|
2023-2024 Workforce Catalog [ARCHIVED CATALOG]
|
UAIT 105 - Maintenance Operations Overview of the area of maintenance operations of a manufacturing facility. Preparation to sit for the NIMS Duty Area 1: Maintenance Operations Certification Exam.
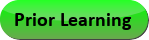.png)
Course Learning Outcomes:
- Perform machine operation including startup, emergency, and normal shutdown and manual functions.
- Monitor machine operation and verify that performance meets safety, production, and maintenance requirements.
- Locate, interpret, and store machine operation and maintenance documentation.
- Perform planned and unscheduled machine maintenance procedures in accordance with a company-approved maintenance plan.
- Perform a preventative maintenance procedure for a given machine to extend machine life and minimize downtime.
Outline:
- Machine Operation
- Safety checklist:
- Machine malfunction definition
- Standard operating procedures definition
- Operations to start and stop an operation
- When a machine needs to be shut down
- Lockout process (perform process)
- Monitoring Machine Operation; Verifying Performance Meets Production Requirements
- Confirming (with operator) machine is operating within specifications
- Five senses to observe machine operation and vibration (i.e. determine machine operating correctly, recognize malfunctions symptoms)
- Operator use of correct operation procedure evaluation
- Leaks, dirt, and loose connections
- Read:
- Pressure gauges
- Flow meters
- Fluid levels
- Temperature gauges
- Voltages and current
- HMI (monitor machine)
- Machine reading comparisons (i.e. machine documentation and performance specifications to determine if machine is performing within specifications)
- Record machine operation history (manual log or computer database)
- Locate, Interpret, and Store Machine Operation and Maintenance Documentation
- Methods of storing machine operation and maintenance documentation (accessible to the maintenance technicians and operators)
- Locate and interpret (for a given machine):
- Machine operation manuals, including: identification of safety requirements and features, performance specifications, stand operating procedures, startup/shutdown procedures
- Spare parts lists, vendor sources, and maintenance procedures
- Machine operation history logs, computer-based and manual
- Machine operating history from an HMI database
- Machine lubrication and preventive maintenance schedules from company or machine manufacturer documentation
- Planned and Unscheduled Machine Maintenance Procedures (In Accordance with a Company-Approved Maintenance Plan)
- Concept of total productive maintenance (TPM) definition (e.g. combination of preventive, predictive, and total company buy-in)
- Benefits and limitations of preventive/predictive maintenance
- Company procedures to inform production personnel of maintenance to be done on a machine
- Use of CMMS description
- When a work order is needed
- Steps to perform an unscheduled/planned maintenance procedure
- Concept of autonomous maintenance
- Elements of a comprehensive maintenance plan
- Methods of eliminating unplanned maintenance events
- Types of planned/unplanned maintenance procedures
- How to read, interpret, and resolve a work order
- Preventative Maintenance Procedure(s) for a Given Machine to Extend Machine Life and Minimize Downtime
- Describe preventive maintenance procedure given machine documentation
- Types of preventive maintenance tasks
- Identify and remove sources of contamination (e.g. select best methods of cleaning machine based upon continuous improvement principle)
- Predictive Maintenance on a Given Machine to Extend Machine Life and Minimize Downtime
- Basic elements and benefits of a predictive maintenance plan
- Types of predictive maintenance methods and their applications using basic senses (hearing, feeling, etc.) and their techniques:
- Vibration analysis
- Thermography
- Oil analysis
- Acoustic analysis
- Motor current analysis.
- Performing predictive maintenance
- Reading/Interpreting Technical Drawings of Parts and Assemblies with Tolerances and Basic GD&T
- Reading/interpreting technical drawings (of parts/assemblies with tolerances, basic GD&T)
- Line types and basic symbology
- Multi-view drawings of cylindrical and prismatic shaped parts
- Metric and English dimension conversions
- Dimension lines for linear, circular, and angular dimensions
- Title blocks
- Feature sizes using a drawing scale
- GD&T feature control frames
- Standard dimensional tolerance
- GD&T tolerances for form orientation, location
- Assembly drawings
- Assembly tolerances, interference fit concept
- Maximum material condition symbols
- Sectional cutaway views
- Threaded and non-threaded fastener specifications
- Type of fastener (given a sample)
- Fastener selection (for a given application)
- Sizes and types of washers, pins, nuts, locking devices
- Hand Tools to Inspect, Adjust/Tighten, and Assemble/Disassemble Equipment to Support Preventive Maintenance, Inspection, and Troubleshooting Activities
- Basic hand tool safety rules and application for use as defined by OSHA standards
- Concepts of how a fastener works, force, torque, dynamic and static torques, press fits, assembly tolerances
- Proper fastener selection
- Select and (proper) use of:
-
-
- Fixed wrenches
- Allen/hex key wrenches
- Ratchet wrenches
- Click-type torque wrench
- Pliers, clamps, and mallets.
- Pneumatic powered torque wrenches
- Electric powered hand tools (e.g. drills, torque wrenches, and screwdrivers)
- Methods to protect parts and components during handling and storage
- Assembling parts using:
- Threaded fasteners, washers, and nuts
-
-
- Pins, keys, clips, snap rings, and tie wraps
- Tightening parts using correct bolt pattern sequence
- Hoists and Other Tools to Safely Handle and Move Parts and Equipment
- Rigging safety including load capacity (description and demonstration)
- Hoist inspection, determining if safe to use
- Manual and powered hoists (using cantilevered and gantry configurations)
- Calculating center of gravity for load balance
- Proper use of eyebolts for lifting parts
- Basic rigging techniques; types of slings, come-a-longs, blocking, chaining to lift a load
- Basic concepts of force, center of gravity, force vectors, rated load, and crush force
- Manual pry bar and truck to move a load
- Hydraulic jack to lift a load
- Dolly to move a load
- Proper containment methods to store a component
- Handling parts using proper containment prevention methods
- Components inspection (for contamination; to take corrective action)
- Troubleshooting Methodologies to Find Malfunctions in Machine Systems (to Return the System to Reliable, Productive Use in the Shortest Time Possible)
- Methodologies to isolate problems to a particular sub-system, 5-why, fishbone, flow charts, half-split method, etc.
- Effective interpersonal skills to interact with production personnel, vendors, and colleagues
- Effective observation and interview strategies to validate the problem and determine the most effective troubleshooting strategy
- Analyzing production information, maintenance, and operation documents to assist in troubleshooting a malfunction.
|
|