|
2021-2022 College Catalog [ARCHIVED CATALOG]
Course Descriptions
|
|
Legend for Courses
HC/HN: Honors Course IN/IH: Integrated lecture/lab LB: Lab LC: Clinical Lab LS: Skills Lab WK: Co-op Work
SUN#: is a prefix and number assigned to certain courses that represent course equivalency at all Arizona community colleges and the three public universities. Learn more at www.aztransfer.com/sun.
|
|
Automated Industrial Technology |
|
-
AIT 100 - Industrial Safety 1 Credits, 1 Contact Hours 1 lecture period 0 lab periods
Application of all safety, health and environmental requirements associated with all of the NIMS duty areas.
Information: BCT 110 may be substituted for AIT 100.
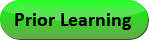.png)
Course Learning Outcomes
- Adhere to all of the safety, health, and environmental rules and regulations.
- Demonstrate ethical behavior and industry professional standards.
- Practice effective oral and written communication.
- Achieve common goals through effective collaboration.
Outline:
- Roles and Responsibilities for Safety, Health, and Environment
- OSHA, NIOSH, EPA, and other Federal and State Safety Requirements for the Workplace
- Common Industrial Hazards per OSHA Standards
- Ergonomics
- Laser safety
- NFPA arc flash
- Confined space
- Lockout/Tagout (LOTO) Program
- LOTO process
- Test to ensure a zero energy state
- Selecting Appropriate Personal Protective Equipment per Job
- Locate a Safety Data Sheet (SDS), Interpret the Information
- Proper Fall Protection for:
- Working at heights
- Sing ladders, scaffolding, and lifts
- Hazardous Situations (i.e. apply proper procedures to the situation)
- Process to Perform a Job Safety Analysis
- Principles of the 6S Program
- Sort
- Sweep
- Sanitize
- Set-to-order
- Sustain
- Safety
- Fuel Source and Selection of Correct Fire Extinguisher Class
- Machine Guarding for Mechanical Power Transmission Systems Purpose
- Required Machine Guarding for Mechanical Power Transmission Systems
- Safely Store and Dispose of:
- Lubricants
- Maintenance chemicals
- Required Machine Guarding for Fluid Power Systems
- Safe Procedures for Removing:
- Stored hydraulic or pneumatic energy
- Systems with accumulators and compressed air reservoirs
- Dangers of Personal Contact with:
- Pressurized hydraulic
- Pneumatic streams
- Procedures to Avoid Oil Fire Hazards
- Guidelines to Avoid Contact with Hot Surfaces in Fluid Power Systems
- NEC Safety Regulations
- Safety Procedures for:
- Tightening electrical conductors and components
- Disconnecting electrical conductors and components
- Connecting electrical conductors and components
- Hazards and Avoiding Personal Contact with Live Electrical Systems
- Guidelines on the Safe Approach Distances While Working on Electrical Systems
- Safety Procedures for:
- Disconnecting electronic components
- Connecting electronic components
- Hazards and Precautionary Safety Procedures for Working with Electronic Systems
- Standards to Adhere to Grounding Safety Procedures
- NFPA 70E Arc Flash Guidelines (i.e. their Importance)
- Safety Procedures for:
- Disconnecting process control components
- Connecting process control components
- Hazards and Precautionary Safety Procedures for Working with Process Control Systems
- Environmental Rules and Regulations (i.e. Could be impacted while Working with Process Control Systems)
Effective Term: Full Academic Year 2019/20 |
|
-
AIT 105 - Maintenance Operations 3 Credits, 5 Contact Hours 2 lecture periods 3 lab periods
Overview of the area of maintenance operations of a manufacturing facility. Preparation to sit for the NIMS Duty Area 1: Maintenance Operations Certification Exam.
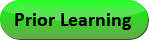.png)
Course Learning Outcomes
- Perform machine operation including startup, emergency, and normal shutdown and manual functions.
- Monitor machine operation and verify that performance meets safety, production, and maintenance requirements.
- Locate, interpret, and store machine operation and maintenance documentation.
- Perform planned and unscheduled machine maintenance procedures in accordance with a company-approved maintenance plan.
- Perform a preventative maintenance procedure for a given machine to extend machine life and minimize downtime.
Outline:
- Machine Operation (i.e. startup, emergency/normal shutdown, manual functions) To Effectively and Safely Meet Production and Maintenance Requirements
- Safety checklist:
- Ready/come online
- Correct operation of safety devices
- Check operation of machine interlocks
- Machine malfunction definition
- Standard operating procedures definition
- Operations to start and stop an operation
- When a machine needs to be shut down
- Lockout process (perform process)
- Monitoring Machine Operation; Verifying Performance Meets Production Requirements
- Confirming (with operator) machine is operating within specifications
- Five senses to observe machine operation and vibration (i.e. determine machine operating correctly, recognize malfunctions symptoms)
- Operator use of correct operation procedure evaluation
- Leaks, dirt, and loose connections
- Read:
- Pressure gauges
- Flow meters
- Fluid levels
- Temperature gauges
- Voltages and current
- HMI (monitor machine)
- Machine reading comparisons (i.e. machine documentation and performance specifications to determine if machine is performing within specifications)
- Record machine operation history (manual log or computer database)
- Locate, Interpret, and Store Machine Operation and Maintenance Documentation
- Methods of storing machine operation and maintenance documentation (accessible to the maintenance technicians and operators)
- Locate and interpret (for a given machine):
- Machine operation manuals, including: identification of safety requirements and features, performance specifications, stand operating procedures, startup/shutdown procedures
- Spare parts lists, vendor sources, and maintenance procedures
- Machine operation history logs, computer-based and manual
- Machine operating history from an HMI database
- Machine lubrication and preventive maintenance schedules from company or machine manufacturer documentation
- Planned and Unscheduled Machine Maintenance Procedures (In Accordance with a Company-Approved Maintenance Plan)
- Concept of total productive maintenance (TPM) definition (e.g. combination of preventive, predictive, and total company buy-in)
- Benefits and limitations of preventive/predictive maintenance
- Company procedures to inform production personnel of maintenance to be done on a machine
- Use of CMMS description
- When a work order is needed
- Steps to perform an unscheduled/planned maintenance procedure
- Concept of autonomous maintenance
- Elements of a comprehensive maintenance plan
- Methods of eliminating unplanned maintenance events
- Types of planned/unplanned maintenance procedures
- How to read, interpret, and resolve a work order
- Preventative Maintenance Procedure(s) for a Given Machine to Extend Machine Life and Minimize Downtime
- Describe preventive maintenance procedure given machine documentation
- Types of preventive maintenance tasks
- Identify and remove sources of contamination (e.g. select best methods of cleaning machine based upon continuous improvement principle)
- Predictive Maintenance on a Given Machine to Extend Machine Life and Minimize Downtime
- Basic elements and benefits of a predictive maintenance plan
- Types of predictive maintenance methods and their applications using basic senses (hearing, feeling, etc.) and their techniques:
- Vibration analysis
- Thermography
- Oil analysis
- Acoustic analysis
- Motor current analysis.
- Performing predictive maintenance
- Reading/Interpreting Technical Drawings of Parts and Assemblies with Tolerances and Basic GD&T
- Reading/interpreting technical drawings (of parts/assemblies with tolerances, basic GD&T)
- Line types and basic symbology
- Multi-view drawings of cylindrical and prismatic shaped parts
- Metric and English dimension conversions
- Dimension lines for linear, circular, and angular dimensions
- Title blocks
- Feature sizes using a drawing scale
- GD&T feature control frames
- Standard dimensional tolerance
- GD&T tolerances for form orientation, location
- Assembly drawings
- Assembly tolerances, interference fit concept
- Maximum material condition symbols
- Sectional cutaway views
- Threaded and non-threaded fastener specifications
- Type of fastener (given a sample)
- Fastener selection (for a given application)
- Sizes and types of washers, pins, nuts, locking devices
- Hand Tools to Inspect, Adjust/Tighten, and Assemble/Disassemble Equipment to Support Preventive Maintenance, Inspection, and Troubleshooting Activities
- Basic hand tool safety rules and application for use as defined by OSHA standards
- Concepts of how a fastener works, force, torque, dynamic and static torques, press fits, assembly tolerances
- Proper fastener selection
- Select and (proper) use of:
- Screw and nut drivers
- Fixed wrenches
- Allen/hex key wrenches
- Ratchet wrenches
- Click-type torque wrench
- Pliers, clamps, and mallets.
- Pneumatic powered torque wrenches
- Electric powered hand tools (e.g. drills, torque wrenches, and screwdrivers)
- Methods to protect parts and components during handling and storage
- Assembling parts using:
- Threaded fasteners, washers, and nuts
- Pins, keys, clips, snap rings, and tie wraps
- Tightening parts using correct bolt pattern sequence
- Hoists and Other Tools to Safely Handle and Move Parts and Equipment
- Rigging safety including load capacity (description and demonstration)
- Hoist inspection, determining if safe to use
- Manual and powered hoists (using cantilevered and gantry configurations)
- Calculating center of gravity for load balance
- Proper use of eyebolts for lifting parts
- Basic rigging techniques; types of slings, come-a-longs, blocking, chaining to lift a load
- Basic concepts of force, center of gravity, force vectors, rated load, and crush force
- Manual pry bar and truck to move a load
- Hydraulic jack to lift a load
- Dolly to move a load
- Proper containment methods to store a component
- Handling parts using proper containment prevention methods
- Components inspection (for contamination; to take corrective action)
- Troubleshooting Methodologies to Find Malfunctions in Machine Systems (to Return the System to Reliable, Productive Use in the Shortest Time Possible)
- Methodologies to isolate problems to a particular sub-system, 5-why, fishbone, flow charts, half-split method, etc.
- Effective interpersonal skills to interact with production personnel, vendors, and colleagues
- Effective observation and interview strategies to validate the problem and determine the most effective troubleshooting strategy
- Analyzing production information, maintenance, and operation documents to assist in troubleshooting a malfunction
Effective Term: Full Academic Year 2020/21 |
|
-
AIT 110 - Mechanical Systems 3 Credits, 5 Contact Hours 2 lecture periods 3 lab periods
Overview of the area of basic mechanical systems of a manufacturing facility. Preparation to sit for the NIMS Duty Area 2: Basic Mechanical Systems Certification Exam.
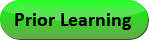.png)
Course Learning Outcomes
- Use measurement hand tools to inspect dimensions of shafts and other components.
- Install, align, tension, and adjust: a shaft couplings, belt drives, chain drives, gear drives, pillow block, and flange block bearing.
- Identify all lubrication points on a machine, select lubricant, and apply lubricant to machine according to maintenance schedule.
- Apply troubleshooting techniques for shaft couplings, chain drives and belt drives.
- Utilize effective mechanical fabrication procedures.
Outline:
- Measurement Tools (i.e. inspect dimensions of shafts and components)
- Metric, decimal, inch fraction rules
- Conversions of measurements
- English units
- Metric units
- Calipers
- Digital
- Dial
- Micrometers
- Digital
- Vernier
- Resolution, repeatability, and accuracy
- Tool selection (based on accuracy and feature to be measured)
- Measurement concepts
- Check calibration of measurement tool using a master
- Dial indicator or digital indicator to measure:
- Total Indicated Run-out (TIR)
- Flatness
- Other features
- Indirect measurement
- Installing/Aligning Shaft Coupling (i.e. using rim and face, feeler gauge, and laser methods); Installing/Aligning/Tensioning: Belt Drive (i.e. single, multiple belt systems; using V-belts, timing, and HTP types) and Chain Drive (i.e. single, multiple chain systems)
- How to mount a motor
- How to correct for a soft foot on a motor
- How to level motors and shaft
- Installing flexible, flange, grid, and chain couplings
- Couplings identification (given a specification)
- Manufacturer’s documentation to locate alignment specifications of a coupling
- Measuring shaft speed using a tachometer
- Shaft alignment, using the following techniques:
- Feeler gauge and straight edge
- Rim and face
- Dial indicators
- Laser aligning equipment
- Installation of:
- Multiple V-belt drive onto a shaft with a bushing
- Timing belt or HTD belt onto a shaft using a bushing
- Split taper, QD, and taper lock bushings
- Identification of sheaves and V-belts specifications
- Identification of V-belt drive components (given a specification)
- Aligning V-belt drive using a straight edge
- Checking tension of a V-belt drive using a tension tool
- Tensioning V-belt drive by positioning the prime mover
- Interpreting specifications of sprockets and chains (given a specification)
- Installing chain drive using proper tools
- Aligning chain drive using a straight edge
- Checking tension of a chain drive using a straight edge and rule
- Tensioning a chain drive by positioning the prime mover
- Install, Align, and Adjust a Spur Gear Drive and a Right Angle Gear Drive
- How gears are attached to shafts through keys and keyways
- Interpreting specifications of gears
- Identifying spur and right angle gear components (given a specification)
- Aligning gear drive using a straight edge
- How to check backlash of gears using a dial indicator per specifications
- Install, Align, and Adjust a Pillow Block and Flange Block Bearing
- Interpreting specifications of pillow block and flange bearings
- Identifying pillow block bearings (given a specification)
- Install, align, and adjust pillow block and flange bearings
- Lubrication Points on a Machine (i.e. select and apply lubricant to machine according to maintenance schedule)
- Importance of a lubrication plan
- How to identify all oil and grease lubrication points using the manual
- Identify/select correct lubricant given a specification from the manual.
- Procedure for safe handling and storage of lubricants
- Lubricate bearings using Zerk fittings
- Grease gun to lubricate a bearing
- How to fill an oil cup
- Inspecting/filling automatic lubricators
- What is lubrication oil
- What is lubricating grease; different grades/usage
- Purpose of vent plugs
- Purpose of additives and viscosity
- Effects of over and under lubrication of bearings
- Troubleshooting Techniques for Shaft Couplings, Chain Drives and Belt Drives
- Identifying cause of wear or malfunction of a flexible coupling through visual inspection
- Perform troubleshooting techniques to analyze wear or malfunction of:
- V-belt drive
- Chain drive
- Gear drive
- Pillow block bearing
Effective Term: Full Academic Year 2020/21 |
|
-
AIT 115 - Hydraulic Systems 3 Credits, 5 Contact Hours 2 lecture periods 3 lab periods
Overview of the NIMS areas of hydraulic systems of a manufacturing facility. Preparation to sit for the NIMS Duty Area 3: Basic Hydraulic Systems Certification Exam.
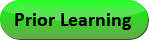.png)
Course Learning Outcomes
- Read and interpret basic fluid power schematics including identifying schematic symbols, process flow, and operation of the components and systems.
- Start up and shut down a hydraulic system, and adjust hydraulic pressure control valves in a system that uses a fixed displacement pump.
- Select and adjust hydraulic actuator speed using a flow control valve.
- Inspect and change a hydraulic filter; and inspect, add, change hydraulic fluid.
- Connect, adjust, and disconnect flexible and rigid hydraulic conductors.
- Install, test, and troubleshoot the operation of components in a basic hydraulic linear or rotary actuator given a schematic.
Performance Objectives:
- Employ mechanical fabrication procedures.
Outline:
- Basic Fluid Power Schematics (e.g. Identifying Schematic Symbols, Process Flow, Operation of the Components/Systems)
- Basic hydraulic components (given NFPA/ISO schematic symbol)
- Operation of circuits using:
- Single stage hydraulic direction control valves with manual and electrical operators
- Two stage hydraulic direction control valves with manual and electrical operators
- Various types of: spool centers, 2-position/3-position and 2/3/4 way designs
- Operation of hydraulic circuits (e.g. using accumulators, pump uploading, remote pressure control, rapid traverse slow feed, pilot-operated check valves)
- Interpretation of hydraulic line types on a schematic
- Operation of a basic hydraulic circuit (given a schematic)
- Basic pneumatic components (given their NFPA/ISO schematic symbol) identification
- Pneumatic line types on a schematic
- Operation of a basic pneumatic circuit given a schematic
- Start Up/Shut Down a Hydraulic System; Adjust Hydraulic Pressure Control Valves in a System that Uses a Fixed Displacement Pump
- Start up a hydraulic power system safely (including pre-start inspection)
- Shut down a hydraulic power system safely
- Manufacturer’s documentation per specific application to determine correct operating pressure
- Reading a pressure gauge
- Adjusting system operating pressure using a relief valve
- Manual valves operation (to direct system flow)
- Adjusting pressure of a pressure reducing valve
- Adjusting system operating pressure
- Pressure-flow characteristics of types of:
- Relief valves
- Direct and pilot operated
- Operation of:
- Double acting cylinder
- Motor
- Hydraulic sequence valve
- Pressure reducing valve
- Pressure-flow characteristics of displacement pumps:
- Fixed
- Variable
- How to do pressure checks and charge accumulators
- Pressure vs. force/torque output characteristics of cylinders and motors
- Pascal’s law, its importance in reading system pressure
- Selecting/Adjusting Hydraulic Actuator Speed (Using a Flow Control Valve)
- Actuator speed adjustment using:
- Needle valve
- Non-compensated flow control valves
- Compensated flow control valves
- Flow control valves adjustment in meter-in and meter-out configurations
- Measuring actuator speed
- Operation of:
- Needle valve
- Flow control valve
- Compensated flow control valve
- Meter-in circuits
- Meter-out circuits
- Flow vs. speed characteristics of a hydraulic cylinder and a motor
- Calculating pump flow rate requirements (given actuator speeds and sizes)
- Calculating pump flow rate (given pump size and speed)
- Inspecting/Changing a Hydraulic Filter to Maximize Hydraulic Fluid Cleanliness
- Interpreting filter specifications/models to determine correct filter
- Manufacturer’s documentation to determine frequency of change
- When to replace a filter based on pressure differential across the filter
- Measuring pressure differential across a filter
- Replacing:
- Spin-on filter
- Cartridge filter
- Symptoms of a required strainer
- Replacing strainer
- Inspecting, Adding, and Changing a Hydraulic Fluid
- Inspecting fluid levels through level gauge; determining when to add fluid
- Adding fluid to a hydraulic system
- Replacing hydraulic fluid using a filter cart
- Fluid inspection through sight, touch, and smell to determine if it should be replaced
- Fluid inspection for water and visible contaminants
- Water and contaminants removal from a hydraulic system (including, but not limited to, flushing and refilling system)
- Interpreting oil specifications (i.e. to determine if an oil meets the specifications specified by the machine manufacturer)
- Manufacturer’s documentation to determine the correct oil to use in a hydraulic system
- Taking fluid sample, preparing for submittal to a testing lab
- Connecting, Adjusting, and Disconnecting Flexible and Rigid Hydraulic Conductors
- Interpreting pipe, hose, and tubing specifications
- Identification of type and size of hose, tubing, and hydraulic fittings (given a sample)
- Safety procedures to make sure pressure is removed before disconnecting conductors
- Proper fitting tightening; consequences of over-tightening
- How to attach/tighten:
- Hydraulic steel tubing, using wrenches and ferrule fittings
- Hydraulic fittings to components with threaded ports, using wrenches and applicable thread sealant
- Hydraulic hose, using wrenches and swivel fittings
- Hydraulic hose, using wrenches and straight thread O-ring fittings
- Adjusting the position and alignment of conductors for proper operation
- How to make hydraulic hose using proper fittings
- O-ring
- Operation
- Installation
- How specified
- Installing, Testing the Operation of Components in a Basic Hydraulic Linear or Rotary Actuator (Given a Schematic)
- Installing/connecting hydraulic components in basic functional circuit (given a schematic)
- Replacing subplate-mounted directional, flow, and pressure control valves in a hydraulic system
- Replacing a threaded port valve
- Mounting/aligning a hydraulic cylinder or a motor
- Types of cylinder and motor mounting methods, and their applications
- Operating a hydraulic system to determine that it is performing correctly
- Proper bleeding procedures of a hydraulic system following component replacement
- Troubleshooting a Basic Hydraulic Linear or Rotary Actuator Circuit
- Basic components in a hydraulic circuit using in-circuit tests troubleshooting
- Using flow and pressure instruments to take hydraulic circuit readings during in-circuit testing
- Flow vs. pressure drop characteristics of components and conductors and their impact on system operation
- Systematic methodologies to troubleshoot basic hydraulic circuits with linear and rotary actuators
- Types of failure of basic hydraulic components
Effective Term: Full Academic Year 2020/21 |
|
-
AIT 120 - Pneumatic Systems 3 Credits, 5 Contact Hours 2 lecture periods 3 lab periods
Overview of the NIMS areas of pneumatic systems of a manufacturing facility. Preparation to sit for the NIMS Duty Area 4: Pneumatic Systems Certification Exam.
Course Learning Outcomes
- Determine and adjust pneumatic system operating pressure using a regulator.
- Select and adjust pneumatic actuator speed using a flow control valve.
- Inspect, drain, and change a pneumatic filter; inspect, fill, and adjust a pneumatic lubricator.
- Connect, adjust, and disconnect flexible and rigid pneumatic conductors.
- Startup and shutdown a reciprocating air compressor, and adjust operating pressure using a pressure switch.
- Install, test, and troubleshoot the operation of components in a basic: pneumatic linear or rotary circuit, and pneumatic circuit that uses vacuum generators (given a schematic for each).
Outline:
- Determining/Adjusting Pneumatic System Operating Pressure using a Regulator
- Operation of relieving and non-relieving pneumatic regulators
- Pressure vs. force/torque output characteristics of cylinders and motors
- Pascal’s law (its importance in reading system pressure)
- Interpreting/converting between air pressure units of measure
- Compressibility characteristics of air; their impact on system operation
- Operation of circuits using:
- Pneumatic direction control valves with manual and electric operators
- Various types of: spool centers, 2-position/3-position, pilot operated, cam-operated, and 2/3/4/5 way designs
- Reading a pressure gauge
- Manufacturer’s documentation to determine correct operating pressure
- Adjusting pneumatic regulator pressure
- Operating a branch shutoff valve to enable flow to a system branch
- Selecting/Adjusting Pneumatic Actuator Speed (Using a Flow Control Valve)
- Operation of:
- Needle valve
- Flow control valve
- Meter-in circuits
- Meter-out circuits
- Flow vs. speed characteristics of a pneumatic cylinder and a motor
- Effect of system pressure on pneumatic actuator speed
- Adjusting actuator speed using:
- Needle valve
- Flow control valve
- Manifold mounted flow control valves
- Adjusting flow control valves in meter-in/meter out configurations
- Measuring actuator speed
- Inspecting, Draining, and Changing a Pneumatic Filter
- Replacing a cartridge filter
- When to replace a filter based on:
- Inspection
- Pressure differential
- Manufacturer’s recommendations
- Interpreting filter specifications/models to determine correct filter
- Manufacturer’s documentation to determine frequency of change
- Operating the drain on a pneumatic filter
- Operating water removal systems on a pneumatic filter
- Recognizing symptoms of excessive water in a compressed air system
- Inspecting, Filling, and Adjusting a Pneumatic Lubricator
- Manufacturer’s documentation to determine correct lubricant
- Proper lubricating media definition
- Inspecting fluid level in a lubricator
- Adding lubricating oil to a lubricator
- Setting lubrication rate on a lubricator
- Connecting, Adjusting, and Disconnecting Flexible and Rigid Pneumatic Conductors
- Safety procedures (to make sure pressure is removed before disconnecting conductors)
- Attaching/tightening pneumatic:
- Steel tubing, using wrenches and ferrule fittings
- Fittings to components with threaded ports, using wrenches and thread sealant when appropriate
- Hose, using wrenches and strait-thread, barb, ferrule, and push-on fittings
- Adjusting the position/alignment of conductors for proper operation
- Interpreting pipe, hose, and tubing specifications
- Identification of type and size of hose, tubing, and fittings (given a sample)
- Identification of fittings and application (given a sample) and limitations for use of each
- Startup/Shutdown a Reciprocating Air Compressor, and Adjusting Operating Pressure Using a Pressure Switch
- Calculating air consumption from a receiver (given a pressure change)
- Interpreting/converting between air flow rate units
- Start up an air compressor system safely (including pre-start inspection)
- Shut down and drain a reciprocating air compressor system safely
- Operating manual valves to direct system flow
- Manufacturer’s documentation to determine correct operating pressure
- Adjusting system operating pressure using a pressure switch
- Adjusting working pressure with a regulator
- Installing, Testing the Operation of Components in a Basic Pneumatic Linear or Rotary Circuit (Given a Schematic)
- Installing/connecting pneumatic components in basic functional circuit (given a schematic)
- Replacing subplate-mounted directional valve in a pneumatic system
- Replacing a threaded port valve
- Mounting/aligning a pneumatic cylinder or a motor
- Operating a pneumatic system to determine that it is performing correctly
- Types of cylinder and motor mounting methods and their applications
- Installing, Testing the Operation of Components in a Basic Pneumatic Circuit That Uses Vacuum Generators (Given a Schematic)
- Interpreting vacuum units of measurement
- Pascal’s law (in relation to vacuum)
- Calculating lifting force of a vacuum cup (given vacuum level and manufacturer’s data)
- Common hose types, fittings, and sealants used in vacuum applications
- Identification of vacuum system and safeguards
- Installing/connecting a vacuum generator and vacuum cups
- Troubleshooting a Basic Pneumatic Linear or Rotary Actuator Circuit
- Basic components in a pneumatic circuit using in-circuit tests troubleshooting
- Flow and pressure instruments (to take pneumatic circuit readings during in-circuit testing)
- Flow vs. pressure drop characteristics of pneumatic components and conductors, and their impact on system operation
- Systematic methodologies to troubleshoot basic pneumatic circuits with linear and rotary actuators
- Types of failures of basic pneumatic components
Effective Term: Full Academic Year 2020/21 |
|
-
AIT 125 - Electrical Systems I 3 Credits, 5 Contact Hours 2 lecture periods 3 lab periods
Overview of the area of electrical systems of a manufacturing facility. Preparation to sit for the NIMS Duty Area 5: Electrical Systems Certification Exam.
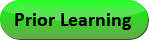.png)
Course Learning Outcomes
- Read and interpret electrical motor control and programmable logic controller system schematics, including identifying schematic symbols, signal flow, and operation of the components and system.
- Adjust and test limit switches, pressure switches, float switches, and electronic proximity sensors.
- Use a multimeter to measure voltage, current, and resistance in an electrical circuit to verify system operation and power levels.
- Select, install, and test: fuses, circuit breakers, electrical relay control components in a control system, and electro-fluid power components and circuits.
- Troubleshoot a solenoid-operated fluid power relay control circuit.
Performance Objectives:
- Test and replace transformers.
Outline:
- Reading, Interpreting Electrical Motor Control and Programmable Controller System Schematics (e.g. Identifying Schematic Symbols, Signal Flow, and Operation of the Components and System)
- Electrical components identification (given their NEC/ISO schematic symbol)
- Interpreting electrical control and power line types on a schematic
- Interpreting the operation of a basic electrical power and control circuits (given a schematic)
- Following signal flow on an electrical control or power schematic
- Interpreting control schematics (given a ladder logic diagram)
- Interpreting power diagrams associated with a PLC and all related input/output devices
- Adjusting, Testing Limit Switches, Pressure Switches, Float switches, and Electronic Proximity Sensors
- Adjusting/ testing the trip point of:
- Limit switch, float switch, and pressure switch
- Capacitive sensor, inductive sensor, photoelectric sensor, Hall Effect sensor, fiber optic, magnetic reed sensor, and light curtain switches
- Operation of limit, float, and pressure switches
- Operation of capacitive sensors, inductive sensors, photoelectric sensors, Hall Effect sensors, fiber optic sensors, and magnetic reed sensors
- Using Multimeter to Measure Voltage, Current, and Resistance in an Electrical Circuit to Verify System Operation and Power Levels
- Multimeter to measure:
- Incoming voltage and current to an electrical circuit
- Voltage and current in an electrical circuit
- Resistance in an electrical circuit
- Multimeter to perform a continuity check in an electrical circuit
- Concepts of resistance, voltage, current, and power
- Using a clamp on amp meter
- Application of a multimeter to measure continuity, resistance, voltage, and current
- Ohm’s law definition (to determine power flow in electrical circuits)
- Calculating power in an electrical circuit (given current and voltage)
- Operation of parallel and series electrical circuits
- Selecting, Installing, and Testing Fuses and Circuit Breakers
- Size fuses and circuit breakers (in accordance with NEC requirements for a given power draw in an electrical circuit with consideration to ampacity of wiring in that circuit)
- Installing fuses and circuit breakers in electrical circuits
- Procedure to test fuses
- Inspecting circuit breakers (to determine if tripped)
- Resetting circuit breakers
- Operation of fuses, circuit breakers, and GFCI’s
- Fuse types identification and their use
- Installing, Testing Electrical Relay Control Components in a Control System
- Operation of control transformers, pushbutton switches, selector switches, control relays, magnetic motor starters, overloads, indicator lamps, electronic sensors, drum switches, solenoid operated fluid power valves, capacitors, resistors, and disconnect switches
- Operation of basic single direction and reversing direction motor control circuits with interlocks and sensors
- Installing/connecting NEMA/IEC relay control components in a control circuit (given a wiring diagram or schematic)
- Installing wiring between components:
- Control cabinet using raceways
- Located in different enclosures via conduit
- Replacing failed relay contacts and coils
- Installing, Testing Electro-Fluid Power Components and Circuits
- Operation of solenoid-operated hydraulic and pneumatic valves
- Operation of relay-controlled sequence fluid power circuits
- Installing/connecting solenoid-operated hydraulic and pneumatic valves in a control circuit (given a wiring diagram or schematic)
- Manual overrides to test operation and describe the potential negative effects or consequences
- Troubleshooting a Solenoid-Operated Fluid Power Relay Control Circuit
- Types of failures of solenoid-operated valves
- Solenoid-operated hydraulic and pneumatic directional control valves troubleshooting (using in-circuit tests)
- Systematic methodologies to troubleshoot electro-fluid power relay control circuits
- Testing, Replacing Transformers
- Transformer ratio definition
- Types and configurations of transformers and their application
- Rating of a transformer
- Connection point and taps for each type of transformer
- Testing a transformer
- Disconnecting/reconnecting primary and secondary transformers
- Replacing primary and secondary transformers
Effective Term: Full Academic Year 2020/21 |
|
-
AIT 130 - Maintenance Piping 3 Credits, 5 Contact Hours 2 lecture periods 3 lab periods
Overview of the area of maintenance of piping systems for manufacturing or industrial facilities. Preparation to sit for the NIMS Duty Area 9: Maintenance Piping Certification Exam.
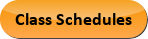
Course Learning Outcomes
- Read and interpret piping schematics.
- Identify and select proper materials for installation and replacement.
- Prepare material for installation or repair of piping systems.
- Assemble and disassemble piping systems.
Performance Objectives:
- Employ mechanical fabrication procedures.
Outline:
- Piping Schematics
- Components
- ISA schematic symbols
- Control valves
- Direction
- Pressure
- Flow
- Cylinders
- Motors
- Instrumentation
- Pumps
- Various types of operators
- Filters
- Piping line types and symbols
- Connectors and fittings specifications for processes
- Operation of basic piping systems (given a schematic)
- Installation and Replacement Materials (i.e. Selection, Identification)
- Proper tools
- Piping types and size by:
- Schedule
- Material
- Tubing type and size by:
- OD/ID
- Material
- Sealants, gaskets, solder types
- Hoses (e.g. types and ratings)
- Hangers (e.g. types, uses)
- Identifying correct materials based on process and medium compatibility
- Fitting, connections
- Pipe or tubing
- Sealants, gaskets, or solder/weld
- Preparing Materials for Installation or Repair
- Appropriate measurement of materials for:
- Cutting
- Bending
- Calculate pipe length for:
- Installation
- Repair
- Pipe and tubing devices
- Threading machines
- Tubing benders
- Cutting devices
- Surface preparation (for all types of connections)
- Measure, cut, and prepare:
- Iron pipes
- PVC or CPVC pipes
- Tubing
- Assembling/Disassembling Piping Systems
- Support devices (for all types of pipe systems)
- Pipe strain and effects on equipment
- Proper torque (importance of)
- Proper installation of sealants and gaskets
- Remove and install:
- Thread pipe and fittings
- Tubing and fittings
- PCV and CPVC pipe and fittings
- Bolted pipe flanges
Effective Term: Full Academic Year 2020/21 |
|
-
AIT 135 - Electronics Assembly & Fabrication I 3 Credits, 4 Contact Hours 2 lecture periods 2 lab periods
Fundamental principles of assembly and manufacture of electronics. Includes electronics safety, hand and power tool usage, measure tools, quality control/Statistical Process Control, and ElectroStatic Discharge (ESD). Also includes clean room procedures, electronics print reading, wiring harnesses, soldering, desoldering and rework, cleaning, prototyping, and high volume production methods.
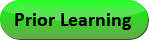.png)
Course Learning Outcomes 1. Demonstrate safe electronic/electrical work procedures.
2. Use common basic hand and power tools.
3. Demonstrate skill in various methods of soldering.
4. Describe electronic components and their function.
5. Explain Electrostatic Discharge (ESD) and how to avoid damage caused by it.
6. Demonstrate appropriate procedures for working in a clean room environment. Outline:
- Electronics Safety
- Lockout/Tagout
- Personal Protective Equipment
- Associated hazards for electrical/electronic work
- Electric shock/burns
- Striking by moving/flying objects
- Lifting
- Chemical/hazardous materials/MSDS
- Fire
- Grounding, insulated tools, ground fault circuit interrupt protection
- Emergency response and first aid
- Electronic Components
- Resistors
- Inductors and capacitors
- Diodes and transistors
- Semiconductor devices
- Microprocessors/microcontrollers
- Transformers and power supplies
- Circuit protection
- Connectors and terminals
- Electronics Prints/Schematic Reading
- General print principles
- Electrical and electronic schematics
- Symbols
- Connections
- Layouts
- Example schematics of common devices
- Electrostatic Discharge (ESD), Product and Component Handling
- Definitions
- Why it matters
- Prevention equipment and methods
- Electronics packaging
- Handling
- Cleanroom Procedures
- Description
- Classes of cleanroom, when and how used
- Acceptable and restricted/prohibited materials
- Attire and proper methods for putting on and removing
- Hand and Power Tools Used in Electronic/Electrical Assembly
- Common tools
- Proper use and care
- Safety considerations
- Soldering
- Manual soldering
- Solders, fluxes
- Soldering equipment
- Through hole
- Surface mount
- Automated soldering
- Wave
- Dip
- Robotic
- Desoldering and Rework
- Tools
- Methods
- Assembly Cleaning
- Prototyping
- Bread boards
- Prototyping
- Perfboard and solder
- Generic printed circuit board
- “Dead Bug”
- Custom printed circuit board
Effective Term: Full Academic Year 2019/20 |
|
-
AIT 205 - Electronic Control Systems I 3 Credits, 5 Contact Hours 2 lecture periods 3 lab periods
Overview of the area of Electronic Control Systems I of a manufacturing or industrial facility. Preparation to sit for the NIMS Duty Area 6: Electronic Control Systems Certification Exam.
Prerequisite(s): AIT 125
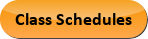
Course Learning Outcomes
- Connect, test, and troubleshoot: linear and switching DC power supplies; and basic PLC and controlled components.
- Install and test solid-state AC and DC discrete and analog relays.
- Install, adjust, and test analog sensors and signal conditioning equipment.
- Connect and transfer programs to a programmable controller (PLC) using a PC.
- Create a basic PLC ladder-style program.
Outline:
- Linear and Switching DC Power Supplies (e.g. Connecting, Testing)
- Measure output (i.e. to determine noise or quality of filtering)
- Operations of:
- PN junction diodes
- LED’s
- Zener diodes
- Voltage regulators
- Half wave and full wave rectifiers
- Capacitive, inductive, and resistive power filters
- Operations of biopolar and FET transistors (used in power supplier), and SCRS
- Operation of linear and switching power supplies
- Connecting
- Testing
- Solid-State AC and DC Discrete and Analog Relays (e.g. Installing, Testing)
- Operation of:
- Discrete and analog solid-state relays
- Sourcing and sinking circuits
- Solid-state relay:
- Styles (also of mountings)
- Schematic symbols
- Specifications
- Solid-state relays in electrical circuit (given schematic)
- Installation
- Failures
- Multimeter testing
- Analog Sensors and Signal Conditioning Equipment (e.g. Installing, Adjusting, Testing)
- Operation of:
- 4-20 ma current output and voltage output signals
- Signal conditioners for analog sensors
- Thermistors, RTD temperature sensors, and thermocouples
- Resistive, capacitive, and piezoelectric pressure sensors
- Interpreting specifications for analog sensors
- Sensors and associated signal conditioners
- Connecting (installing, adjusting)
- Testing
- Types of failures
- Adjust range and zero point (of analog signal conditioner)
- Connecting/Transferring Programs to a Programmable Controller (PLC) (Using a PC)
- Basic operation of a PLC
- Basic operation and navigation of PC software for PLCs
- Nomenclature for PLC program file elements
- How PLCs are wired to power, I/O, and network devices
- PLC network operations
- Devices: how identified on PLC network
- Ladder logic (e.g. use and importance of comments)
- PLC modes (e.g. able to change modes)
- PLC and PC
- Connecting
- Transfer programs between PC and PLC via:
- Serial
- USB
- Ethernet connection
- Basic PLC Ladder-Style Program
- PC software, PLC program, and reviewing files
- Interpreting PLC programs:
- Internal and external contacts
- Timers
- Counters
- Non-retentive output coils
- Internal coils
- Subroutines
- Conditional commands
- Math commands
- Interpreting PLC programs that control/sequence electric motors and fluid power systems
- PLC I/O diagram interpretation
- I/O device identification by memory address
- Function of analog I/O card
- Address scheme of a PLC
- Operation and basic PLC commands related to:
- Internal and external contacts
- Timers
- Counters
- Non-retentive output coils
- Internal coils
- PLC Component Installation and Testing
- Connecting and configuring HMI to a PLC via network or direct connection
- Installing and configuring PLC and its components
- Powering up HMI
- Viewing data from HMI panel
- HMI screen navigation
- Touchscreen
- Function keys
- PLC program operation interpretation (using ladder logic program to interface to a hardware component)
- PLC System and Controlled Components Troubleshooting
- PLC troubleshooting flow chart
- PLC program history
- Systemic methodologies
- HMI
- To troubleshoot PLC-controlled machine
- To troubleshoot HMI on a PLC-controlled machine
- Tune performance of PLC-controlled machine via:
- Mechanical adjustments
- Electrical adjustments
- Software adjustments
- Team skills to install, troubleshoot, and optimize systems
Effective Term: Full Academic Year 2019/20 |
|
-
AIT 210 - Electronic Control Systems II 3 Credits, 5 Contact Hours 2 lecture periods 3 lab periods
Continuation of AIT 205 . Overview of the area of Electronic Control Systems II of a manufacturing and industrial facility. Preparation to sit for the NIMS Duty Area 6: Electronic Control Systems Certification Exam.
Prerequisite(s): AIT 205 or concurrent enrollment.
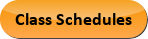
Course Learning Outcomes
- Install and operate an AC variable frequency volts-to-hertz motor drive systems.
- Effectively use computer applications, information systems, and programming.
Outline:
- AC Variable Frequency Volts-to-Hertz Motor Drive System (e.g. Installation, Operation)
- Operation of an AC Variable Frequency Drive (VFD) motor control system
- Function and use of common AC drive parameters
- Operation of IGBT and FET transistors as used in VFDs
- VFD alarms/diagnosis and their importance
- Grounding Rings (purpose, and use with VFD)
- Connect and operate:
- AC VFD with AC motor
- AC VFD with relay control circuit
- AC VFD using onboard HMI
- Manual operation
- View and edit parameters
Effective Term: Full Academic Year 2019/20 |
|
-
AIT 215 - Process Control Systems 4 Credits, 6 Contact Hours 3 lecture periods 3 lab periods
Overview of the area of Process Control Systems of a manufacturing or industrial facility. Preparation to sit for the NIMS Duty Area 7: Process Control Systems Certification Exam.
Prerequisite(s): AIT 125
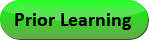.png)
Course Learning Outcomes
- Read and interpret process control system documentation including identifying components on a P&ID diagram, instrument tag, and instrument index.
- Calibrate, adjust, and test analog sensors and signal conditioning equipment.
- Calibrate, adjust, and test pneumatic proportional valves and I/P transmitters.
- Build a simple/basic process signal loop system.
Outline:
- Interpreting Process Control System Documentation (e.g. Identifying Components on a P&ID Diagram, Instrument Tag, Instrument Index)
- Process control components identification (given their ISA P&ID schematic symbol)
- Operation of a process control system (given a P&ID diagram)
- Components on a P&ID diagram identification (given their instrument tags)
- Instrument data interpretation (given on an instrument list)
- Analog Sensors and Signal Conditioning Equipment (i.e. Calibration, Adjustment, Testing)
- Operation of current-output and voltage-output signal sensors
- Operation of signal conditions for analog sensors
- Operation of various transmitter types
- Analog sensors and specification interpretations
- Units of measurement variables (conversions from raw data units, 4-20ma)
- Connecting and testing
- Span and zero point adjustments
- Failure types
- Pneumatic Proportional Valves and I/P Transmitters (e.g. Calibration, Adjustment, Testing)
- Current-output and voltage-output of signal final control elements
- I/P converters operation
- Pneumatic proportional valves operation
- 2-way and 3-way Pneumatic PCV (connect and test)
- I/P converter (connect, test, calibrate)
- Pneumatic proportional valves calibration
- Building a Simple/Basic Process Signal Loop System
- Identification of basic signal loop process control systems components
- Drawing a print of a single loop process control system
- Connecting, calibrating, and tuning
- PID process control loop operation
- Single loop process controller operation
- PCL process control and distributed control systems (DCS) basic operation and application
Effective Term: Full Academic Year 2019/20 |
|
|
|
-
AIT 235 - Electronics Assembly & Fabrication II 3 Credits, 4 Contact Hours 2 lecture periods 2 lab periods
Continuation of AIT 135 . Fundamental principles of creating electronic prototypes, wire and cable termination, electronics safety, and wiring harness assembly. Includes fabrication of electronics enclosures, electrical control systems, and electronic control systems. Also includes checking torque applied to fasteners used in electrical and electronic systems.
Prerequisite(s): AIT 135
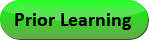.png)
Course Learning Outcomes 1. Demonstrate safe electronic/electrical work procedures.
2. Differentiate between various prototyping methods and their appropriate application.
3. Demonstrate effective wire/cable termination and wiring harness assembly.
4. Apply appropriate electronics enclosure fabrication procedures.
5. Fabricate electrical/electronic control systems that meet applicable standards.
6. Test fastener torque using various tools. Outline:
- Electronics, Electrical and Fabrication Safety Review
- Lockout/Tagout, Personal Protective Equipment
- Associated hazards for electrical/electronic work
- Electric shock/burns
- Striking by moving/flying objects
- Lifting
- Chemical/hazardous materials/MSDS
- Fire
- Grounding, insulated tools, ground fault circuit interruption protection
- Emergency response and first aid
- Prototyping
- Perfboard and solder
- Generic printed circuit board
- “Dead Bug”
- Custom printed circuit board
- Wire wrap
- Wire Termination and Wiring Harnesses
- Terminal and plug types
- Installing terminals and plugs
- Assembly
- Testing
- Troubleshooting and repair
- Enclosure Fabrication
- Design
- Measurement and layout tools
- Fabrication techniques
- Layout
- Projects
- Electrical and Electronic Control System Fabrication
- Component layout
- Raceway/wire routing
- Mounting internal and front panel components
- Wiring connection and termination
- Testing and troubleshooting
- Torque
- Principles of fasteners and effects of torque on threaded fasteners
- Torque theory
- Mechanical torque devices
- Electronic torque devices
Effective Term: Full Academic Year 2019/20 |
|
-
AIT 250 - Automated Industrial Technology Capstone 3 Credits, 5 Contact Hours 2 lecture periods 3 lab periods
An examination of the integration of mechanical, hydraulic, pneumatic, electrical, piping, electronic control, and process control systems. Experience in designing, building, maintaining, troubleshooting, and repairing such integrated systems will be gained.
Prerequisite(s): AIT 225 or concurrent enrollment.
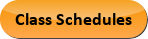
Course Learning Outcomes 1. Demonstrate safe working procedures when working with integrated systems.
2. Program a stepper motor.
3. Adjust various pneumatic and electric actuators.
4. Create designs that integrate mechanical, hydraulic and/or pneumatic, piping, electronic control, and process control systems.
5. Determine the problem(s) to be resolved by a project; and analyze and correct design flaw(s). Performance Objectives: 1. Operate various types of single and multiple automated manufacturing stations.
2. Connect automated manufacturing stations to function in unison.
3. Effectively create all necessary documentation for a project.
4. Fabricate, test, and evaluate prototypes of designs. Outline:
- Safety (review)
- Lockout/Tagout
- Hydraulic, pneumatic, electrical, electronic, and mechanical system hazards
- Housekeeping considerations
- Automation Operations
- Introduction to mechatronics
- Control system principles
- Machine operation
- Component Adjustment
- Manual station operation
- Pneumatic/electric pick and place actuators
- Sensors
- Pick and Place Feeding Station
- Station operation
- Station component adjustment
- Module sequencing
- Station sequencing
- Gauging
- Station operation
- Station component adjustment
- Module sequencing
- Station sequencing
- Indexing
- Station operation
- Station component adjustment
- Module sequencing
- Station sequencing
- Stepper motor programming
- Sorting and Queuing
- Station operation
- Station component adjustment
- Module sequencing
- Station sequencing
- Servo Robotic Assembly
- Station operation
- Station component adjustment
- Module sequencing
- Station sequencing
- Torquing
- Station operation
- Station component adjustment
- Torque adjustment
- Module sequencing
- Station sequencing
- Parts Storage
- Station operation
- Station component adjustment
- Module sequencing
- Station sequencing
- Multiple Station Control
- Discrete I/O handshaking
- System startup/halt
- System stop/reset
- FMS programming
- Capstone Project
- Problem identification
- Researching and documenting information
- Methods of Recording
- Protecting Information From Loss and Tampering
- Design process
- Idea generation (i.e. brainstorming and researching ways similar problems have been solved)
- Idea screening methods
- Testing ideas against customer requirements
- Common pitfalls in the design process
- Determining specifications
- Prototypes and their creation
- Iterative testing and redesign to improve a design
- Continuous improvement
Effective Term: Full Academic Year 2019/20 |
|
-
AIT 260 - Manufacturing Mechanics 3 Credits, 4 Contact Hours 2 lecture periods 2 lab periods
Fundamental principles of the application, installation, lubrication, and maintenance of plain, ball and roller bearings. Includes an exploration of gaskets and seals, gear drives, brakes and clutches, linear ball brushings, and ball screw drives.
Prerequisite(s): AIT 110
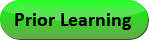.png)
Course Learning Outcomes 1. Demonstrate safe practices when working with mechanical drives and other mechanical systems.
2. Choose appropriate types of bearings, brakes, clutches, gaskets, and seals for mechanical function.
3. Recommend appropriate installation and maintenance procedures. Outline:
- Plain Bearings
- Solid plain bearings
- Lubrication
- Selection
- Maintenance and selection
- Ball Bearings
- Introduction to antifriction bearings
- Identification
- Mechanical bearing installation
- Temperature bearing installation
- Roller Bearings
- Identification
- Mechanical installation
- Temperature installation
- Applications
- Antifriction Bearing Selection and Maintenance
- Angular-contact bearings
- Bearing lubrication
- Selection
- Maintenance/troubleshooting
- Gaskets and Seals
- Gaskets
- O-ring seals
- Lip seals
- Mechanical seals
- Seal maintenance and selection
- Advanced Gear Drives
- Helical gear drives
- Right angle gear drives
- Speed reducers
- Speed reducer maintenance
- Gear Drive Selection and Maintenance
- Selection
- Lubrication
- Maintenance and troubleshooting
- Brakes and Clutches
- Brake and clutch concepts
- Brakes
- Friction clutches
- Cam clutches
- Brake/Clutch Selection and Maintenance
- Brake/clutch combinations
- Selection
- Maintenance
- Linear Ball Bushings
- Linear drives
- Applications
- Identification
- Maintenance and selection
- Ball Screw Drives
- Operation
- Applications
- Identification
- Selection and maintenance
Effective Term: Full Academic Year 2019/20 |
|
-
AIT 270 - Robotics I 3 Credits, 4 Contact Hours 2 lecture periods 2 lab periods
Fundamental principles of working safely with robots, and applications of and trends in industrial robotics. Includes types of robots, axes and coordinate systems, programming and operating robots. Also includes end effectors, and collaborative robots.
Prerequisite(s): AIT 100 and AIT 105
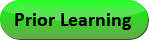.png)
Course Learning Outcomes 1. Recommend safe work procedures when working with robots.
2. Analyze applications and trends in industrial robotics.
3. Compare various robot, axes and coordinate types and systems.
4. Develop an industrial robot program to perform a specified task.
5. Identify various end effectors. Outline:
- Definition of a Robot
- Robotics Safety
- Work spaces
- Physical barriers and interlocks
- Avoiding collision paths
- Lock Out/Tag Out
- Applications of Industrial Robots
- Material handling
- Loading and unloading machines
- Painting
- Welding, soldering, and adhesive application
- Assembly
- Picking (Warehousing)
- Trends in Robots
- Traditional robots
- Collaborative robots
- Use of vision systems
- Machine learning and Artificial Intelligence (AI)
- Industry 4.0, IoT, Smart Factories
- Types of Robots and Axes
- Definition of an axis
- Articulated (Arm)
- Cartesian (Gantry)
- Polar
- Cylindrical
- SCARA
- Delta
Effective Term: Full Academic Year 2019/20 |
|
-
AIT 275 - Robotics II 3 Credits, 4 Contact Hours 2 lecture periods 2 lab periods
Continuation of AIT 275. Fundamental principles of working safely with robots; robot auxiliary, subsystems, and components. Also includes robot maintenance, troubleshooting, repair, and a basic robot design project.
Prerequisite(s): AIT 270
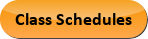
Course Learning Outcomes 1. Implement various robot vision systems.
2. Analyze various robotic subsystems and components.
3. Troubleshoot maintenance and repair issues on a robot.
4. Design a rudimentary, functional robot. Outline:
- Robotics Safety Review
- Robot Vision
- 1, 2, and 3 Dimensions
- Line scan
- Area scan
- Robot Subsystems and Components
- Structure
- Joints/Articulation
- Mechanical drive systems
- Servo and stepper motors
- Controllers
- Teach pendants
- Enclosures
- End effectors
- Maintenance
- Preventative
- Cleaning
- Lubrication
- Predictive
- Controller
- Electrical
- Structural
- Mechanical
- Safety
- Robot Troubleshooting
- Principles and methods
- Common problems
- Repair
- Disassembly
- Component repair
- Component replacement
- Reassembly
- Design and Build
- Machine Learning
Effective Term: Full Academic Year 2019/20 |
|
-
AIT 280 - Industry 4.0 and Industrial Control Systems 3 Credits, 4 Contact Hours 2 lecture periods 2 lab periods
Fundamental principles of existing and developing automation systems such as Supervisory Control and Data Acquisition (SCADA), Distributed Control Systems (DCS), Smart Factories, Industry 4.0, and the Internet of Things. Also includes an introduction to software used in SCADA and DCS, and practice setting up one of these systems.
Prerequisite(s): AIT 215 or concurrent enrollment.
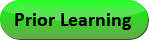.png)
Course Learning Outcomes 1. Explain the 5 Layer Automation Pyramid.
2. Describe Industry 4.0, Smart Factories, Internet of Things, and related terms.
3. Create an Industry 4.0 compliant production device or system. Outline:
- Definitions
- The 5 Layer Automation Pyramid
- Layer 1-Sensors, Actuators and Hardware
- Sensor types, applications, and developments
- Actuator types, applications, and developments
- Hardware aspects
- Networking
- The Open Systems Interconnection (OSI) seven layer model
- Cabling and other media
- Topologies
- Network speed and reliability
- Network security
- Layer 2-Local Control Devices and Data Collection Devices
- Programmable Logic Controllers (PLCs)
- Remote terminal units
- Human machine interface
- Proportional integral derivative controllers
- Layer 3-Distributed Control Systems (DCS) and Supervisory Control and Data Acquisition (SCADA)
- Definition
- Common components and structures
- Software
- Examples
- Programming
- Layer 4-Manufacturing Execution Systems (MES)
- Layer 5-Enterprise Resource Planning (ERP)
- Related Principles
- Internet of Things
- Industry 4.0
- Smart Factories
- Digital Twin
- Digital Shadow
- Smart Maintenance
- Projects/Practicum
Effective Term: Full Academic Year 2019/20 |
|
-
AIT 285 - Sensors and Data Acquisition 3 Credits, 4 Contact Hours 2 lecture periods 2 lab periods
Fundamental principles of sensors such as sensor design, function, installation, maintenance, calibration, and repair. Includes brief exploration of signal conditioning, data acquisition, chart recorder operation, and data storage.
Prerequisite(s): AIT 215 or concurrent enrollment.
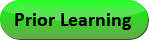.png)
Course Learning Outcomes 1. Describe the general purpose of sensors
2. Differentiate the operation, function, and application of different types of sensors
3. Calibrate sensors and/or connected equipment to assure correct operation
4. Describe signal conditioning and the operation of signal transducers
5. Connect, configure, and operate data acquisition equipment Outline:
- Purposes of Sensors
- The Big 4
- Pressure
- Temperature
- Flow
- Level
- Other Important Types of Sensors
- Strain
- Radiation
- Voltage and current
- Position-angular and linear
- Proximity
- Inductance
- Conductivity
- pH
- Photo
- Switches
- Principles of Operation
- Designs
- Property sensed, vs property signal
- Function
- Installation
- Calibration
- Maintenance
- Transmitters
- Signal conditioning
- Transducers/signal conditioning
- Introduction to Data Acquisition
- Introduction to chart recorders
- Digital chart recorder menu navigation
- Digital chart recorder configuration
- Chart Recorder Applications
- Thermocouple applications
- RTD applications
- Voltage/current/ohm applications
- Managing Chart Recorder Data
- Chart recorder display formats
- Continuous logging
- Fuzzy logging
- Digital chart recorder data transfer
- Special Chart Recorder Functions
- Alarms
- Math functions
- Replay mode
- Introduction to Chart Recorder Software
- Loading chart recorder data
- Graph events
- Graph display formatting
- Graph printing
Effective Term: Full Academic Year 2019/20 |
|
-
AIT 291 - Automated Industrial Technology Internship 3 Credits, 6 Contact Hours 0 lecture periods 6 lab periods
Supervised work experience in production environments. Includes experiences in maintenance, troubleshooting, repair of production environment and specific manufacturing processes. Also includes experiences in problem solving; working as a team; soft skills; time and resource management; and exposure to specific manufacturing processes.
Prerequisite(s): AIT 225 or concurrent enrollment.
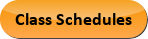
Course Learning Outcomes 1. Demonstrate professional workplace behavior.
2. Assess and report own professional growth over the course of the class.
3. Identify opportunities for continuing growth.
4. Allocate time, material, and other resources effectively.
5. Explain and evaluate manufacturing processes used at a manufacturing facility; and create solutions to identified problems Outline: I. Professional Workplace Behavior/Employabilty Skills
A. Attitude
B. Appearance
1. Hygiene
2. Proper attire
C. Commitment to continuing learning
D. Punctuality/Dependability
E. Working safely
F. Communication
G. Working in a team
II. Professional Growth
A. Self pre-assessment
1. Identifying strengths & opportunities for growth
2. Setting goals and creating plans to reach achieve those goals
B. Self post-assessment
1. Identifying successes and opportunities for further growth
2. Resources to help achieve that growth
III. Time and Resource Management
A. Identifying and prioritizing tasks and responsibilities
B. Evaluating time and other resources available
C. Analyzing wastes of time and resource
D. Creation and execution of plans to reduce those wastes
E. Measuring success of those plans
IV. Manufacturing Processes
A. Identification and evaluation of manufacturing processes in use
B. Analyzing effectiveness existing processes
C. Determining suitability of alternative processes
D. Apply quality control concepts and formulate potential improvements
E. Examine continuous improvement opportunities
V. Diagnosing Problems and Determining Solutions
A. Systems thinking
B. Troubleshooting methodologies
C. Determining solutions
Effective Term: Full Academic Year 2019/20 |
|
|
|