propeller constructions
1. Wood
2. Steel
3. Aluminum
4. Composite
E. Propeller types
1. Fixed pitch
2. Controllable pitch
3. Contra-rotating
F. Propeller governors
G. Ram jet
H. Rocket
I. Pulse jet
J. Engine starting and ignition
II. Aircraft Assembly
A. Technical data
B. Major components
C. Procedures
III. Engine Theory
A. Reciprocating engines
B. Gas turbine engines
C. Ram, rocket and pulse jet
D. Fuels, fuel systems, and fuel storage
E. Lubricants and lubricating systems
F. Cooling
IV. Aircraft Repair
A. Damage identification
B. Damage assessment
C. Types of repair
D. Required procedures following a repair.
E. Technical data
V. Aircraft Reciprocating Engine Overhaul/Repair
A. Dismantle
B. Cleaning
C. Inspection
D. Inspection of components
E. Identification of parts
F. Measuring parts
G. Engine reassembly
H. Technical data
VI. Aircraft Maintenance
A. Requirements
B. Regulations
C. Procedures
D. ATA codes
E. Inspection
F. Technical data
G. Repair
H. Special equipment
VII. Aircraft Systems and Components
A. Mechanical
B. Pneumatic
C. Hydraulic
D. Electrical
E. Flight instruments
F. Engine instruments
G. Auxiliary instruments
VIII. Rigging Flight Controls
A. Identification
B. Technical data
C. Procedures
D. Inspection
E. Control surface balancing.
IX. Jacking Aircraft
A. Equipment inspection
B. Aircraft preparation
C. Procedures
D. Technical data
Effective Term: Full Academic Year 2021/2022 |
|
-
AVM 105 - Aircraft Sheet Metal Repair I 3.5 Credits, 8 Contact Hours 1.25 lecture periods 6.75 lab periods
Principles and procedures for fuselage, wing, and empennage sheet metal repair. Includes safety, hand tools, layout methods, materials, fasteners, repair techniques, parts fabrication, and corrosion prevention and control.
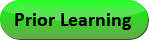.png)
Course Learning Outcomes
- Demonstrate proficient knowledge of applicable safety procedures and machine operation
- Demonstrate proficiency in the identification and use of aircraft fasteners and pattern layout
- Demonstrate proficient knowledge of various parts fabrication processes
- Demonstrate proficient knowledge of various inspection and repair techniques
Outline:
- Safety Procedures and Machine Operation
- Safety
- Hand tools
- Shop
- Sheet metal machines
- Safety around aircraft
- Materials handling
- Hand tools and equipment used in sheet metal repair
- Basic mechanic hand tools
- Sheet metal mechanic hand tools
- Forming, shearing and bending equipment
- Aircraft Fasteners and Pattern Layout
- Aircraft Fasteners
- Solid
- Blind
- Special
- Installation and removal techniques
- Basic sheet metal layout methods and repair operations
- Blueprint review
- Mathematical determination of fastener placement
- Measuring tools
- Inspection methods
- Fabrication Processes
- Aircraft structural materials
- Aluminum designations
- Alloying
- Material characteristics
- Heat treatments
- Parts fabrication
- Forming
- Rolling
- Shearing
- Shrinking and stretching
- Bend allowance and bending
- Inspection and Repair Techniques
- Aircraft repair techniques
- Single Pilot Resource Management (SRM) usage
- Maintenance manuals
- Scab repairs
- Flush repairs
- Splicing repairs
- Built up repairs
- Corrosion Prevention and Control
- Types
- Identification
- Removal
- Treatment
Effective Term: Full Academic Year 2021/2022 |
|
-
AVM 106 - Aircraft Sheet Metal Repair II 3.5 Credits, 8 Contact Hours 1.25 lecture periods 6.75 lab periods
Continuation of AVM 105 . Includes safety, bend allowance, layout, fasteners, machine usage, patching techniques and structural repair techniques.
Prerequisite(s): AVM 105
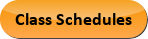
Course Learning Outcomes
- Calculate bend allowance mathematical determinations and perform layout in preparation for bending.
- Demonstrate equipment set-up and equipment operation for required bend allowance specifications.
- Describe use and safety requirements for bending, rolling, cutting, dimpling, squeeze riveting and shaving equipment.
- Identify structural fasteners by type, use, and size.
- Demonstrate installation procedures for structural fasteners.
- Describe shear, tensile and bearing strength analysis techniques required in the layout of structural repairs.
- Demonstrate several types of structural repairs to an aircraft.
Outline:
- Bend Allowance
- Mathematical determination
- Layout
- Radius requirements
- Equipment set-up
- Bending procedures
- Machine Safety and Use
- Cornice brake
- Box and pan brake
- Slip rolls
- Contour band saw
- Dimplings
- Structural Fasteners
- Function
- Use
- Size
- Installation
- Strength Analysis Techniques
- Shear
- Tensile
- Bearing
- Fabrication from a Blueprint
- Hand forming
- Joggling
- Shrinking
- Stretching
- Stress Relieving
- Clean up
- Structural Repairs
- Fuselage Repair - Flat
- Fuselage Repair - Curved
- Frame Repair
- Stringer Repair
- Sheet Replacement
- Section Replacement
Effective Term: Full Academic Year 2021/22 |
|
-
AVM 110 - Aircraft Blueprint Reading 3 Credits, 3 Contact Hours 3 lecture periods 0 lab periods
Theory and application of aircraft blueprint reading. Includes types of aircraft drawings, measuring tools, drawing and lay-out equipment, types of views, projections, reference lines, drawing format, title block, manufacturing codes, symbology for fasteners, hardware, and materials. Also includes production of aircraft drawing, sketches, usage of aircraft schematics, graphs, charts, detail, assembly and exploded diagrams.
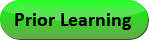.png)
Course Learning Outcomes
- Demonstrate proficient knowledge of mechanical drawings and their history
- Demonstrate proficient use of measurements and drawing techniques
- Demonstrate proficient use of blueprint references and standards
- Demonstrate proficient ability to interpret and apply print data
Outline:
- Basic Concepts of Blueprint Layout (0.5 class hours)
- History
- Manufacturing usage
- Repair and modification C.A.D. drawings
- Measurement Tools (2.0 class hours)
- Scale reading in 1/16 inch, 1/10 inch increments
- Micrometer reading
- Measurement transfer tooling
- Drawing and Layout Equipment (1.0 class hours)
- Dividers
- T-square
- Triangles
- Compass
- Curves
- Templates
- Radius gauges
- View and Projections (1.0 class hours)
- Perspective
- Oblique
- Isometric
- Types of Drawing Lines (4.0 class hours)
- Object
- Hidden
- Phantom
- Centerline
- Extension
- Dimension
- Cutting plane
- Leader
- Reference Lines (2.0 class hours)
- Water line (WL)
- Buttock line (BL)
- Fuselage station (FS)
- Wing station (WS)
- FFS front spar station
- Wing buttock line (SBL)
- Mean aerodynamic chord (MAC)
- Leading edge (L.E.)
- Trailing edge (T.E.)
- Zone diagrams
- Body section
- Access doors and panels
- Types of Drawings (4.0 class hours)
- Detail
- Assembly
- Installation
- Production
- Schematics
- Exploded diagrams
- Drawing Format (4.0 class hours)
- Nomenclature
- Drawing number
- Numbering of pages
- Scale
- Revisions
- Left and right parts
- Part numbers
- Approvals
- Zoning
- List of materials
- Drawing Techniques (10.0 class hours)
- Pencil lines
- Use of compass
- Use of the T-square
- Use of dividers
- Dimensioning and tolerances
- Lettering
- Title block development
- Sketches
- Production and Repair Standards Usage (0.5 class hours)
- Military standards (MS)
- Structural repair manuals
- Army Navy (AN)
- Aircraft Blueprint Interpretations (3.0 class hours)
- Use of prints for transfer of information
- Interpretation of the presented format
- Interpretation of charts and graphs
- Applicability of notes and instructions
- Charts and Graphs
- Typical layout
- Usage
Effective Term: Fall 2019 |
|
-
AVM 114 - Regulatory Requirements 3 Credits, 3 Contact Hours 3 lecture periods 0 lab periods
Federal Aviation Administration (FAA) regulatory requirements. Includes certification of aircraft and components, FAA regulations for aircraft maintenance, FAA publications, manufacturing standards, inspection requirements, maintenance, mechanic certification, maintenance publications and forms, and aircraft logs.
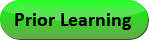.png)
Course Learning Outcomes
- Demonstrate proficient knowledge of aircraft certifications and regulations
- Demonstrate proficient knowledge of aircraft publications
- Demonstrate proficient knowledge of aircraft inspections
- Demonstrate proficient knowledge of aircraft records and forms
Outline:
- Certification
- Terms and abbreviations
- Part 23 aircraft
- Part 25 aircraft
- Experimental
- Restricted
- Limited
- Special use
- Aircraft specifications and type certificate data sheets
- FAA Regulations
- Part 1
- Part 21
- Part 23
- Part 25
- Part 39
- Part 43
- Part 61
- Part 65
- Part 91
- Part 121
- Part 135
- Part 145
- Part 147
- FAA Publications
- Advisory circular
- Alerts
- Airworthiness directives
- Manufacturing standards
- Type certificates (TC)
- Aircraft specifications
- Aircraft listings
- Supplemental type certificates (STC)
- Parts manufacturers approvals (PMA)
- Technical standard orders (TSO)
- ATA specification 100
V. Inspection Requirements
- Preflight
- 50 hour
- 100 hour
- Annual
- Progressive
- Check system
- Maintenance
- Preventive
- Alterations
- Rebuilding
- Minor repairs and alterations
- Major repairs and alterations
- Certifications of Mechanics
- Eligibility requirements
- Repairmen
- Airframe
- Powerplant
- Inspection authorization
- Duration of certificates
- Maintenance Publications
- Service bulletin (SE)
- Service manual (SM)
- Maintenance manual (MM)
- Illustrated parts catalog (IPC)
- Structural repair manual (SRM)
- Overhaul manual (OM)
- Operation manual
- Maintenance Forms and Logs
- FAA Form 337
- Acceptable data
- Approved data
- Field approval
- 8130-3 form
- Colored tag system
- Aircraft maintenance records
- Aircraft log books
Effective Term: Fall 2019 |
|
-
AVM 130 - Aircraft Composite Repair I 3.5 Credits, 8 Contact Hours 1.25 lecture periods 6.75 lab periods
Construction and repair processes using advanced composite materials. Includes reinforcing fibers, matrix and core materials, manufacturing of components, composite safety, curing wet layup and prepreg repairs, tools and equipment, and inspection and damage assessment.
Information: Consent of instructor is required before enrolling in this course.
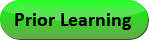.png)
Course Learning Outcomes
- Demonstrate proficient knowledge of composite materials and nomenclature
- Demonstrate proficient knowledge of composite fabrication and curing
- Demonstrate proficient knowledge of applicable safety procedures and machine operation
- Demonstrate proficient knowledge of various composite repair techniques
Outline:
- Material and Nomenclature
- Types and applications of reinforcing fibers
- Fiberglass cloth
- Aramid fabrics
- Carbon graphite
- Fiber placement
- Fiber usage
- Fabric styles
- Ply orientation
- Matrix Materials
- Matrix systems
- Thermo sets
- Thermo plastics
- Lay-ups
- Wet
- Prepreg
- Core Materials
- Honeycomb
- Foam cores
- Wood cores
- Fabrication and Curing
- Manufacturing of components
- Heat and pressure
- Manufacturing methods
- Lighting protection
- Electrical bonding
- Composite part finishing
- Curing and Repairs
- Room temp cures
- Vacuum bagging
- Heat curing - hot bonders
- Heat curing - oven
- Safety Procedure and Machine Operation
- Composite Safety
- Material safety data sheets
- Personal safety with chemicals
- Solvents: usage and safety
- Personal safety while machining
- Tools and equipment
- Cutting fabrics
- Machining cured composites
- Machining acrylics
- Facilities
- Repair Techniques
- Assessment of damage
- Classification of damage
- Types of damage
- Inspection methodology
- Repair operations
- Repair procedures
- Types of Repairs
- Declamation
- Disbonding
- Typical repair procedures
- Damage to monolithic laminate structure
- Repairs to honeycomb structures
- Repairs to thermoplastics
- Repair Procedures
- Structural Repair Manual (SRM) procedures
- Fiberglass monolithic lay-up
- Fiberglass sandwich lay-up
- Aramid fiber sandwich lay-up
- Carbon fiber sandwich lay-up
- Single sided step sand repair
- Single sided scarf repair
- Double sided scarf repair
- Edge band repair
- Thermo plastic bond
- Fastener installations
Effective Term: Full Academic Year 2021/22 |
|
-
AVM 150 - Aircraft Sheet Metal Repair III 4 Credits, 8 Contact Hours 2 lecture periods 6 lab periods
Continuation of AVM 106 . Includes repair publications, materials handling, cable fabrication, machining processes, protective coatings, hand forming and structural repair processes.
Prerequisite(s): AVM 106
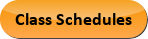
Course Learning Outcomes
- Demonstrate the use of the Structural Repair Manual (SRM), Illustrated Parts Catalog (IPC), Service Bulletins (SBs), Airworthiness Directives (ADs), Supplemental Type Certificates (STCs), and Engineering Orders (EOs).
- Describe the methods of material handling and material verification.
- Describe and demonstrate drilling, reaming, heli-coil installation, routing, spot facing, counter boring, torqueing, and jigging.
- Describe and demonstrate coating applications.
- Describe and demonstrate hand forming of flanges, concave curvatures, and convex curvatures.
- Describe layout procedures and perform dent repair, web repair, skin repair, and spar repair.
Outline:
- Repair Publication Use
- SRM
- IPC
- SBs
- ADs
- STCs
- EOs
- Blueprint reading
- Materials Handling and Verification
- Rules of handling sheet metal
- Importance of verification
- Methods of verification
- Hardness testing identification
- Special Machining Processes
- Drilling and reaming tooling
- Drilling and reaming of close tolerance hardware and fittings
- Rivet shaver
- Routing procedures
- Spot facing application and tooling
- Spot facing procedures
- Counter boring application and tooling
- Counter boring procedures
- Torque applications
- Jig and fixture building
- Protective Coatings
- Alodine treatment
- Anodizing
- Primers and applications
- Final coatings and application
- Hand Forming
- Tooling fabrication
- Forming flanges
- Forming concave curvatures
- Forming convex curvatures
- Repair Processes
- Dent repairs
- Web repairs
- Skin repairs
- Spar repair
- Rib repair
Effective Term: Full Academic Year 2021/2022 |
|
-
AVM 151 - Aircraft Sheet Metal Repair IV 4 Credits, 8 Contact Hours 2 lecture periods 6 lab periods
Continuation of AVM 150 . Includes locking fasteners, damage classifications, and structural repair processes.
Prerequisite(s): AVM 150
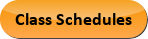
Course Learning Outcomes
- Describe the types, materials and sizing of special locking fasteners.
- Demonstrate the use of locking fasteners in structural repair procedures.
- Define and use damage classifications according to the Structural Repair Manual (SRM).
- Use the SRM and the Illustrated Parts Catalog (IPC) to determine repair and replacement requirements.
- Describe layout procedures and perform pressurized repair, flush skin and frame repair to heavy materials.
Outline:
- Special Locking Fasteners
- Types, Materials and Sizing
- Installation Procedures for the following:
- Dzus
- Camlock
- Airlock
- Paneloc
- Zip-loc
- Milsou
- Calfac
- Damage Classifications
- Definitions
- Allowable damage
- Repairable damage
- Replacement of the part
- Damage beyond allowable limits
- Hole preparation and stop drilling of cracks
- Use of the SRM to identify type of damage
- Repair and Replacement Requirements
- Use of the SRM to determine repair procedures
- Use of the IPC to determine parts replacement and effectiveness
- Repair Processes
- Pressurized repairs
- Flush skin repair - heavy material
- Frame repair - heavy material
- External patch repair
Effective Term: Full Academic Year 2021/2022 |
|
-
AVM 165 - Aircraft Hardware and Fasteners 3 Credits, 3 Contact Hours 3 lecture periods 0 lab periods
Aircraft structural repair hardware and fasteners. Includes specifications and standards, types, control linkages, tubing, hose and packings.
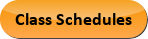
Course Learning Outcomes
- Describe characteristics and properties of aircraft metals.
- Identify material types through designation numbering.
- Describe and classify types of corrosion found in aircraft and determine the methods of removal and treatment.
- Describe destruction and non-destruction testing methods and applications used in aircraft repair.
- Use characteristics and properties of ferrous and non-ferrous metals in aircraft.
Outline:
- Aircraft Structural Materials
- Usage
- Mechanical properties
- Chemical properties
- Electrical properties
- Thermal properties
- Stress versus strain
- Fatigue
- Non-ferrous Metals
- Use in aircraft
- Characteristics and properties
- Forming and mechanical working
- Alteration of mechanical properties through thermal treatments
- Corrosion
- Heat treatment procedures
- Ferrous Metals
- Use in aircraft
- Characteristics and properties
- Forming
- Thermal treatments
- Corrosion
- Heat Treatment Procedures
- Surface Treatments for Ferrous and Non-ferrous Metals
- Aluminum cladding
- Case hardening of ferrous material
- Alloying of Ferrous and Non-ferrous Metals
- Reasons for alloying
- Alloying elements and designations for aluminum
- Alloying elements and designations for steel
- Alloying elements and designations for magnesium
- Alloying elements and designations for titanium
- Special alloys
- Corrosion in Aircraft Structural Materials
- Understanding corrosion and its causes
- Classifying corrosion
- Detection methods
- Removal
- Treatment and prevention
- Destruction Testing of Structural Materials
- Impact
- Tensile
- Hardness
- Chemical
- Non-Destructive Testing of Structural Material
- Theory
- Magnetic particle
- Penetrant
- Eddy current
- Ultra-sonic
- X-Ray
Effective Term: Spring 2010 |
|
-
AVM 202 - Aviation Safety 2.5 Credits, 5 Contact Hours 1.25 lecture periods 3.75 lab periods
Introduction to aviation safety procedures. Includes personal safety issues, human factors, accident avoidance, facility fire protection, hazardous materials safety and handling procedures, ramp procedures for movement, and securing and servicing of aircraft and ramp support equipment. Also includes forklift and scissors lift training.
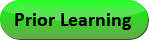.png)
Course Learning Outcomes
- Demonstrate proficient knowledge of personal, shop, and ramp safety
- Demonstrate proficient knowledge of potential aircraft hazards
- Demonstrate proficient knowledge of aircraft handling
- Demonstrate proficient knowledge of ground equipment handling
Outline:
- Personal Safety
- Define terms related to safety
- Discuss general safety practices and precautions
- Discuss personal safety practices and equipment
- List steps to be followed in case of an accident
- Human Factors
- Physiology
- Personal habits
- Attitudes towards the workplace
- Accident avoidance
- Shop and Hangar Safety
- Standard safety procedures
- Emergency evacuation procedures
- Hazards of shop floor equipment
- Hazard tags and markings
- Electrical and chemical shutdown procedures
- Ramp Safety
- Standard safety procedures
- Emergency evacuation procedures
- Hazard zone and ramp markings
- Precautions around aircraft
- Pneumatic, electrical and fuel shutdown procedures
- Hazardous Aircraft
- Obstructions
- Grounding
- Fire
- Radiation
- Turbine engine hazards
- Piston and propeller hazards
- Movement of aircraft
- Securing
- System hazards
- Hazardous Material Handling
- Safety equipment
- Storage
- Disposal
- Material Safety Data Safety Sheet (MSDA) data
- Handling precautions
- Fire Safety
- Types of fires
- Proper extinguishing equipment
- Use of extinguishers
- Protective equipment
- Confined Space
- Ventilation
- Precautions
- Aircraft Ground Handling
- Terms
- Chalking and tie down
- Ground support equipment
- Jacking and hosting
- Cleaning
- Servicing
- Fuel contamination hazards
- Fueling
- De fueling
- Selection of proper fuel grades
- Landing gear and control surface locks
- Aircraft Movement and Ground Operations
- Terms
- Standard hand signals
- Start-up procedures
- Prop
- Turbine
- Air Traffic Control (ATC) procedures
- Movement on airports
- Towing of aircraft
- Forklift and Scissors Lift Operation
- Terms
- Equipment capabilities
- Safety precautions
- Safety procedures
- Operation
- Securing techniques
Effective Term: Full Academic Year 2021/2022 |
|
-
AVM 203 - Aircraft Sheet Metal Repair V 4 Credits, 8 Contact Hours 2 lecture periods 6 lab periods
Continuation AVM 151 . Includes jigging, shoring and alignment, corrosion and heat treatment and structural repair processes.
Prerequisite(s): AVM 151
Course Learning Outcomes
- Describe the procedures for jigging, shoring, leveling and aligning aircraft.
- Describe safety and emergency safety procedures in the handling and use of corrosion treatment chemicals.
- Demonstrate corrosion control of ferrous and non-ferrous aircraft structures.
- Demonstrate corrosion control of plated aircraft parts.
- Describe the principles and processes of heat treatment for aluminum structures and carton steel alloys.
- Demonstrate the heat treatment of aluminum alloys.
- Demonstrate layout and repair of aircraft control surfaces.
- Demonstrate balancing of flight control surfaces.
- Demonstrate use of reader and printer.
Outline:
- Jigging, Shoring, and Alignment
- Requirement
- Shoring techniques
- Jigging requirements
- Alignment determination techniques
- Jacking and leveling
- Corrosion Treatment
- Safety procedures
- Emergency safety procedures
- Corrosion damage and rework limits
- Corrosion removal techniques
- Identification of metals
- Corrosion removal for aluminum alloys
- Corrosion removal for magnesium
- Corrosion removal for carbon steel
- Corrosion removal for titanium alloys
- Corrosion removal for chromium and nickel plated parts
- Corrosion removal for cadmium plated parts
- Heat Treatment
- Basic principles of heat treatment for ferrous and non-ferrous metals
- Equipment
- Temperatures
- Soaking
- Quenching
- Natural and artificial aging
- Temper designations
- Hardness
- Strength specifications
- Corrosion problems
- Cracking
- Quality assurance techniques
- Heat treatment of aluminum alloys
- Structural Repair Processes
- Layout and perform control surface repairs
- Balance control surfaces
- Stringer repairs
- Frame repairs
Effective Term: Full Academic Year 2021/2022 |
|
-
AVM 204 - Aircraft Sheet metal Repair VI 4 Credits, 8 Contact Hours 2 lecture periods 6 lab periods
Continuation of AVM 203 . Includes sealants and sealant applications, heat treatment, plastics and plastic repairs and structural repair processes.
Prerequisite(s): AVM 203
Course Learning Outcomes
- Describe aircraft sealant materials, use and safety.
- Demonstrate sealant application.
- Demonstrate heat treatment and tempering of alloy steels.
- Demonstrate layout and repair of formed sections.
- Demonstrate layout and repair of extruded sections.
Outline: I. Sealants - General
A. Basic concept and definitions
B. Sealing materials
C. Types of sealant applications
D. Sealing equipment
E. Storage of sealant
F. Preparation of sealants
G. General safety precautions
H. Inspection requirements
II. Sealant Application
A. Sealant application technique
B. Sealing fuel tanks
C. Sealing structural repairs
D. Sealing pressure vessels
E. Specialized curing techniques
III. Heat Treatment
A. Basic heat treatment of alloy steels
B. Tempering for specific properties
IV. Structural Repair Processes
A. Formed section repair
B. Extruded section repair
Effective Term: Full Academic Year 2021/2022 |
|
-
AVM 205 - Motion Dynamics 2.5 Credits, 5 Contact Hours 1.25 lecture periods 3.75 lab periods
Principles of hydraulic power. Includes basic physics, basic mechanics, heat and fluid dynamics, fabrication and installation of fluid lines and fittings, laws of motion, basic aerodynamics, and aircraft nomenclature.
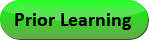.png)
Course Learning Outcomes
- Demonstrate proficient knowledge of basic physics and mechanics
- Demonstrate proficient knowledge of hydraulic theory
- Demonstrate proficient knowledge of aerodynamic theory
- Demonstrate proficient knowledge of common aircraft nomenclature
Outline:
- Basic Physics
- Terms
- Principles of physics
- States of matter
- Laws of motion
- Potential energy
- Kinetic energy
- Simple Mechanics
- Stresses
- Leverage
- Stored energy
- Ratios
- Sound, Heat, and Fluid Dynamics
- Heat and energy
- Heat transfer
- Sound transmission
- Temperature monitoring
- Pressure types
- Pressure monitoring
- Hydraulic Lines and Fittings
- Rigid lines
- Flexible lines
- Standard fittings
- Military Standard (MS), Army, Navy Standard (AN), and Advisory Circular (AC) standards
- Tooling
- Fabrication methods
- Basic Aerodynamics
- Forces of flight
- Physics of aerodynamics
- Airfoils
- Atmospheric conditions
- Center of pressure
- Supersonic flight
- Axis of an aircraft
- Stalls
- Control around the axis
- Speed, pitch, roll control
- Aircraft nomenclature
- Primary structure
- Primary flight controls
- Secondary flight controls
- Cockpit controls
- Cowlings and nacelles
- Skins and fairings
- Landing gear
- Panels and doors
- Wing types
- Empennage types
- Bundy layer control
Effective Term: Full Academic Year 2021/2022 |
|
-
AVM 206 - Materials and Processes 3 Credits, 6 Contact Hours 1.5 lecture periods 4.5 lab periods
Introduction to non-metallic and metallic structural materials for comparison of their structural properties. Includes structural materials, metal processing, heat treatment, heat treatment of alloys or limited use metals, non-destructive testing/inspection, corrosion, corrosion types and factors, corrosion-prone areas, corrosion control: steel, aluminum, and limited use metals, processes and materials for corrosion control, aircraft cleaning, and aircraft cleaning agents.
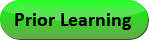.png)
Course Learning Outcomes
- Demonstrate proficient knowledge of common materials and processes
- Demonstrate proficiency in the identification and use of various types of aircraft hardware
- Demonstrate proficient knowledge in non-destructive testing and inspection
- Demonstrate proficient knowledge of aircraft cleaning and corrosion control processes
Outline:
- Materials and Processes
- Properties of metals
- Hardness
- Strength
- Density
- Malleabitlity
- Ductility
- Elasticity
- Toughness
- Brittleness
- Fusibility
- Conductivity
- Thermal expansion
- Ferrous aircraft metals
- Types
- Identification
- Spark test
- SAE and AISI numerical indexes
- Electrochemical testing
- Non-Ferrous aircraft metals
- Aluminum and aluminum alloys
- Wrought aluminum
- Alloying elements
- Hardness identification
- Magnesium and magnesium alloys
- Titanium and titanium alloys
- Copper and copper alloys
- Nickel and nickel alloys
- Substitution of aircraft metals
- Metal processes
- Hot working
- Cold working
- Extuding
- Forging
- Casting
- Internal structure of metal
- Heat treatment equipment
- Furnaces and salt bath
- Temperature measurement and control
- Heating
- Soaking
- Cooling
- Quenching
- Heat treatment of ferrous metals
- Behavior of steel
- Hardening
- Tempering
- Annealing
- Normalizing
- Casehardening
- Heat treatment of nonferrous metals
- Aluminum alloys
- Alclad aluminum
- Solution heat treatment
- Quenching
- Lag time
- Reheat treatment
- Straightening
- Precipitation
- Annealing
- Aluminum rivets
- Heat treatment of aluminum alloy rivets
- Compositions
- Time
- Temperature
- Heat treatment of magnesium alloys
- Solution
- Precipitation
- Heat treatment of titanium
- Stress relieving
- Full annealing
- Thermal hardening
- Casehardening
- Hardness testing
- Brinell tester
- Rockwell tester
- Barcol tester
- Forging
- Hot forging
- Drop forging
- Casting
- Strength
- Metals
- Extruding
- Process
- Metals
- Cold working/hardening
- Cold rolling
- Cold drawing
- Nonmetallic aircraft metals
- Wood
- Plastic
- Composite materials
- Fiber reinforced material
- Reinforced plastic
- Rubber
- Shock absorber cord
- Seals
- Packings
- V-ring
- U-ring
- Gaskets
- Wipers
- Sealing compounds
- Identification and Use of Aircraft Hardware
- Aircraft hardware
- Idenfification
- Threaded fasteners
- Aircraft bolts
- Special-purpose bolts
- Aircraft nuts
- Non-self-locking nuts
- Self-locking nuts
- Sheet spring nuts
- Internal and external wrenching nuts
- Identification coding
- Washers
- Lock washers
- Special washers
- Installation of nuts, washers, and bolts
- Bolt and hole size
- Installation practices
- Repair of damaged internal threads
- Bushings
- Helicoils
- Fastener torque
- Torque wrenches
- Torque tables
- Cotter pin line up
- Aircraft rivets
- Standards and specifications
- Solid shank
- Identification
- Mechanically-expanded
- Material
- Head styles
- Diameters
- Grip length
- Special and bearing load fasteners
- Pin rivet
- Taper-lok
- Hi-tigue
- Captive
- Turn lock
- Dzus
- Camloc
- Airloc
- Screws
- Structural
- Machine
- Self-tapping
- Identification
- Riveted and rivetless nut plates
- Nut plates
- Rivuts
- Drill Lok
- Deutsch
- Sealing
- Hole repair
- Blind rivets
- Acres fastener
- Control cables and turnbuckles
- Construction
- Fittings
- Turnbuckles
- Push-pull linkage
- Safetying methods
- Pins
- Safety wire
- Nuts, bolts, and screws
- Oil caps, drain cocks, and valves
- Electrical connectors
- Turnbuckles
- General safety wire rules
- Snap rings
- Pliers
- Reuse
- Precision measuring equipment
- Micrometer caliper
- Dial indicator
- Telescopic gauges
- Slide caliper
- Non-Destructive Testing (NDT) and Inspections
- NDT
- Training, qualification, and certification
- Visual inspection
- Liquid penetrant inspection
- Eddy current inspection
- Ultrasonic inspection
- Magnetic particle inspection
- Radiographic inspection
- Magnetic particle
- Inspection of welds
- Speed
- Voltage
- Current
- Temperature
- Corrosion and Cleaning
- Factors affecting corrosion
- Climate
- Location
- Foreign material
- Micro-organisms
- Manufacturing process
- Types of corrosion
- Direct chemical attack
- Electrochemical attack
- Forms of corrosion
- Surface
- Filiform
- PItting
- Dissimilar metal
- Concentration cell
- Intergranular
- Exfoliation
- Stress
- Fretting
- Fatigue
- Galvanic
- Common corrosive agents
- Acids
- Alkalies
- Salts
- Atmosphere
- Water
- Preventative maintenance
- Surface finishing
- Inspections
- Corrosion prone areas
- Exhaust
- Battery area
- Bilge
- Lavatories
- Wheel well and landing geer
- Water entrapment areas
- Engine areas
- Wing flaps
- Electronics
- Corrosion removal
- Surface cleaning
- Blending
- Corrosion of ferrous metal
- Mechanical removal
- Chemical removal
- Chemical treatment
- Corrosion treatment
- Aluminum
- Magnesium
- Titanium
- Protection of dissimilar metals
- Treatment
- Corrosion limits
- Chemical treatment
- Anodizing
- Alodizing
- Inhibitors
- Chromic acid
- Sodioum dichromate
- Chemical surface
- Aircraft cleaning
- Exterior
- Interior
- Powerplant
- Solvent cleaners
- Emulsion cleaners
- Mechanical cleaners
- Chemical cleaners
Effective Term: Full Academic Year 2021/22 |
|
-
AVM 207 - Weight and Balance 1.5 Credits, 3 Contact Hours .75 lecture periods 2.25 lab periods
Preparation of aircraft for weight and balance. Includes service and maintenance manuals, type certificate data sheets, standard weight and balance practices, weighing an aircraft, calculating center of gravity, and correction of out of balance conditions. Also includes addition and subtraction of equipment, equipment lists, flight manual updates, control surface balancing, identification and selection of standard hardware, installation and assembly of specialty hardware, and use of precision measuring equipment.
Prerequisite(s): GTM 105V
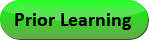.png)
Course Learning Outcomes
- Demonstrate proficient knowledge of aircraft weight and balance theory and terms
- Demonstrate proficient knowledge of aircraft weight and balance procedures and equipment
- Demonstrate proficiency performing aircraft center of gravity calculations
- Demonstrate proficiency performing adverse loading calculations
Outline:
- Theory and Terms
- Weight and balance (W&B) theory
- Need for weighting
- Flight operational concerns
- Controllability
- Safety of flight
- Principles of W&B
- W&B terms
- Datum
- Arm
- Moment
- Center of gravity (CG)
- Maximum weight
- Empty weight (EW)
- EWCG
- Useful load
- Minimum fuel
- Tare weight
- W&B Procedures and Equipment
- Procedures for weighing
- General concepts
- W&B data
- Manufacturer-furnished information
- W&B equipment
- Scales
- Spirit level
- Plumb bob
- Hydrometer
- Preparing an aircraft for weighing
- Fuel system
- Oil system
- Miscellaneous fluids
- Flight controls
- Other considerations
- Weighing point
- Jacking and leveling the aircraft
- Precautions
- Longitudinal adjustments
- Lateral adjustments
- Safety considerations
- Calculcating CG
- CG range
- Location
- CG limit
- EWCG
- Operating CG
- Standard weights used for W&B
- Fuel
- Oil
- Water
- Crew
- CG formulas
- EWCG
- Datum forward of CG
- Datum aft of main wheels
- Location of datum
- Loading an aircraft for flight
- Responsibility
- TCDS data
- Loaded weight
- Maximum take-off weight
- Adverse-loaded CG Checks
- Forward and Aft check
- Equipment change and aircraft alteration
- Calculations
- Use of Ballast
- Temporary ballast
- Permanent ballast
- Ballast calculations/formulas
- Loading graphs and CG envelopes
- Manufacture use
- Pilot use
- Helicopter W&B
- General concepts
- Helicopter weighing
- Helicopter leveling
- Weight-shift control aircraft and powered parachutes
- Weight-shift aircraft
- Powered parachutes
- W&B for large airplanes
- Built-in electronic weighing
- Mean aerodynamic chord (MAC)
- Leading edge MAC
- CG range
- Percent of MAC
- W&B records
- FAA requirements
- W&B report
Effective Term: Full Academic Year 2021/22 |
|
-
AVM 208 - Basic Electricity 3.5 Credits, 8 Contact Hours 1.25 lecture periods 6.75 lab periods
Introduction to basic aircraft electricity. Includes the study of matter, electron theory, current/electron flow, direct and alternating current, Ohm’s Law, Kirchoff’s laws, circuit elements, use of testing equipment, and electrical calculation and measurements. Also includes interpretation of schematics and other wiring diagrams, battery theory and maintenance, aircraft electrical systems, and introduction to communication and navigation radio systems.
Prerequisite(s): GTM 105V
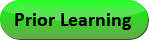.png)
Course Learning Outcomes
- Demonstrate proficient knowledge of DC theory and circuits
- Demonstrate proficient knowledge of AC theory
- Demonstrate proficient knowledge of voltage generation and control elements
- Demonstrate proficient knowledge of various aircraft electrical systems
Outline:
- Basic Electron and Electrical Theory
- Types of current and voltage
- Units of electrical measurement
- Powers of ten and scientific notation
- Static electricity
- Electric and magnetic fields (EMF)
- Ohm’s Law
- Resistance, conductors, and insulators
- Sources of electric energy
- Direct Current (DC) and Alternating Current (AC)
- DC (series parallel and grid circuits)
- Ohm’s Law
- AC
- Use of Test Equipment to Measure Continuity, Voltage, Current, Resistance, Inductance and Capacitance
- Circuit elements
- Capacitors, resistors, and inductors
- Switches
- Protective devices
- Volt-Ohm multimeters
- DC power supplies
- High potential testers and harness testers
- LCR meter for inductance and capacitance
- Signal generators
- Generators, Motors, Ignition Systems, and Magnetos
- Magnetic theory
- Inductance
- Aircraft Batteries
- Lead acid batteries
- Nickel cadmium batteries
- Battery maintenance and safety
- Wiring
- Wire type and size
- Wire installation
- Troubleshooting
- Aircraft Lighting Systems
- Exterior lighting
- Landing lights
- Taxi lights
- Federal Aviation Administration (FAA) and Federal Aviation Regulations (FARs)
- Weight and balance
- Problem solving
- Aircraft modifications
- Communication and Navigation Systems
- Audio systems, microphones, speakers and headsets
- Communication systems
- Navigation systems
Effective Term: Full Academic Year 2021/22 |
|
-
AVM 209 - Intermediate Electricity 3.5 Credits, 8 Contact Hours 1.25 lecture periods 6.75 lab periods
Intermediate electricity includes the study of aircraft airframe electrical components as well as airframe and powerplant electrical systems. Includes electric motors, generators and generator controls, alternators, inventers and related controls, power distribution systems, design and maintenance of aircraft electrical systems, digital electronics, analog electronics, communication and navigation systems, communications, weather warning systems, and electric instruments and autoflight systems.
Prerequisite(s): AVM 208
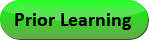.png)
Course Learning Outcomes
- Demonstrate proficient knowledge of motors and generators
- Demonstrate proficient knowledge of alternators and inverters
- Demonstrate proficient knowledge of power distribution systems
- Demonstrate proficient knowledge of instrumentation systems
Outline:
- Electric Motors
- Motor theory
- Motor construction
- AC motors
- Inspection and maintenance
- Generators and Generator Controls
- Generator theory
- Direct Current (DC) generator construction
- Starter-Generators
- Generator control
- Generator inspection, service and repair
- Alternating Current (AC) generators
- Voltage regulators
- Inverters,
- Variable speed, constant frequency power systems
- Alternators, Inverters and Related Controls
- AC generators
- Voltage regulators
- Inverters and static inverters
- Variable-speed constant-frequency power systems
- Power Distribution Systems
- Requirements for power distribution systems
- Main power distribution systems
- Power distribution in composite aircraft
- Large aircraft power distribution
- Design and Maintenance of Aircraft Electrical Systems
- Requirements for electrical systems
- Aircraft lights
- Large aircraft electrical systems
- Maintenance and troubleshooting of electrical systems
- Digital Electronics
- Logic gates
- Integrated circuits
- Large scale and very large scale integrated circuits
- Microprocessors
- Application specific integrated circuits
- Digital aircraft systems
- Troubleshooting digital circuits and systems
- Analog Electronics
- DC amplifiers
- Radio frequency (RF) amplifiers
- Audio amplifiers
- Power supplies
- Control circuits
- Communication and Navigation Systems
- Communications
- Navigation
- Long range navigation
- Installation of avionics equipment
- Antennas
- Weather Warning Systems
- Radar
- Digital airborne weather radar
- Weather mapping systems
- Electric Instruments and Autoflight Systems
- Revolutions per minute (RPM) measuring instruments
- Temperature indicators
- Synchro systems
- Fuel quantity indicators
- Electromechanical flight instruments
- Electronic flight systems
- Automatic flight control systems
- Autoflight and landing systems
- Flight management systems
- Strap-down gyro system
Effective Term: Full Academic Year 2021/22 |
|
-
AVM 211 - Alternate Structures 3.5 Credits, 8 Contact Hours 1.25 lecture periods 6.75 lab periods
Aircraft structural fabrication using wood, tube steel and fabric processes and techniques. Includes structural types, wood and welded tube steel fabrication methods, welding of typical metals used in aircraft construction, fabric covering processes, inspection and maintenance typical repair procedures, and aircraft finishings.
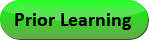.png)
Course Learning Outcomes
- Demonstrate proficient knowledge of wooden aircraft structures
- Demonstrate proficient knowledge of welded aircraft structures
- Demonstrate proficient knowledge of fabric aircraft coverings
- Demonstrate proficient knowledge of aircraft finishes
Outline:
- Wood Structures
- Terms
- Fuselage
- Wing
- Typical applications
- Wood
- Types
- Defects
- Decay
- Fastening
- Adhesives
- Metal fasteners
- Wood Machining
- Cutting
- Sanding
- Preparation for joining
- Installation of fasteners
- Wood Repairs
- Identification of damage
- Inspection
- Replacement
- Scarf joints
- Splicing
- Patches
- Finishing Wood Structure
- Precautions
- Surface
- End grain
- Sealing holes
- Tubular Structures
- Terms
- Fuselage
- Landing gear
- Typical applications
- Metals
- Types and alloys
- Harness indicators
- Machining
- Cutting
- Drilling
- Sanding/grinding
- Forming
- Fabrication of joints
- Welding, Brazing, and Soldering
- Types of welding
- Brazing
- Soldering
- Equipment
- Gas welding
- F. Shielded metal arc (stick)
- Gas metal arc (MIA)
- Gas tungsten arc (TIA)
- Welded Repairs
- Joints
- Fit and preparation
- Selection of materials
- Precautions and safety
- Non-repairable structures
- Fabric Materials
- Terms
- Type of fabric
- Applications
- Typical Installation
- Fastening materials
- Attachment to structure
- Shrinking
- Reinforcing
- Lacing
- Sewing
- Openings
- Coatings
- Dopes
- Sealers
- Sanding
- Defects
- Repairs
- Precautions
- Sewn patch
- Doped on patch
- Refinishes
- Finishes and Paints
- Paint types
- Thinning
- Catalyzing
- Cleanup
- Environmental
- Equipment
- Finish Trims Striping
- Numbers and lettering
- Touchup
- Masking
- Decals
- Defects
- Orange peel
- Sags and runs
- Fisheye
- Scratches
- Scuffing
- Repairs
- Inspection
- Sanding
- Matching
- Blending
- Polishing
Effective Term: Full Academic Year 2021/22 |
|
-
AVM 218 - Airframe Rigging and Landing Gear Systems 2.5 Credits, 5 Contact Hours 1.25 lecture periods 3.75 lab periods
Identification, assembly, alignment, balancing and rigging of aircraft rigging and landing gear systems. Includes aircraft nomenclature, characteristics of flight, flight control system, airframe assembly, rigging, structural alignments, control surface balancing, landing gear, shock struts, landing gear retraction, wheel alignment and steering, brake system servicing, brake assemblies, wheels, tires, warning systems, and anti-skid system.
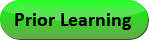.png)
Course Learning Outcomes
- Demonstrate proficient knowledge of aircraft rigging and balancing procedures
- Demonstrate proficient knowledge of aircraft landing gear systems
- Demonstrate proficient knowledge of aircraft position and warning systems
- Demonstrate proficient knowledge of aircraft inspection and servicing procedures
Outline:
- Aircraft Nomenclature
- Fuselage types
- Wing types
- Empennage types
- Flight controls
- Primary
- Secondary
- Landing gear types
- Characteristics of Flight
- Flight about the axis
- Lift vs. drag
- Stability
- static
- Dynamic
- Longitudinal
- Directional
- Lateral
- Thrusts
- Torque
- Flight Control System
- Flight controls
- Primary
- Secondary
- Mechanical linkage
- Hydraulic/mechanical
- Artificial feedback
- Control locks (external)
- Airframe Assembly
- Technical data
- Special tooling
- Jigs and fixtures
- Rigging
- Positioning
- Surface travel
- Cable tensioning
- Rig pin and locks
- Fixtures and templates
- Structural Alignments
- Symmetry checks
- Alignment
- Dihedral
- Incidence
- Instruments (measurement)
- Control Surface Balancing
- Principles
- Rebalancing
- Static balance
- Dynamic balance
- Tools and fixtures
- Landing Gear, and Shock Struts
- Nomenclature
- Principles of operation
- Servicing and maintenance
- Landing Gear Retraction
- Support structure
- Nomenclature
- Electrical actuation
- Hydraulic actuation
- Manual actuation
- Emergency extension
- Positions indicating
- Rigging/adjustment
- Maintenance
- Inspection
- Wheel alignment/steering
- Torque links
- Centering cams
- Hose wheel steering
- Shimmy dampers
- Brake system servicing
- Maintenance
- Servicing
- Inspection
- Brake assemblies
- Single disc
- Multiple disc
- Segmented rotor
- Expander tube
- Brake system servicing
- Maintenance
- Servicing
- Inspection
- Wheels
- Split
- Flange
- Fixed
- Removable
- Bearings
- Axle
- Tires
- Construction
- Nomenclature
- Inflation issues
- Inspection
- Warning systems
- Gear warning systems
- Flap
- Throttle
- Stall warning
- Position indication
- Maintenance
- Inspection
- Anti-skid system
- System principles
- Airspeed vs. wheel speed
- Components
- Protection systems
Effective Term: Full Academic Year 2021/2022 |
|
-
AVM 219 - Airframe Inspections 2.5 Credits, 5 Contact Hours 1.25 lecture periods 3.75 lab periods
Conformity inspections of airframes. Includes inspections of incoming spare parts and stock items, airframe and equipment conformity inspections, airframe and systems airworthiness and conformity inspections, conformity inspections of installed equipment, annual and 100-hour inspections of small aircraft, including research of all pertinent inspection documents, service or maintenance manuals, type certificate data sheets, airworthiness directives, service bulletins and additional instructions for continued airworthiness, inspection procedures for large aircraft work orders, non-routine job cards used by local aviation maintenance companies.
Prerequisite(s): AVM 114
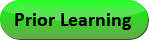.png)
Course Learning Outcomes
- Demonstrate proficient knowledge of aircraft inspection requirements
- Demonstrate proficient knowledge of aircraft documents
- Demonstrate proficient knowledge of repair station operations
- Demonstrate proficient knowledge of proper maintenance documentation
Outline:
- Safety
- Owner and operator responsibility
- Mechanic responsibility
- Inspector responsibility
- Minimum requirements
- Costs
- Aircraft ownership
- Operational
- Maintenance
- Insurance
- Airworthiness
- Definition
- Documents
- Maintainability
- Changes
- Unapproved Parts
- Definition
- Identification and labeling
- Alterations
- Inspection procedures
- Reporting
- Annual and 100 hour Inspections
- Preparation
- Documents for review
- Maintenance and service manual
- Using the check list
- Inspection requirements
- Service and maintenance
- Performing inspections
- Document Usage
- Use of maintenance publications
- Airworthiness directives, procedures
- Type certificate application
- Service bulletin application
- Instructions for continued airworthiness
- Equipment lists and minimums
- Aircraft log and maintenance records
- Progressive Inspections
- Applicability
- Breakdown of tasks
- Scheduling of maintenance and inspections
- Documentation
- Use of manufacturer data
- Equipment requirements
- Performing inspections
- Repair Station Requirements
- Certification
- Ratings
- Pertinent regulations
- Set-up and equipment
- Training
- Staffing
- Equipment
- Operating
- Documentation
- Inspection and maintenance sign offs
- Work orders
- Routine and non-routine
- Job cards
Effective Term: Fall 2019 |
|
-
AVM 223 - Hydraulic and Pneumatic Power 2.5 Credits, 5 Contact Hours 1.25 lecture periods 3.75 lab periods
Hydraulic and pneumatic system components. Includes system operating principles, fluids, pressures, hydraulic powered flight controls, landing gear, braking and accessory power systems, pneumatically powered or assisted accessories, and system and component inspection servicing and repairs.
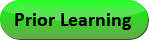.png)
Course Learning Outcomes
- Demonstrate proficient knowledge of aircraft hydraulic system components
- Demonstrate proficient knowledge of aircraft hydraulic system operation
- Demonstrate proficient knowledge of aircraft landing gear, flight control, and brake systems
- Demonstrate proficient knowledge of aircraft hydraulic system inspection, servicing, and repair
Outline:
- Hydraulic Fluids
- Viscosity
- Stability
- Types
- Precautions
- System Principles
- Needs for power
- Moving of fluid
- Routing and selector valves
- Basic components
- Reservoirs Types
- Features
- Servicing and inspection
- Filters
- Types
- Features
- Servicing and inspection
- Fluid Pumps
- Hand pumps
- Constant delivery
- Variable delivery
- Types
- Features
- Servicing and inspection
- Pressure Regulation
- Relief valves
- Regulators
- Indicating equipment
- Adjustment and servicing
- Accumulators
- Types
- Features
- Servicing
- Check Values
- Types
- Features
- Installations
- Actuating Cylinders
- Types
- Principles of operation
- Inspection and servicing
- Maintenance
- Selector Valves
- Operating principles
- Types
- Applications
- Hydraulic Power Systems
- Light A/C brakes
- Heavy A/C brakes
- Flight controls
- Steering
- Accessories
- Pneumatic Power Supply
- Pumps and supply
- Storage
- Precautions
- Pneumatic Power Equipment
- Control valves
- Pressure adjustment
- Restrictors
- Filters
- Maintenance and inspection
Effective Term: Full Academic Year 2021/2022 |
|
-
AVM 224 - Atmospheric Controls 2.5 Credits, 5 Contact Hours 1.25 lecture periods 3.75 lab periods
Atmospheric controls and its elements that are of concern to flight includes control systems; types of operations and maintenance; physiological requirements for flight crews, passengers, and the human support systems. Also includes oxygen systems; cabin pressurization system and their operations; and safety and maintenance requirements.
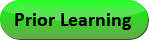.png)
Course Learning Outcomes
- Demonstrate proficient knowledge of aircraft oxygen systems
- Demonstrate proficient knowledge of aircraft cabin heat and vapor cycle systems
- Demonstrate proficient knowledge of aircraft bleed air systems air cycle machines
- Demonstrate proficient knowledge of aircraft pressurization systems
Outline:
- Atmosphere
- Composition of gasses
- Segments
- Pressure changes
- Temperature changes
- Heating and cooling of air masses
- Water vapor
- Oxygen Requirements
- Physiological needs
- Hypoxia
- Regulations
- Oxygen Storage
- Gaseous
- Liquid
- Solid
- Oxygen System Components
- Regulators
- Masks
- Supply lines
- Fittings
- Indicating
- Oxygen Systems Functions
- Continuous
- Demand
- Emergency
- Maintenance
- Handling of oxygen
- Installation and removal of components
- Servicing
- Inspection
- Hazards
- Heating Systems
- Exhaust gas heaters
- Cabin combustion heaters
- Electrical element
- Engine bleed air heating
- Ventilating Systems
- Air distribution
- Tempering air
- Air sources
- Indicating and sensors
- Air Conditioning (Cooling) Systems
- Vapor cycle principles
- Vapor cycle components
- Air cycle principles
- Air cycle components
- Pressurization
- Structural requirements
- Cabin pressure sources
- Cabin pressure control systems
- Pressurization system components
- Safety features
- Typical operations
Effective Term: Fall 2019 |
|
-
AVM 225 - Fire, Ice, Rain, and Fuel Systems 2.5 Credits, 5 Contact Hours 1.25 lecture periods 3.75 lab periods
Theory and application of fire, ice, rain and fuel systems. Includes fire detection terms, extinguishing and protection systems, smoke detection, fire warning, fire extinguishing system components used, how systems function, inspection testing and maintenance, ice and rain protection terms, formation and conditions for icing of aircraft, ice and rain detection, protection systems components, functions, inspection and maintenance, fuel system terms, safety system requirements, fuel tank types and construction, indicating, fueling, and defueling inspection and maintenance.
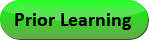.png)
Course Learning Outcomes
- Demonstrate proficient knowledge of aircraft fire detection and protection systems
- Demonstrate proficient knowledge of aircraft ice and rain protection systems
- Demonstrate proficient knowledge of aircraft fuel systems
- Demonstrate proficient knowledge of aircraft system maintenance practices
Outline:
- Fire Protection Terms
- Fuels
- Oxidizers
- Combustion
- Reactivity
- Detection
- Protection
- Extinguishing
- Zones
- Fixed
- Portable
- Detection
- Overheat
- Rate of temp rise
- Flame detectors
- Radiation sensing
- Smoke
- Carbon monoxide
- Combustible mixture
- Fiber optic
- Observation of crew or passengers
- Detection System Requirements
- Accurate warnings
- Location
- Testing
- Environmental
- Weight
- Power
- Indicating
- Common Fire and Overheat Detection Devices
- Thermal switch
- Spot detector
- Thermocouple
- Continuous loop
- Continuous element
- Fire Protection
- Firewalls
- Heat shielding
- Protective sleeving
- Interior material treatments
- Smoke Detection
- Carbon monoxide
- Photo electric
- Visual
- Extinguishing Agents
- Halogenated hydrocarbons
- Inert cold gas
- Extinguishing Systems
- Hand held
- High rate of discharge
- Maintenance
- Troubleshooting
- Ice and Rain
- Conditions
- Effects
- Types and terms
- Detection Methods
- Visual
- Performance
- Optical
- Electronic
- Prevention
- Avoidance
- Heating surfaces
- Chemical
- Mechanical
- Pneumatic Deicing
- Operation
- Components
- Maintenance
- Thermal (Combustion Heater)
- Operation
- Components
- Maintenance
- Thermal (Bleed Air)
- Operation
- Components
- Maintenance
- Thermal (Electrical Element)
- Operation
- Instrument sensing protection
- Windshield icing/defrost
- Drain heating
- Maintenance
- Rain Removal Systems
- Forced air
- Wiper
- Chemical
- Maintenance
- Fuel Systems Safety
- Safety
- System types
- Fuel compatibility
- System Types
- Fuel storage
- Tank
- Bladder
- Integral
- Gravity feed
- Transfer feed
- Fuel Pumps
- Vane
- Rotary piston
- Hand pumps
- Fuel Filters and Strainers
- Types
- Servicing and replacements
- Lines and fittings
- Fuel Valves
- Selector
- Check values
- Sump and drain
- Fuel Management
- Multiple tank, selection
- Fueling
- Transfer
- Jettison
- VXXII. Indicating
- Visual
- Placarding
- Resistance
- Capacitance
- Mechanical
- System Maintenance
- Securing
- Leakage
- Corrosion
Effective Term: Full Academic Year 2021/2022 |
|
-
AVM 226 - Engine Electrical Systems 3.5 Credits, 8 Contact Hours 1.25 lecture periods 6.75 lab periods
Inspection, repair, and modification of engine electrical systems. Includes magneto(s) (components, tooling, wiring, and drives), ignition switches, ignition harness, ignition booster system, spark plugs, engine ignition analyzers, turbine engine (ignition transformers and igniter plugs), engine electrical controls (switches, fuses and circuit breaker, circuits, wiring, installation, and engine bulkhead), and technical data manuals and catalogs.
Prerequisite(s): AVM 208
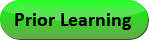.png)
Course Learning Outcomes
- Demonstrate proficient knowledge of reciprocating engine ignition systems
- Demonstrate proficient knowledge of turbine engine ignition systems
- Demonstrate proficient knowledge of engine electrical system wiring standards
- Demonstrate proficient knowledge of engine electrical system troubleshooting processes
Outline:
- Magnetos (Components)
- Rotor
- Magnets
- Bearings
- Pole shoe
- Housings
- Timing gears
- Coils
- Breaker points
- Distributor
- Magnetos (Tooling)
- Basic tools for disassembly
- Point gapping tools
- E-gap equipment
- Fixtures
- Timing equipment
- Condenser testers
- Magneto test bench
- Ohm meter ops
- Magnetos (Wiring)
- High tension
- Low tension
- Flexible shielding
- Non-flexible shielding
- Ignition contacts
- Magnetos (Drives)
- Impulse
- Operation
- Lag
- Inspection
- Direct drive spline
- Accessory drive attachments
- Ignition Switches
- Purpose
- Types
- Operation
- Installations
- Ignition Harness
- Descriptions
- Types
- Operations
- Installations
- Troubleshooting
- Repairs
- Ignition Booster System
- Description of operation
- Booster coil
- Induction vibrator
- Troubleshooting
- Spark Plugs
- Description of operation
- Types and designations
- Reach
- Electrodes
- Servicing
- Engine Ignition analyzers
- Description of operations
- Equipment types
- Usage
- Turbine Engine (Ignition Transformers)
- Description of operations
- Types and designations
- Hazards
- Components
- Mounting
- Troubleshooting and repair
- Turbine Engine (Igniter Plugs)
- Description of operation
- Types/designations
- Hazards
- Components
- Igniter leads
- Troubleshooting, servicing and repair
- Engine electrical controls (switches)
- Types
- Applications
- Troubleshooting and repair
- Installations
- Engine electrical controls (fuses, circuit breakers)
- Types
- Applications
- Troubleshooting and repair
- Installations
- Engine Electrical Controls (Circuits)
- Type
- Power supplies
- 14 volt
- 28 volt
- 115 volt AC
- Applications
- Troubleshooting and repair
- Engine Electrical Controls (wiring)
- Types
- Applications
- Sizing
- Selection
- Installation
- Securing
- Protective methods
- Typical installations
- Engine Electrical Controls (Installation)
- Electrical terminals
- Splicing
- Bonding jumpers
- Identification of cables
- Engine Electrical Controls (Engine Bulkhead)
- Connector plugs
- Mating receptacles
- Quick disconnect
- Securing and safe tying
- Technical Data
- Service manuals (SM)
- Part catalogues
- Maintenance manuals (MM)
- Wiring diagram manuals (WDM)
- Overhaul manuals (OM)
Effective Term: Full Academic Year 2021/22 |
|
-
AVM 227 - Engine Air Flow Systems 2.5 Credits, 5 Contact Hours 1.25 lecture periods 3.75 lab periods
Fundamentals of engine air flow systems. Includes reciprocating engine induction systems, alternate induction air systems, induction systems maintenance, superchargers, turbochargers, turbo compound systems, reciprocating engine exhaust systems, exhaust subsystems, exhaust system maintenance, reciprocating engine cooling, turbine engine induction systems, turbine engine cooling, turbine engine exhaust systems, turbine engine exhaust systems maintenance, and turbine engine airflow subsystems.
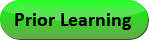.png)
Course Learning Outcomes
- Demonstrate proficient knowledge of reciprocating engine induction systems
- Demonstrate proficient knowledge of reciprocating engine exhaust systems
- Demonstrate proficient knowledge of engine ice, rain, and cooling systems
- Demonstrate proficient knowledge of turbine engine airflow systems
Outline:
- Reciprocating Engine Induction Systems
- Naturally aspirated
- Air scoop
- Air filters
- Ducting
- Manifolds
- Super charged
- Air scoop
- Filters
- Ducting
- Manifolds
- Alternate Induction Air Systems
- Air preheat
- Carburetor ice
- Induction air heat exchange
- Induction air icing
- Alternate air source
- Cabin heating
- Water separation
- Induction System Maintenance
- Inspections
- Repairs
- Servicing
- Superchargers
- Principles of operation
- Internally driven
- Externally driven
- Inspection and maintenance
- Turbochargers
- Principles of operation
- Components
- Intercoolers and heat exchanges
- Waste gate
- Controllers
- Fuel system requirements
- Lubrication
- Inspection and maintenance
- Turbo Compound Systems
- Principles of operation
- Components
- Applications
- Reciprocating Engine Exhausts Systems
- Principles of operation
- Materials
- Types
- Open systems
- Collector
- Effect on power production
- Exhaust Subsystems
- Ejectors
- Expansion joints
- Augmenters
- Heating source
- Mufflers
- Thermal anti ice
- Exhaust System Maintenance
- Hazards
- Crew and passengers
- Aircraft components
- Inspection
- Service and maintenance
- Repairs
- Reciprocating Engine Cooling
- System functions
- Principles of operation
- Cowlings
- Construction
- Installation and removal
- Baffling and seals
- Cylinder fin cooling
- Accessory cooling
- Exhaust component cooling
- Inspection and maintenance
- Turbine Engine Induction Systems
- Air inlets principles of operation
- Subsonic inlet ducts
- Supersonic inlet ducts
- Divergent type
- Convergent type
- Blow-in doors
- Turbine Engine Cooling
- Distribution of inlet air
- Fan and by-pass air
- Combustor air cooling
- Air mixers
- Turbine Engine Exhaust Systems
- Flow of gasses
- Collection of gasses
- Divergent passages
- Convergent ducts
- Inner cone
- Insulation of components
- Turbine Engine Exhaust Systems Maintenance
- Typical operational problems
- Inspection
- Service and maintenance
- Repair
- Turbine Engine Airflow Subsystems
- Cowl and glide vane anti-ice control
- Vortex destruction
- Thrust reverse
- Clamshell (external blocking)
- Cascade vane (internal blocking)
Effective Term: Full Academic Year 2021/2022 |
|
-
AVM 228 - Aircraft Propellers 2.5 Credits, 5 Contact Hours 1.25 lecture periods 3.75 lab periods
Basics of aircraft propellers. Includes propeller theory, nomenclature, types, construction, and installation and maintenance. Also includes constant speed systems, feathering systems, reversing systems, icing systems, synchronizing systems, and unducted fans.
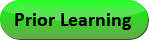.png)
Course Learning Outcomes
- Demonstrate proficient knowledge of aircraft propeller theory
- Demonstrate proficient knowledge of aircraft propeller operation
- Demonstrate proficient knowledge of aircraft propeller maintenance
- Demonstrate proficient knowledge of aircraft propeller systems
Outline:
- Propeller Theory
- Production of thrust
- Forces acting on propellers
- Centrifugal
- Torque bending force
- Thrust bending force
- Aerodynamic twisting force
- Centrifugal twisting force
- Propeller Nomenclature
- Leading edge
- Trailing edge
- Tip
- Shank
- Blade face
- Blade back
- Chord line
- Blade angle
- Axis of rotation
- Blade pitch and distribution
- Types of Propellers
- Fixed pitch
- Ground adjustable
- Two position
- Controllable pitch
- Identification
- McCauley
- Sensenich
- Constant speed
- Feathering
- Propeller Construction
- Wood propellers
- Aluminum propellers
- Steel propellers
- Composite propellers
- Propeller Installation and balancing
- Tapered shaft
- Flanged shaft
- Splined shaft
- Propeller safetying
- Propeller blade tracking
- Propeller balancing
- Propeller Maintenance
- Inspections and checks
- Service
- Repairs
- Lubricants and lubrication
- Propeller Federal Aviation Regulations (FARs)
- Propeller repair stations
- Constant Speed Systems
- Theory
- Types
- Instrumentation
- Controls
- Governors
- System operation
- Installation and removal
- Inspections and checks
- Troubleshooting
- Service and repairs
- Feathering Systems
- Theory
- Types
- Controls
- System operation
- Instrumentation
- Accumulator
- Governors
- Installations
- Inspections and checks
- Troubleshooting
- Service and repair
- Reversing Systems
- Theory
- Types
- Controls
- System operation
- Instrumentation
- Precautions
- Installations
- Inspections and checks
- Troubleshooting
- Service and repair
- Propeller Icing Systems
- Theory
- Types
- Controls
- System operation
- Installations
- Inspections and checks
- Troubleshooting
- Service and repair
- Propeller Synchronizing Systems
- Theory
- Types
- Instruments
- Controls
- Special sub systems
- System operations
- Installation removal
- Inspections and checks
- Troubleshooting
- Service and repair
- Unducted Fans
- Theory
- Types
- System operations
- Systems components
- Installations
- Inspections and checks
- Troubleshooting
- Service and repairs
Effective Term: Full Academic Year 2021/2022 |
|
-
AVM 229 - Engine Support Systems 2.5 Credits, 5 Contact Hours 1.25 lecture periods 3.75 lab periods
Theory and application of support systems for gas turbine engines. Includes fire protection, fire detection systems, fire extinguishing agents and systems, and fire detection and extinguishing system maintenance. Also includes turbine engine pneumatic systems, pneumatic starting systems, thrust reversers, auxiliary power units, turbine engine removal and installation, and engine storage and transport.
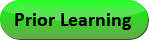.png)
Course Learning Outcomes
- Demonstrate proficient knowledge of engine fire protection systems
- Demonstrate proficient knowledge of engine pneumatic systems
- Demonstrate proficient knowledge of auxiliary power units
- Demonstrate proficient knowledge of engine removal and installation procedures
Outline:
- Fire Protection
- Requirements
- Fire detection
- Fire extinguishing
- Fire zones
- Fire Detection Systems
- Thermal switch
- Thermocouple
- Continuous loop
- Spot detector
- Rate of temperature rise
- Radiation sensing
- Smoke detection
- Overheat detectors
- Carbon monoxide detectors
- Combustible mixture
- Fiber optic detector
- Observations by crew
- Fire Extinguishing Agents
- Carbon dioxide
- Halogenated hydrocarbons
- Health and environmental precautions
- Fire Protection Systems
- Single point extinguishers
- Multiple point extinguishers
- High rate discharge systems
- Fire Detection and Extinguishing System Maintenance
- Inspections and checks
- Troubleshooting
- Servicing
- Repairs
- Turbine Engine Pneumatic Systems
- Bleed air sources
- Air to air heat exchangers
- Controls and monitoring
- Valves, lines and fittings
- Inspections/checks and servicing
- Pneumatic Starting Systems
- Starters
- Controls and operation
- Installations
- Maintenance
- Troubleshooting and repair
- Auxiliary Power Units
- Theory of operation
- Installations
- Controls and operations
- Starting system
- Fuel control system
- Speed sensing
- Power production
- Induction and exhausts
- Engine components
- Fire protection
- Inspection and checks
- Servicing
- Troubleshooting and repairs
- Thrust Reversers
- Operation and controls
- Installations
- Types
- Internal blockage
- External blockage
- Deflector valves
- System components
- Inspection/checks
- Service and repairs
- Troubleshooting
- Turbine Engine Removal
- Specialty equipment
- Hoists
- Transport dollies
- Engine mounts
- Attaching hardware
- Electrical disconnects
- Control disconnects
- Fuel lines attachments
- Pneumatic lines attachments
- Check list usage
- Turbine Engine Installation
- Pre-installation checks
- Mounting and attachment
- System connections
- Rigging of controls
- Inspections and checks
- Engine Storage and Transport
- Preserving processes
- Securing for shipping
- Shipping equipment
Effective Term: Full Academic Year 2021/2022 |
|
-
AVM 231 - Engine Principles, Monitoring and Inspection 3.5 Credits, 8 Contact Hours 1.25 lecture periods 6.75 lab periods
Principles, monitoring, and inspection of engines. Includes theory and construction of powerplants, requirements, types of engines, reciprocating engine design and construction, radial engine design and construction, reciprocating engine operating principles, engine power and efficiencies, turbine engine construction, turbine engine sub-assemblies, turbo prop engines, turbine engine operation principles, engine instrumentation, instrument principles of operation, maintenance of instruments and systems, and engine inspection requirements.
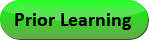.png)
Course Learning Outcomes
- Demonstrate proficient knowledge of reciprocating engine theory
- Demonstrate proficient knowledge of turbine engine theory
- Demonstrate proficient knowledge of engine instrumentation
- Demonstrate proficient knowledge of engine inspection procedures
Outline:
- Theory and Construction of Powerplants: Types and Terms
- Reciprocating
- Turbo jet
- Turbo props
- Fan Jet
- Pulse jet
- Ram jet
- Rocket
- Requirements
- Power and weight
- Fuel economy
- Durability and reliability
- Operating flexibility
- Compactness
- Power plant selection
- Types of Engines
- Inline engines
- Opposed, O type engines
- V-type engines
- Radial engines
- Reciprocating Engine Design and Construction
- Basic reciprocating part
- Crank case sections
- Crank shafts
- Connecting rods
- Pistons and pins, rings
- Cylinders and valve train
- Bearings
- Accessory case
- Numbering of cylinders
- Firing order
- Radial Engine Design and Construction
- Nose section
- Power section
- Diffuser section
- Accessory section
- Numbering of cylinders
- Firing order
- Reciprocating Engine Operating Principles
- Otto cycle
- Two stroke cycle
- Four stroke cycle
- Engine Power and Efficiencies
- Work
- Horsepower
- Piston displacement
- Compression ratio
- Indicated horsepower
- Brake horsepower
- Friction horsepower
- Thrust horsepower
- Thermal efficiency
- Mechanical efficiency
- Volumetric efficiency
- Propulsive efficiency
- Turbine Engine Construction
- Air inlet
- Compressor section
- Centrifugal flow
- Axial flow
- Diffuser section
- Combustion
- Annular
- Can
- Can-annular
- Turbine section
- Exhaust section
- Accessory section
- Turbine Engine Sub-Assemblies
- Single spools
- Split spools and exhaust systems
- Cowlings
- Turbo fans
- Turbo Prop Engines
- Power section
- Gear section
- Torque section
- Accessory section
- Turbine Engine Operation Principles
- Thrust
- Force
- Mass
- Acceleration
- Newton Laws
- Brayton pressure cycle
- Thermal efficiency
- Engine Instrumentation
- Carburetor air temperature gage
- Fuel pressure
- Fuel flowmeter
- Manifold pressure
- Oil temperature
- Oil pressure
- Tachometer
- Cylinder head temperature
- Torque meter
- Suction
- Range markings
- Red
- Yellow
- Blue
- Green
- White
- Instrument Principles of Operation
- Mechanical temperature indicators
- Electrical temperature indicators
- Mechanical pressure indicators
- Electrical pressure indicators
- Mechanical RPM indicators
- Electrical RPM indicators
- Mechanical fluid rate of low indicators
- Electrical fluid rate of flow indicators
- Maintenance of Instruments and Systems
- Performing maintenance on instruments
- Servicing of instruments
- Inspection, check of instruments
- Troubleshooting instrument systems
- Repairs of instrument systems
- Engine Inspection Requirements
- Inspection regulations
- FAR Part 21
- FAR Part 33
- FAR Part 39
- FAR Part 43
- FAR Part 91
- Manufacturers inspection instructions
- Maintenance manual
- Service manual
- Service bulletins
Effective Term: Full Academic Year 2021/22 |
|
-
AVM 232 - Reciprocating Engine Overhaul 3.5 Credits, 8 Contact Hours 1.25 lecture periods 6.75 lab periods
Basic aircraft reciprocating engine overhaul. Includes engine components, wrist pins, connection rods, crankshafts, case, cam shafts, lifters, valves, push rods and tubes, rocker assemblies, accessories, lubrication, overhaul options overhaul credentials, overhaul procedures, reassembly after overhaul, engine installations, engine break-in, and test cell procedures.
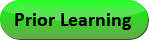.png)
Course Learning Outcomes
- Demonstrate proficient knowledge of common reciprocating engine nomenclature
- Demonstrate proficient knowledge of reciprocating engine overhaul procedures
- Demonstrate proficient knowledge of reciprocating engine overhaul processes
- Demonstrate proficient knowledge of reciprocating engine operation
Outline:
- Engine Components: Cylinders and Heads
- Barrels
- Skirts
- Fins
- Materials
- Taper
- Mounting holes
- Pistons
- Materials
- Shapes
- Ring groves
- Ring types
- Cam ground
- Wrist Pins
- Materials
- Caps and retainers
- Connection Rods
- Materials
- Bushing and bearings
- Lubrication
- Crankshafts
- Materials
- Manufacturing process
- Rod and bearing journals
- Throws
- Counter weights
- Flange and spline prop shafts
- Case
- Materials
- Construction
- Stud and bolts
- Alignment
- Lubrication
- Data plates
- Assembly concerns
- Cam Shafts
- Materials
- Manufacturing process
- Bearing journals
- Cam lobes
- Lifters
- Solid
- Hydraulic
- Lubrication
- Valves
- Types
- Materials
- Nomenclature
- Grinding
- Lapping
- Seats
- Guides
- Push Rods and Tubes
- Types
- Materials
- Lubrication
- Rocker Assemblies
- Types
- Materials
- Lubrication
- Accessories
- Gears
- Case
- Mounting pads
- Lubrication
- Principles
- Lubricants
- Oil pumps
- Filters
- Sumps
- Oil supplies
- Overhaul Options
- Complete
- Top overhaul
- Remanufacture
- Factory service instructions
- When to overhaul
- Overhaul Credentials
- Who is authorized
- A&P
- A&P – I/A
- Factory
- Repair station
- Overhaul Procedures
- Initial inspections
- Disassembly
- Cleaning
- Dimensional inspections/table of limits
- NDI inspections
- Magnetic particles
- Dye penetrate
- Eddy current
- X-ray
- Manuals
- Service instructions
- Individual component maintenance
- Crankshaft and camshaft run out
- Valve and cylinder grinding
- Spring, rod, lifter, and rocker inspection and service
- Reassembly After Overhaul
- Layout of components
- Tooling and equipment
- Torque
- Pre-lubrication
- Paperwork
- Engine Installations
- Motor mount
- Accessories
- Magnetos, plugs, and harnesses
- Starter
- Fuel systems
- Electrical
- Propeller
- Baffling
- Engine Break-In
- Procedures
- Cooling
- Monitoring
- Instrumentation
- Run cells
- Aircraft installations
- Test Cell Procedures
- Minimum crew
- Equipment limitations
- Safety concerns
Effective Term: Full Academic Year 2021/22 |
|
-
AVM 233 - Turbine Engines 4 Credits, 8 Contact Hours 2 lecture periods 6 lab periods
Basic gas turbine engine and turbo propeller component makeup and repair. Includes inspection, servicing, and repairs performed on engine components: compressor, diffuser, combustion, accessory drive, and lubricating system. Also includes a reassembly overhaul.
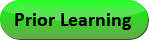.png)
Course Learning Outcomes
- Demonstrate proficient knowledge of common turbine engine nomenclature
- Demonstrate proficient knowledge of turbine engine overhaul procedures
- Demonstrate proficient knowledge of turbine engine overhaul processes
- Demonstrate proficient knowledge of turbine engine lubrication systems
Outline:
- Engine Components: Compressor
- Principles of operation
- Pressure
- Velocity
- Compression ratio
- Surges
- Tall
- Bleed air
- Construction
- Materials
- Manufacturing processes
- Assembly
- Type Specifics
- Centrifugal flow
- Axial flow
- Reverse flow
- Stages
- Split spools
- Fans
- Hybrids
- Engine Components: Compressor
- Principles of operation
- Pressure
- Velocity
- Compression ratio
- Surges
- Tall
- Bleed air
- Construction
- Materials
- Manufacturing processes
- Assembly
- Type Specifics
- Centrifugal flow
- Axial flow
- Reverse flow
- Stages
- Split spools
- Fans
- Hybrids
- Vanes
- Guide vane
- Stator vane
- Rotor vane
- Fan blades
- Attachment
- Inspection
- Service and maintenance
- Repair
- Overhaul
- Engine Components: Diffuser
- Principles of operation
- Pressure
- Velocity
- Routing
- Mixing
- Construction
- Materials
- Manufacturing processes
- Type specifics
- Centrifugal
- Axial flow
- Fuel routing
- Mixture control
- Attachment
- Maintenance
- Inspection
- Servicing
- Repairs
- Overhaul
- Engine Components: Combustion
- Principles of operation
- Fuel air mixing
- Distribution to burners
- Cooling
- Pressure of gasses
- Construction
- Materials
- Manufacturing processes
- Assembly
- Type specifics
- Can
- Can-annular
- Annular
- Reverse-flow combustors
- Stages
- Hybrids
- Turbine blades
- Inlet guide vanes
- Reaction turbine blade
- Impulse blade
- Turbine stators
- Blade shrouding
- Blade tip clearance
- Blade cooling
- Attachment
- Blade failures
- Maintenance
- Inspection
- Servicing
- Repairs
- Overhaul
- Engine Components: Accessory Drives
- Purpose
- Drive pads
- Oil pump
- Fuel pump
- Hydraulic pump
- Electrical generation
- Starter
- Monitoring
- Construction
- Type specifics
- Power inputs
- Engine Components: Lubricating System
- Lubricants
- Friction
- Heat
- Corrosion
- Contaminants
- Types
- Grades
- Additives
- Lubricant Systems
- Wet sump
- Dry sump
- Hot tank
- Cold tank
- Pressure
- Scavenge
- Vents
- Tanks
- Construction
- Purpose
- Air oil separation
- Pressurization
- Bearings and seals
- Materials
- Loads
- Alignment
- Vibration
- Ball type
- Roller type
- Split type
- Lubrication
- Seals
- Carbon
- Labyrinth
- Oil Pumps
- Gerotor type
- Vain type
- Spur-gear
- Pressure relief valves
- Filters
- Disc type
- Element
- S
- By-pass system
- Servicing
- Oil coolers
- Purpose
- Types
- Oil to air types
- Oil to fuel types
- By-pass systems
- Maintenance
- Monitoring
- Pressure
- Temperature
- Quantity
- Filter by-pass
- Chip detection
- Oil analysis
- Inspection
- Servicing
- Repairs
- Overhaul
- Engine Components: Propeller Reduction Gear Systems
- Principles
- Transition of power
- Torque
- Assembly
- Construction
- Materials
- Manufacturing processes
- Assembly
- Type specifics
- Allison
- Garrett
- Pratt and Whitney
- General Electric
- Reduction Gearing
- Maintenance
- Inspection
- Servicing
- Repairs
- Overhaul
- Turbine Engine Overhaul
- Overhaul options
- Complete
- Partial selection
- Compressor
- Turbine
- Reduction gear
- Factory service instructions
- When to overhaul
- Authorization to perform maintenance
- Airframe and powerplant
- Factor
- Repair stations
- Inspection
- Overhaul procedures
- Initial inspection
- Disassembly
- Cleaning
- Dimensional inspections
- N.D.I. inspections
- Magnetic particle
- Eddy current
- X-ray
- Ultra sound
- Dye-penetrate
- Visual
- Manuals
- Service instructions
- Reassembly after overhaul
- Layout of components
- Tooling and equipment
- Torque
- Pre-treatments
- Paperwork
- Final inspection
Effective Term: Full Academic Year 2021/2022 |
|
-
AVM 234 - Engine Fuel Metering and Operation 4 Credits, 8 Contact Hours 2 lecture periods 6 lab periods
Fundamentals of aircraft fuel systems. Includes fuel metering theory and requirements, aviation fuels, float type carburetion, float carburetor maintenance and installation, and pressure carburetor maintenance and installation. Also includes fuel injection systems, Bendix fuel injection and maintenance, and Teledyne Continental Motors (TCM) fuel injection and maintenance. Also includes fuel metering system components and maintenance, turbine engine fuel systems components and maintenance, jet fuel controls; and reciprocating, turbine, and turbo propeller engine operations.
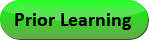.png)
Course Learning Outcomes
- Demonstrate proficient knowledge of engine fuel metering systems
- Demonstrate proficient knowledge of aircraft carburetors
- Demonstrate proficient knowledge of engine fuel metering system maintenance
- Demonstrate proficient knowledge of engine operation
Outline:
- Fuel Metering Theory
- Energy transformation
- Fuel air mixtures
- Efficiencies
- Power production
- Aviation Fuels
- Automotive gasoline
- Aviation gasoline
- Aviation turbine engine fuels
- Fuel ratings and grades
- Fuel additives
- Fuel contamination
- Fuel handling
- Fuel Metering Requirements
- Basic operations
- Operating environments
- Float Carburetors
- Float Type Carburetion
- Main metering system
- Mixture control
- Idle metering
- Idle mixture
- Acceleration system
- Power enrichment
- Float Carburetor Maintenance
- Destinations
- Data plates
- Inspection and checks
- Servicing
- Overhaul
- Float Carburetor Installations
- Mounting
- Adjustments
- Troubleshooting
- Supply lines
- Adjustments
- Pressure Carburetors
- Pressure Carburetor Components
- Fuel and air metering forces
- Mixture control
- Idle systems
- Acceleration systems
- Power enrichment
- Pressure Carburetor Maintenance
- Designations
- Inspection and checks
- Servicing
- Overhaul
- Adjustments
- Pressure Carburetor Installations
- Mounting
- Adjustments
- Troubleshooting
- Supply fuel lines
- Fuel pumps
- Fuel Injection Systems
- Principles of operation
- System components
- Fuel plumbing
- Fuel pumps
- Fuel Injection (Bendix)
- Components
- Metering forces
- Fuel flow
- Idle system
- Power enrichment
- Injectors
- Mixture control
- Fuel Injection Maintenance (Bendix)
- Inspection and checks
- Servicing
- Troubleshooting
- Repairs
- Adjustments
- Overhaul
- Fuel Injection (TCM)
- Components
- Fuel control unit
- Injection pump
- Fuel manifold
- Supply and return lines
- Injector nozzles
- Fuel Injection Maintenance (TCM)
- Inspection and checks
- Servicing
- Troubleshooting
- Adjustments
- Repairs
- Overhaul
- Fuel Metering Systems
- Fuel Metering System Components
- Lines and fittings
- Hoses and clamps
- Fuel pumps
- Mounting (installation)
- Fuel Metering System Components Maintenance
- Inspection and checks
- Servicing and repair
- Troubleshooting
- Adjustment and tests
- Reciprocating Engine Operations
- Terms and definitions
- Controls
- Engine monitoring instruments
- Performance charts
- Emergency procedures
- Operational checks
- Turbine Engine Fuel System Basics
- Requirements
- Jet fuel metering basics
- Turbine engine pressure and temperature sensing
- Engine start sequence
- Engine run parameters
- Engine shut down sequence
- Turbine Fuel System Components
- Main fuel pumps
- Constant displacement
- Variable displacement
- Fuel heaters
- Fuel filters
- Fuel spray nozzles
- Fuel manifolds
- Simplex
- Duplex
- Flow divider
- Fuel pressurizing and dump values
- Turbine Engine Jet Fuel Controls
- Principles of operation
- Venturi and regulator valves
- Metering value
- Speed sensing
- Fuel drain valve
- Pressure regulating valve
- Throttle valve
- Surge and temperature valve
- Translating cam
- Speed protection
- Turbine Engine Fuel System Maintenance
- Inspection and checks
- Servicing
- Adjustment and test
- Troubleshooting
- Repairs
- Turbine Engine Operations
- Terms and definitions
- Controls
- Engine monitoring instruments
- Performance charts
- Emergency procedures
- Operational checks
- Turbo Propeller Operations
- Terms and definitions
- Controls
- Engine monitoring instruments
- Performance charts
- Emergency procedures
- Operational checks
Effective Term: Full Academic Year 2021/2022 |
|
-
AVM 260 - Aircraft Composite Repair II 1 Credits, 1 Contact Hours 1 lecture period 0 lab periods
Theory and application of composite and bonded metal structures utilized in aircraft construction. Includes repair methods selection, source documents, repair methods and design criteria, bonded metal repairs, tank and non-tank processing, priming, and environmental considerations. Also includes a heavy emphasis on repair performance utilizing the Structural Repair Manuals for composite monolithic and sandwich core, and bonded metal structures.
Prerequisite(s): AVM 130 Corequisite(s): AVM 260LB
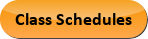
Course Learning Outcomes
- Demonstrate Structural Repair Manual selection by determining Component identification and damage classification.
- Describe the function and use of source documents provided by aircraft manufacturers.
- Explain the history and purpose of bonded metal repairs.
- Describe tank processing of bonded metal repairs.
- Describe environmental considerations in the handling of composite and metal bonded materials.
Outline:
- Structural Repair Manual Repair Method Selection
- Component identification
- Damage classification
- Source Documents
- Revision systems
- Effectivity
- Drawing systems
- Internal documents
- Material and process specifications
- Original equipment manufacturer documents
- Regulatory documents
- Bonded Metal Repairs (General)
- History
- Purpose
- Theory
- Safety
- Tank Processing
- Forest Products Laboratories (FPL)
- Phosphoric Acid Anodizing (PAA)
- Environmental Considerations
- Environmental Protection Agency
- Handling
- Disposal
Effective Term: Full Academic Year 2018/19 |
|
-
AVM 260IN - Advanced Composite Aircraft Repair II 4 Credits, 10 Contact Hours 1 Lecture Period 9 Lab Periods
Theory and application of composite and bonded metal structures utilized in aircraft construction. Includes repair methods selection, source documents, repair methods and design criteria, bonded metal repairs, tank and non-tank processing, priming, and environmental considerations. Also includes a heavy emphasis on repair performance utilizing the Structural Repair Manuals for composite monolithic and sandwich core, and bonded metal structures.
Prerequisite(s): AVM 130 Information: IN is the integrated version of the course with the lecture and lab taught simultaneously.
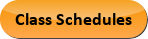
Course Learning Outcomes
- Demonstrate Structural Repair Manual selection by determining Component identification and damage classification.
- Describe the function and use of source documents provided by aircraft manufacturers.
- Demonstrate repair methods including speed tape, resin sealing, potting, bolted doublers, wet layup at room temperature and elevated temperature, prepreg hot bonding, and edge and corner damage.
- Explain the history and purpose of bonded metal repairs.
- Demonstrate metal priming in preparation for metal bonding repair.
- Describe tank processing of bonded metal repairs.
- Differentiate non-tank processing of bonded metal repairs.
- Describe environmental considerations in the handling of composite and metal bonded materials.
Outline:
- Structural Repair Manual Repair Method Selection
- Component identification
- Damage classification
- Repair Methods
- Speed tape
- Resin sealing
- Potted repairs
- Bolted and bonded doubler
- Pre-cure
- Wet layup (room temperature)
- Wet layup (elevated temperature)
- Prepreg
- Serrated rivet
- Glass repair of aluminum
- Source Documents
- Revision systems
- Effectivity
- Drawing systems
- Internal documents
- Material and process specifications
- Original equipment manufacturer documents
- Regulatory documents
- Structural Repair Manual General Repairs and Design Criteria (Chapter 51)
- Damage removal
- Line repairs
- Pre-cure versus co-cure
- Surface preparation
- Ply orientation
- Taper repairs
- Step repairs
- Wet lay up techniques
- Prepreg techniques
- Sandwich structure repair
- Combination monolithic/sandwich repair
- Corner repairs
- Blind repairs
- Bonded Metal Repairs (General)
- History
- Purpose
- Theory
- Safety
- Tank Processing
- Forest Products Laboratories (FPL )
- Phosphoric Acid Anodizing (PAA )
- Non-Tank Processing
- Phosphoric Acid Non-Tank Anodizing (PANTA )
- Pasa-gel
- Hydrofluoric acid
- Abrasion
- Priming
- Purpose
- Types
- Safety
- Application
- Curing and drying
- Environmental Considerations
- Environmental Protection Agency
- Handling
- Disposal
Effective Term: Full Academic Year 2021/22 |
|
-
AVM 260LB - Aircraft Composite Repair II Lab 3 Credits, 9 Contact Hours 0 lecture periods 9 lab periods
This is the Lab portion of AVM 260 .
Prerequisite(s): AVM 130 Corequisite(s): AVM 260
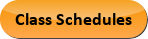
Course Learning Outcomes
- Demonstrate repair methods including speed tape, resin sealing, potting, bolted doublers, wet layup at room temperature and elevated temperature, and prepreg hot bonding.
- Demonstrate step and taper repairs to wet layup and prepreg materials including edge and corner damage.
- Demonstrate step and taper repairs to wet layup and prepreg materials including edge and corner damage.
- Differentiate non-tank processing of bonded metal repairs.
- Demonstrate hydrofluoric acid metal etching.
- Demonstrate metal priming in preparation for metal bonding repair.
Outline:
- Repair Methods
- Speed tape
- Resin sealing
- Potted repairs
- Bolted and bonded doubler
- Pre-cure
- Wet layup (room temperature)
- Wet layup (elevated temperature)
- Prepreg
- Serrated rivet
- Glass repair of aluminum
- Structural Repair Manual General Repairs and Design Criteria (Chapter 51)
- Damage removal
- Line repairs
- Pre-cure versus co-cure
- Surface preparation
- Ply orientation
- Taper repairs
- Step repairs
- Wet lay up techniques
- Prepreg techniques
- Sandwich structure repair
- Combination monolithic/sandwich repair
- Corner repairs
- Blind repairs
- Non-Tank Processing
- Phosphoric Acid Non-Tank Anodizing (PANTA )
- Pasa-gel
- Hydrofluoric acid
- Abrasion
- Priming
- Purpose
- Types
- Safety
- Application
- Curing and drying
Effective Term: Full Academic Year 2018/19 |
|
|
|