|
Apr 30, 2024
|
|
|
|
2023-2024 College Catalog [ARCHIVED CATALOG]
|
AVM 206 - Materials and Processes 3 Credits, 6 Contact Hours 1.5 lecture periods 4.5 lab periods
Introduction to non-metallic and metallic structural materials for comparison of their structural properties. Includes structural materials, metal processing, heat treatment, heat treatment of alloys or limited use metals, non-destructive testing/inspection, corrosion, corrosion types and factors, corrosion-prone areas, corrosion control: steel, aluminum, and limited use metals, processes and materials for corrosion control, aircraft cleaning, and aircraft cleaning agents.
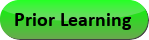.png)
Course Learning Outcomes
- Recall proficient knowledge of aircraft metal types and corrosion control processes
- Recall proficient knowledge in non-destructive testing and inspection
- Demonstrate proficiency in the hardware identification and common materials and processes
Outline:
- Aircraft Metals
- Property of Metals
- Ferrous Aircraft Metals
- Non-Ferrous Aircraft Metals
- Substitution of Aircraft Metals
- Metalworking Process
- Heat Treatment of Ferrous Metals
- Heat Treatment of Nonferrous Metals
- Straightening After Solution Heat Treatment
- Precipitation Heat Treating
- Annealing of Aluminum Alloys
- Heat Treatment of Aluminum Alloy Rivets
- Heat Treatment of Magnesium Alloys
- Heat Treatment of Titanium
- Hardness Testing
- Forging
- Casting
- Extruding
- Coldworking/Hardening
- Nonmetallic Aircraft Materials
- Wood
- Plastics
- Transparent Plastics
- Composite Materials
- Rubber
- Seals
- Packings
- Gaskets
- Wipers
- Sealing Compounds
- Aircraft Hardware
- Identification
- Threaded Fasteners
- Aircraft Bolts
- Aircraft Nuts
- Aircraft Washers
- Installation of Nuts, Washers, and Bolts
- Safetying of Bolts and Nuts
- Fastener Torque
- Aircraft Rivets
- Mechanically Expanded Rivets
- Special Shear and Bearing Load Fasteners
- Screws
- Riveted and Rivetless Nut Plates
- Hole Repair and Hole Repair Hardware
- Safetying Methods
- Safety Wiring
- General Safety Wiring Rules
- Cleaning and Corrosion
- Factors Affecting Corrosion
- Types of Corrosion
- Forms of Corrosion
- Common Corrosive Agents
- Common Corrosive Agents
- Inspection
- Corrosion Prone Areas
- Exhaust Trail Areas
- Battery Compartments and Battery Vent Openings
- Bilge Areas
- Lavatories, Buffets, and Galleys
- Wheel Well and Landing Gear
- Water Entrapment Areas
- Engine Frontal Areas and Cooling Air Vents
- Wing Flap and Spoiler Recesses
- External Skin Areas
- Electronic and Electrical Compartments
- Miscellaneous Trouble Areas
- Corrosion Removal
- Surface Cleaning and Paint Removal
- Fairing or Blending Reworked Areas
- Corrosion of Ferrous Metals
- Mechanical Removal of Iron Rust
- Chemical Removal of Rust
- Chemical Surface Treatment of Steel
- Removal of Corrosion from Highly Stressed Steel Parts
- Corrosion of Aluminum and Aluminum Alloys
- Treatment of Unpainted Aluminum Surface
- Treatment of Anodized Surfaces
- Treatment of Intergranular Corrosion in Heat-Treated Aluminum Alloy Surfaces
- Corrosion of Magnesium Alloys
- Treatment of Wrought Magnesium Sheet and Forgings
- Treatment of Installed Magnesium Castings
- Treatment of Titanium and Titanium Alloys
- Protection of Dissimilar Metal Contacts
- Contacts Not Involving Magnesium
- Contacts Involving Magnesium
- Corrosion Limits
- Processes and Materials Used in Corrosion Control
- Metal Finishing
- Surface Preparation
- Chemical Treatments
- Anodizing
- Alodizing
- Chemical Surface Treatment and Inhibitors
- Chromic Acid Inhibitor
- Sodium Dichromate Solution
- Chemical Surface Treatments
- Protective Paint Finishes
- Aircraft Cleaning
- Exterior Cleaning
- Interior Cleaning
- Powerplant Cleaning
- Solvent Cleaners
- Dry Cleaning Solvent
- Aliphatic and Aromatic Naphtha
- Safety Solvent
- Methyl Ethyl Ketone (MEK)
- Kerosene
- Cleaning Compound for Oxygen Systems
- Emulsion Cleaners
- Water Emulsion Cleaner
- Solvent Emulsion Cleaners One type of solvent emulsion cleaner
- Soaps and Detergent Cleaners
- Cleaning Compound, Aircraft Surfaces
- Nonionic Detergent Cleaners
- Mechanical Cleaning Materials
- Mild Abrasive Materials
- Abrasive Papers
- Chemical Cleaners
- Phosphoric-citric Acid
- Baking Soda
- Nondestructive Inspection/Testing
- Training, Qualification, and Certification
- Advantages and Disadvantages of NDI Methods
- General Techniques
- Visual Inspection
- Eddy Current Inspection
- Principles of Operations
- Eddy Current Instruments
- Ultrasonic Inspection
- Ultrasonic Instruments
- Reference Standards
- Inspection of Bonded Structures
- Types of Defects
- Acoustic Emission Inspection
- Magnetic Particle Inspection
- Magnaglo Inspection
- Radiographic Inspections
- Inspection of Composites
- Tap Testing
- Electrical Conductivity
- Thermography
- Inspection of Welds
Effective Term: Fall 2023
|
|